Every Day Carry Tray
Click here to subscribe to my YouTube channel.
Who doesn't love a nice every day carry tray. I really like ovals for the shape of these type of trays. For this tutorial I am going to show you how to design a simple oval tray in Inventables Easel Pro software and then make 3 oval shaped trays using three different types of wood blanks.
20 degree veneer tray
Wavey veneer tray
Straight veneer tray
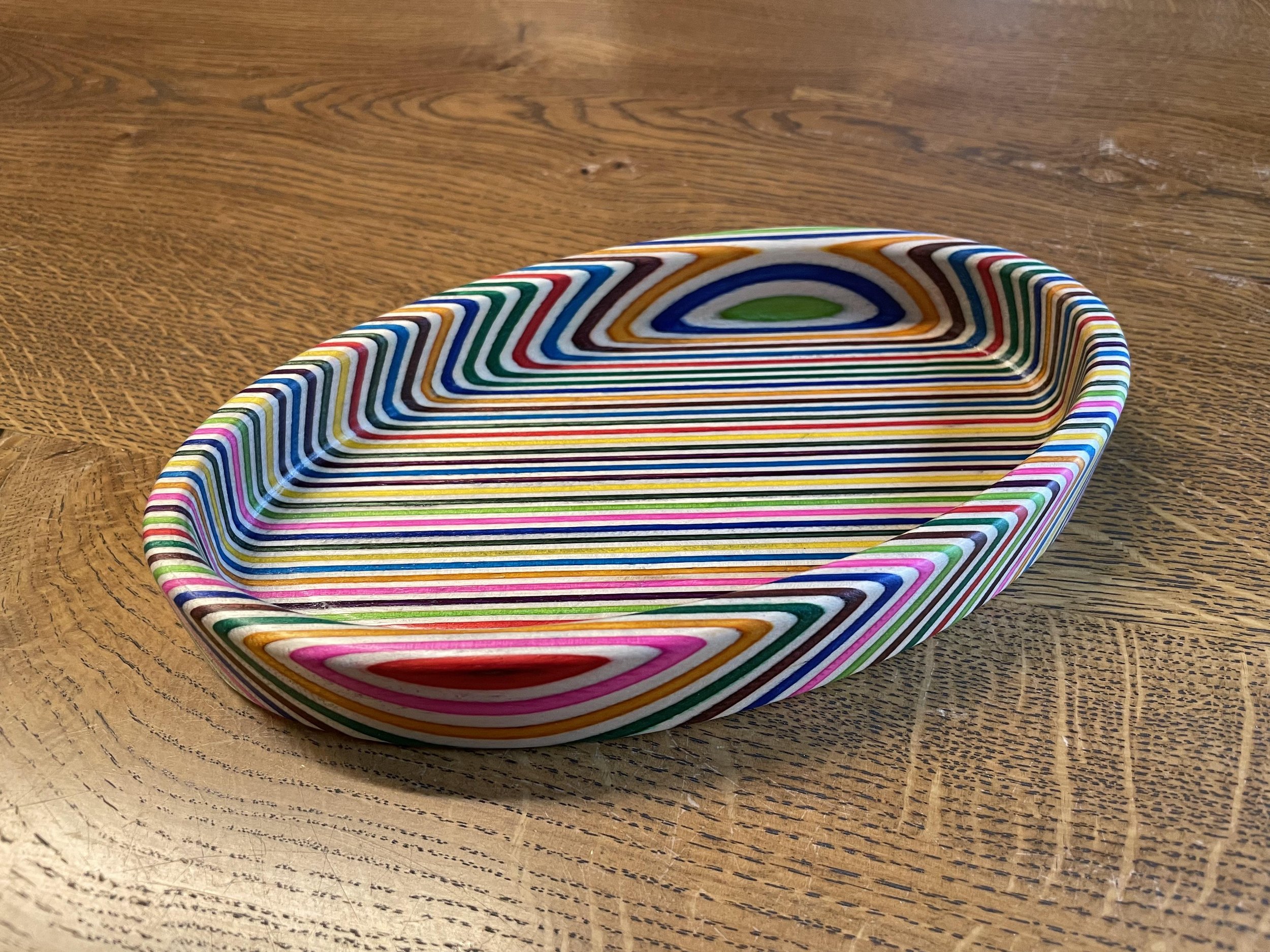
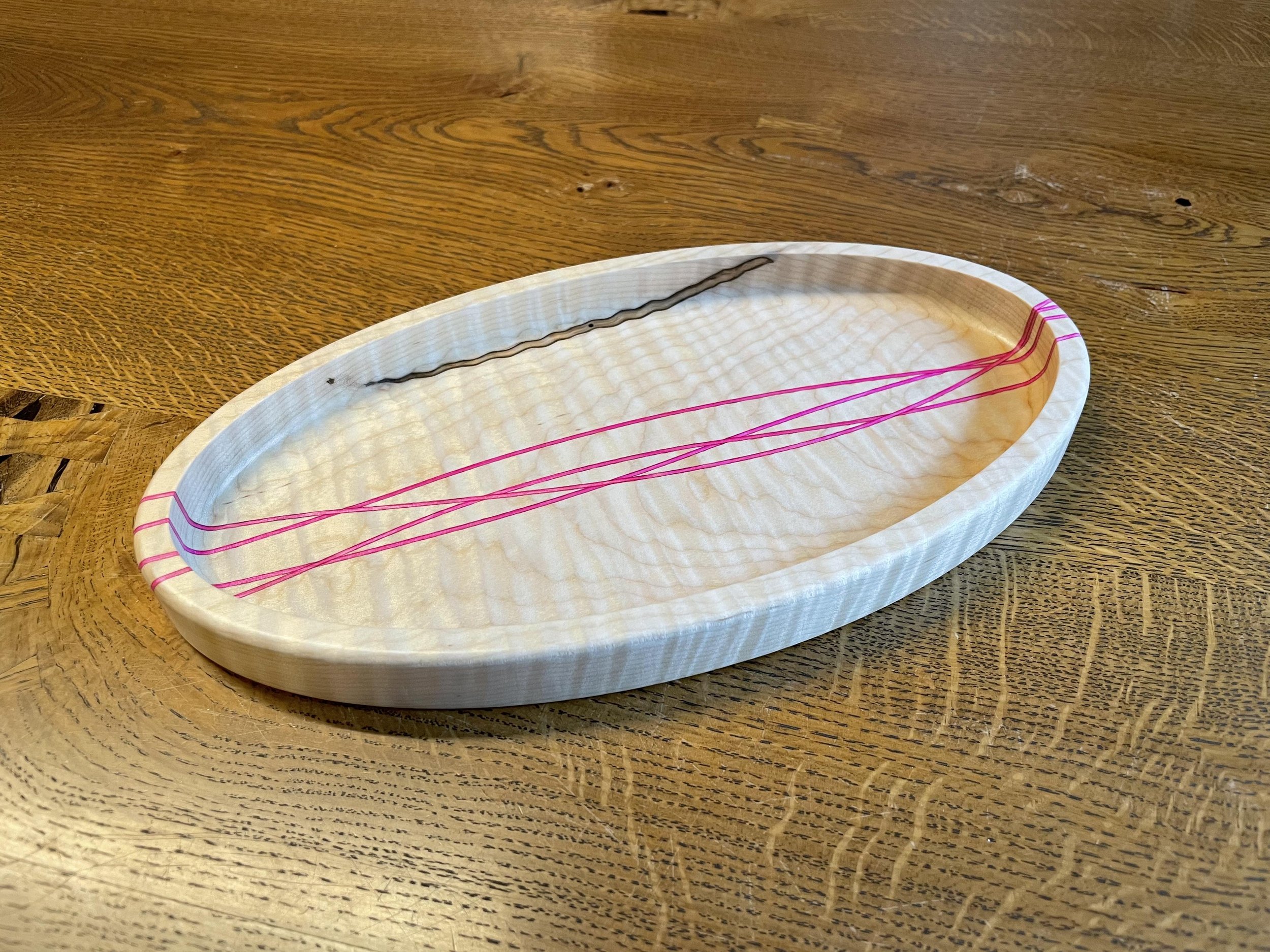
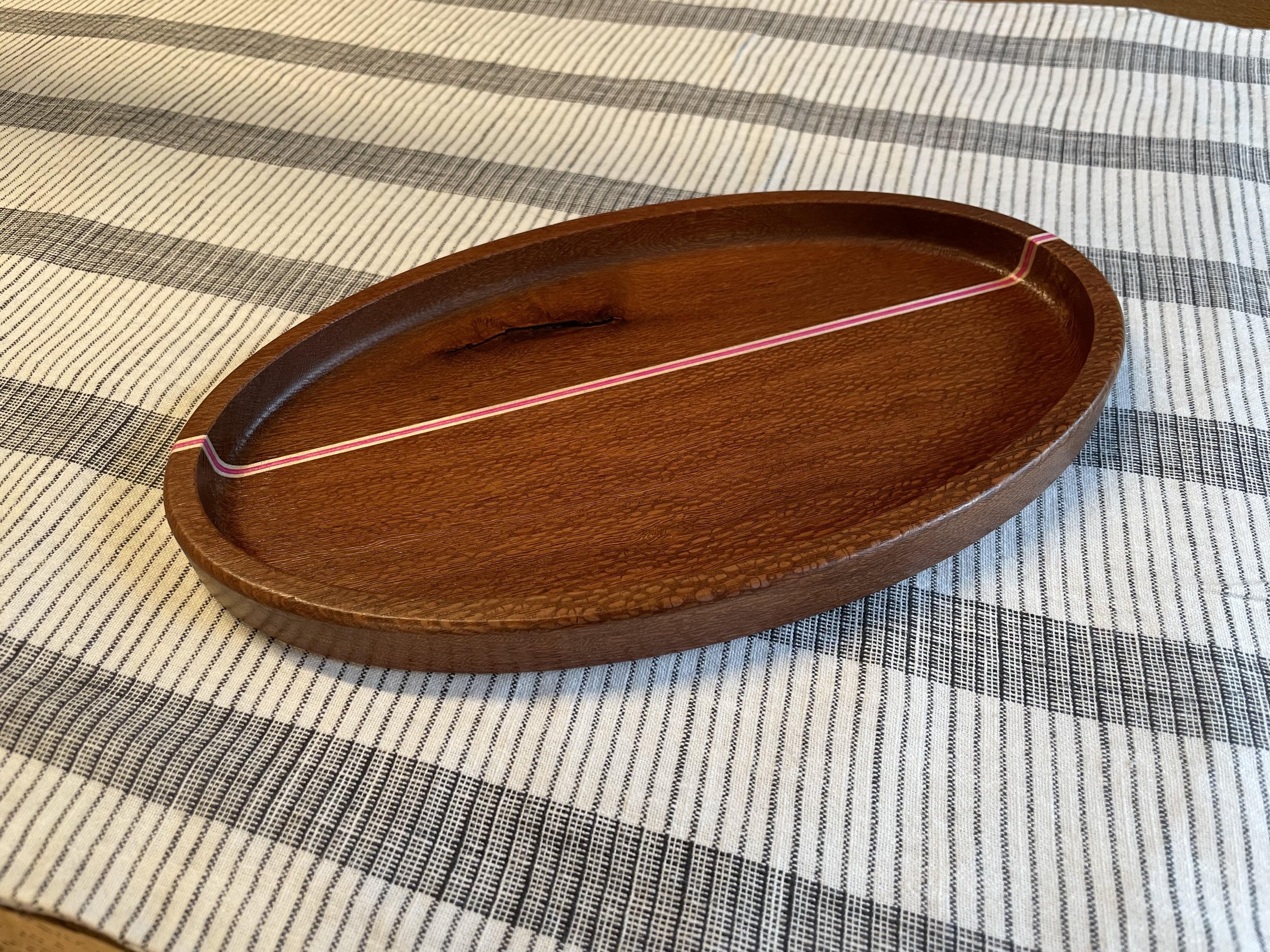
Step 1: Tools and Materials
SOFTWARE
Easel Pro Software by Inventables - https://www.inventables.com/technologies/easel?ref=MakingAtHome
MATERIALS
Dyed skateboard veneer or wood of your choice
I get my skateboard veneer from Cousineau Wood Products - https://www.cwp-usa.com/collections/dyed-veneer-sheets
TOOLS
The tools I used on the project were as follows:
X-Carve 1000mm CNC Machine by Inventables - https://www.inventables.com/technologies/x-carve?ref=MakingAtHome
1/4" diameter downcutting bit - https://amzn.to/3zJALbi
1/8" radius roundover bit with guide bearing
1/2" diameter 1/8" radius bowl and tray bit - https://amzn.to/3wOe187
Saw Stop table saw - https://amzn.to/3a8znCE
Grizzly 14" Band Saw
12" Planer - https://amzn.to/3Hw5XxI
Random orbit sander
Shop vac
Parallel clamps
Tape Measures (my favorite two):
Fastcap PMS-16 Auto Lock ProCarpenter Tape Measure - https://amzn.to/333fTMN
or FastCap PSSR16 16 ft Standard Reverse Measuring Tape - https://amzn.to/35eQe6k
2" diameter sanding discs - https://amzn.to/3xik2cC
XFasten Double Sided Woodworking Tape - https://amzn.to/3lfCDUk
Minwax 15210 Clear Aerosol Spray Lacquer - https://amzn.to/3yayIvL
NOTE: As an Amazon Associate I earn from qualifying purchases.
NOTE: If you plan on using any tool for a project please make sure you are familiar with the tool and all of the dangers associated with it. If you are not familiar with a tool then you should ask someone who is to show you the proper way to use it. A lot of communities have classes at local colleges on the proper use of tools and machinery. There are also local woodworking clubs that offer classes at very reasonable rates for beginners. I highly recommend using these resources for your safety and for the most efficient use of the tool.
SAFETY FIRST
Always wear eye and hearing protection.
Always work safe with the proper safety equipment and guards on your tools.
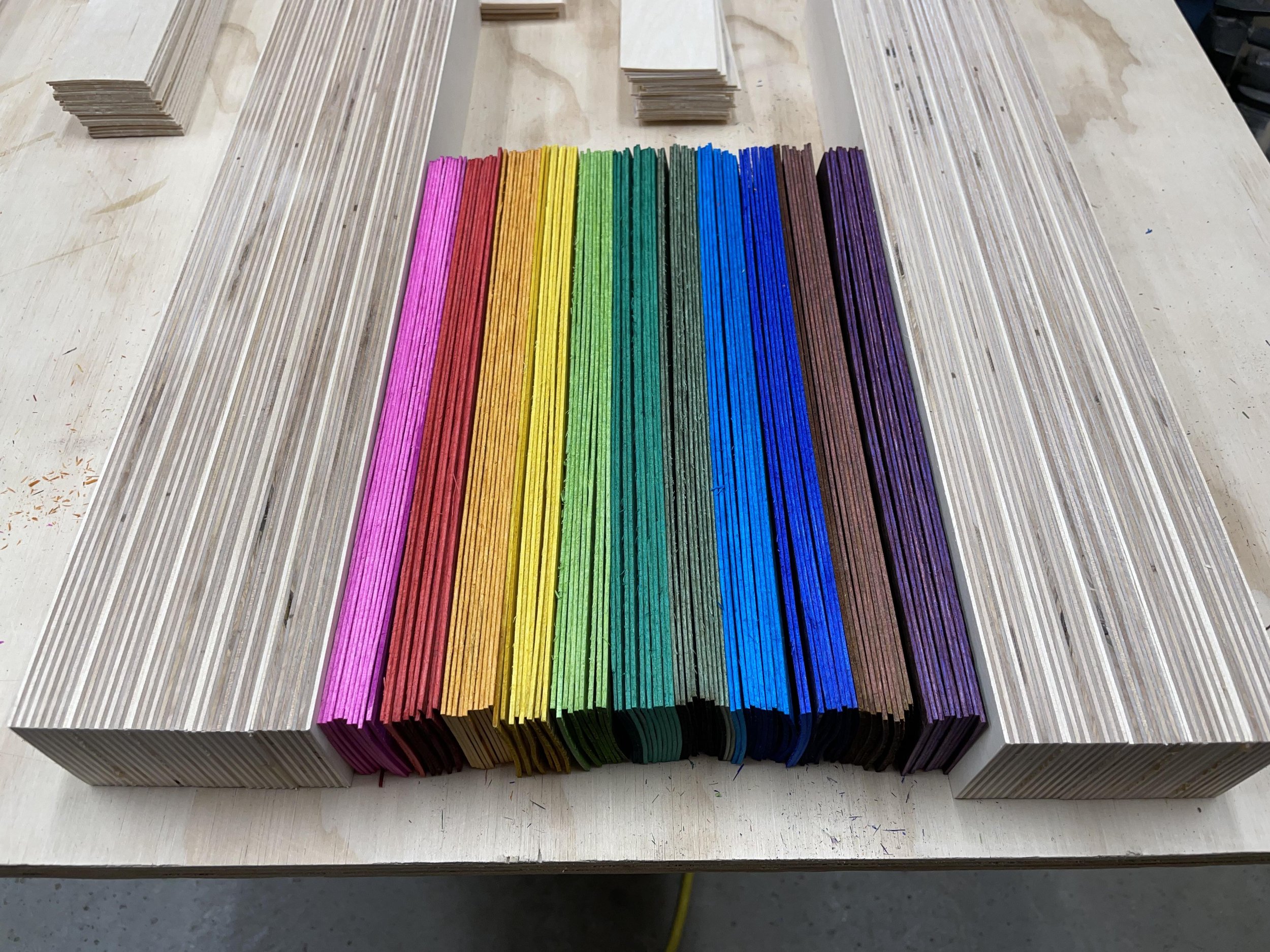
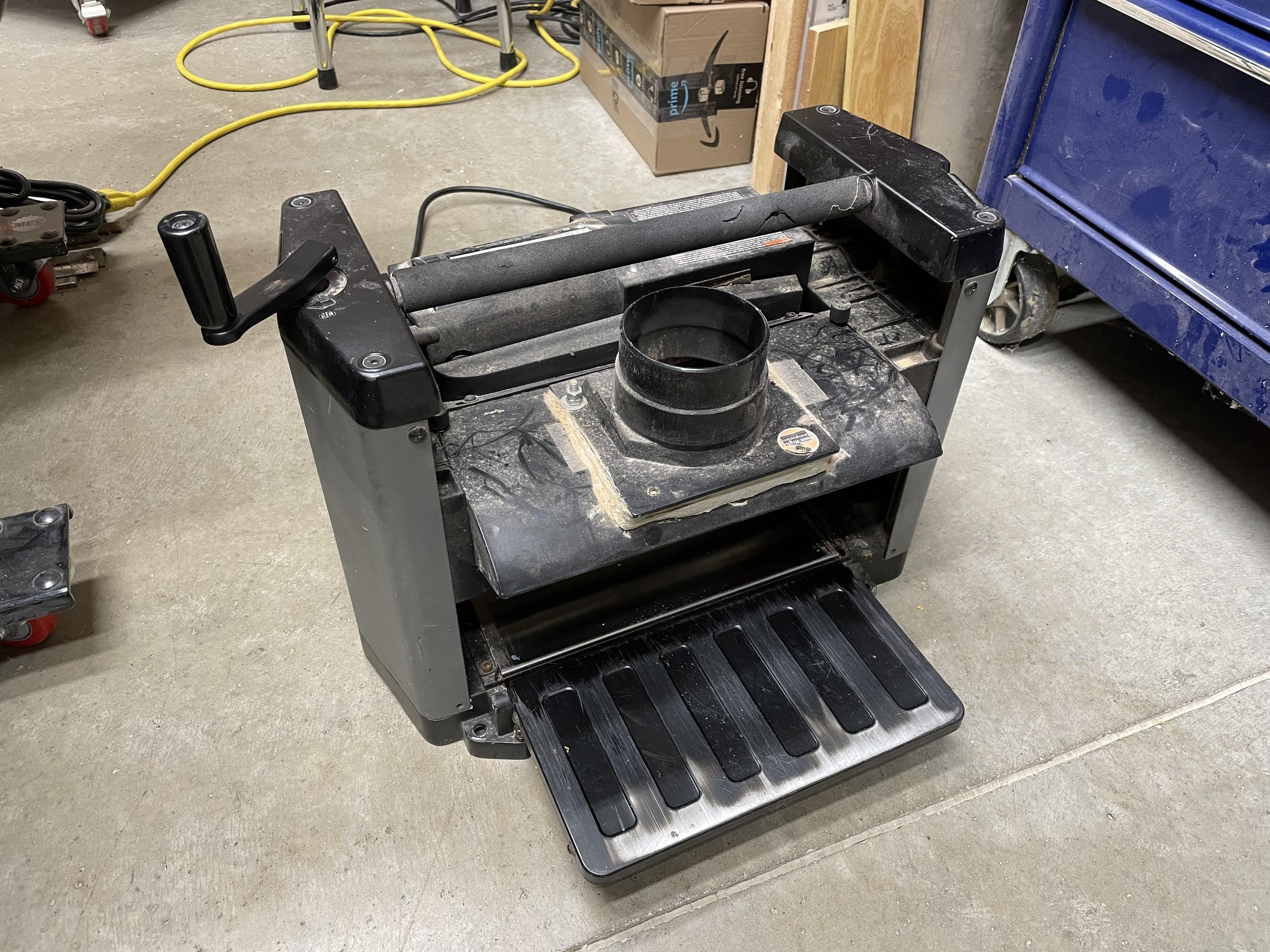
Step 2: Tray Design
To create the oval shape you can select the oval circle tool and place it on the work piece. I then grab the grips on the selected piece and pull those around until I have the shape that I like.
You can make this shape as large as the piece of wood you are going to carve getting right out to the edges. Once you have the outline of the shape you will need to offset that shape to the inside to create the inside edge of the tray. I like to have a 3/8” thick edge as that gives me enough width to cut a 1/8” radius roundover on the inside and outside of the tray edge if the tray itself is deep enough.
To create the offset, make sure you have the oval shape selected and then go into the apps menu in the Easel software. I always use the version 2 of the offsetter app. Select the options for offsetting to the inside, just make on instance, and set the distance to offset at 3/8”.
Once you select OK, you will see a new oval has been added to your work area. Select the inside work piece and set the cut setting to carve out a pocket. Set the outside piece to carve to the outside.
Now we have the two pieces of the tray, but we need to set them up into two separate carving operations. I like to carve the inside of the trays using a bowl bit so the tray has an inside radius in the inside corner. This makes it easier to sand and finish the inside edge of the tray. The bit I used for these was the Amana Tool 45983 Carbide Tipped Bowl & Tray bit. It has a 1/8" radius which makes a nice inside corner on the trays.
I take this master design page and duplicate it several times. The first duplicate page I make I delete the tray outline and use this for the tray carving operation. The second duplicate page I make I delete the tray carving section (center) and leave the outline cut.
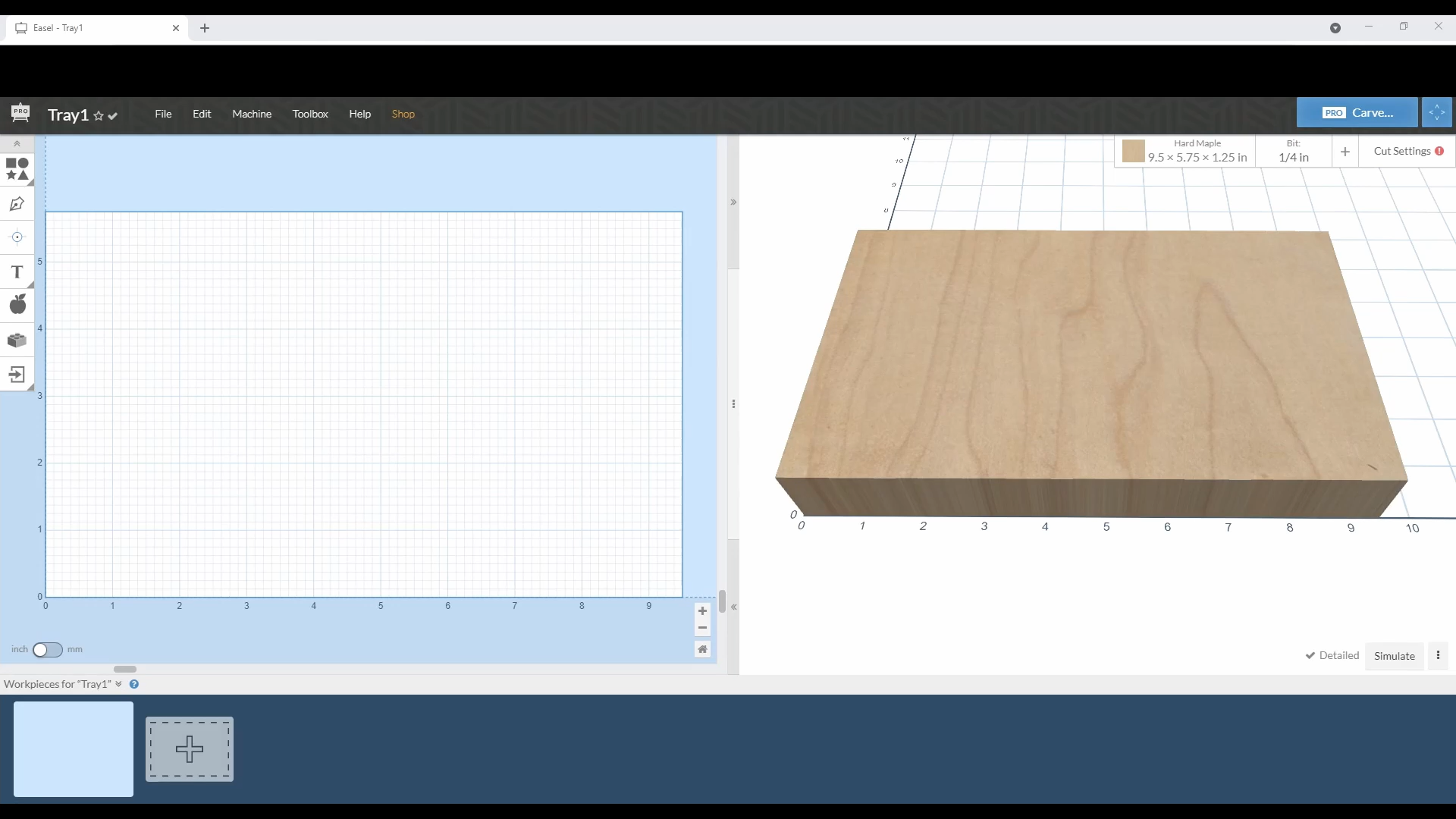
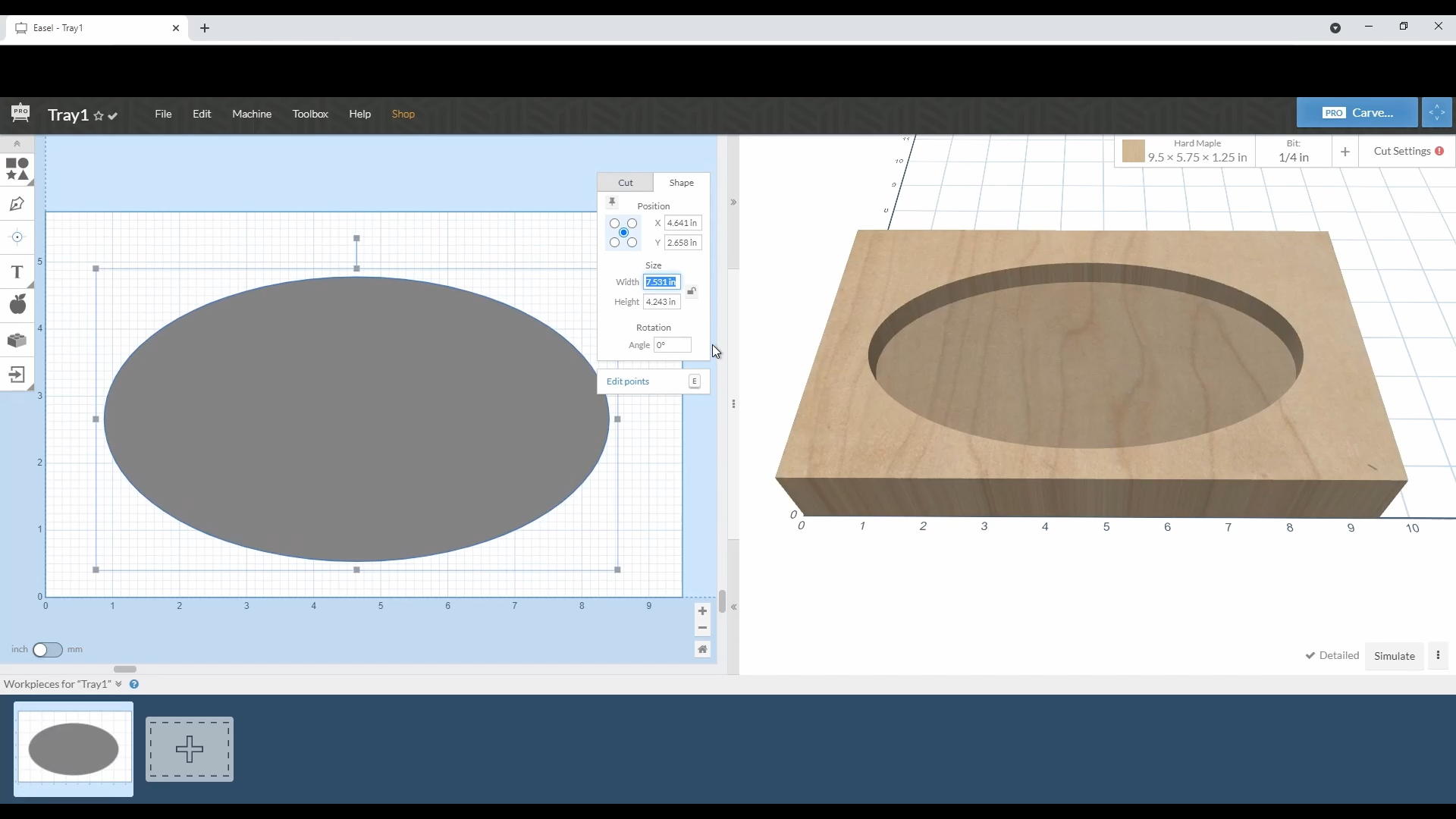
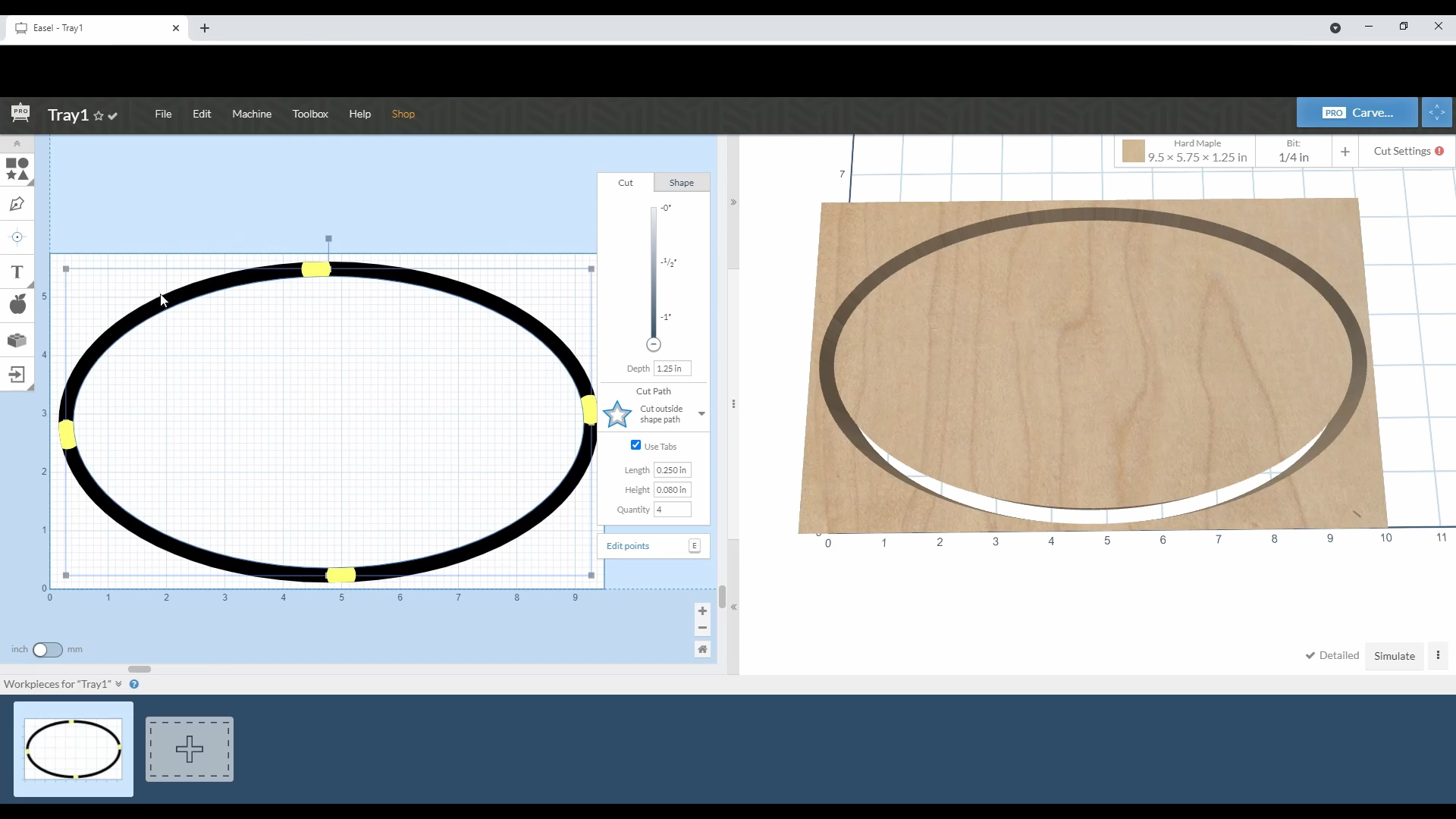
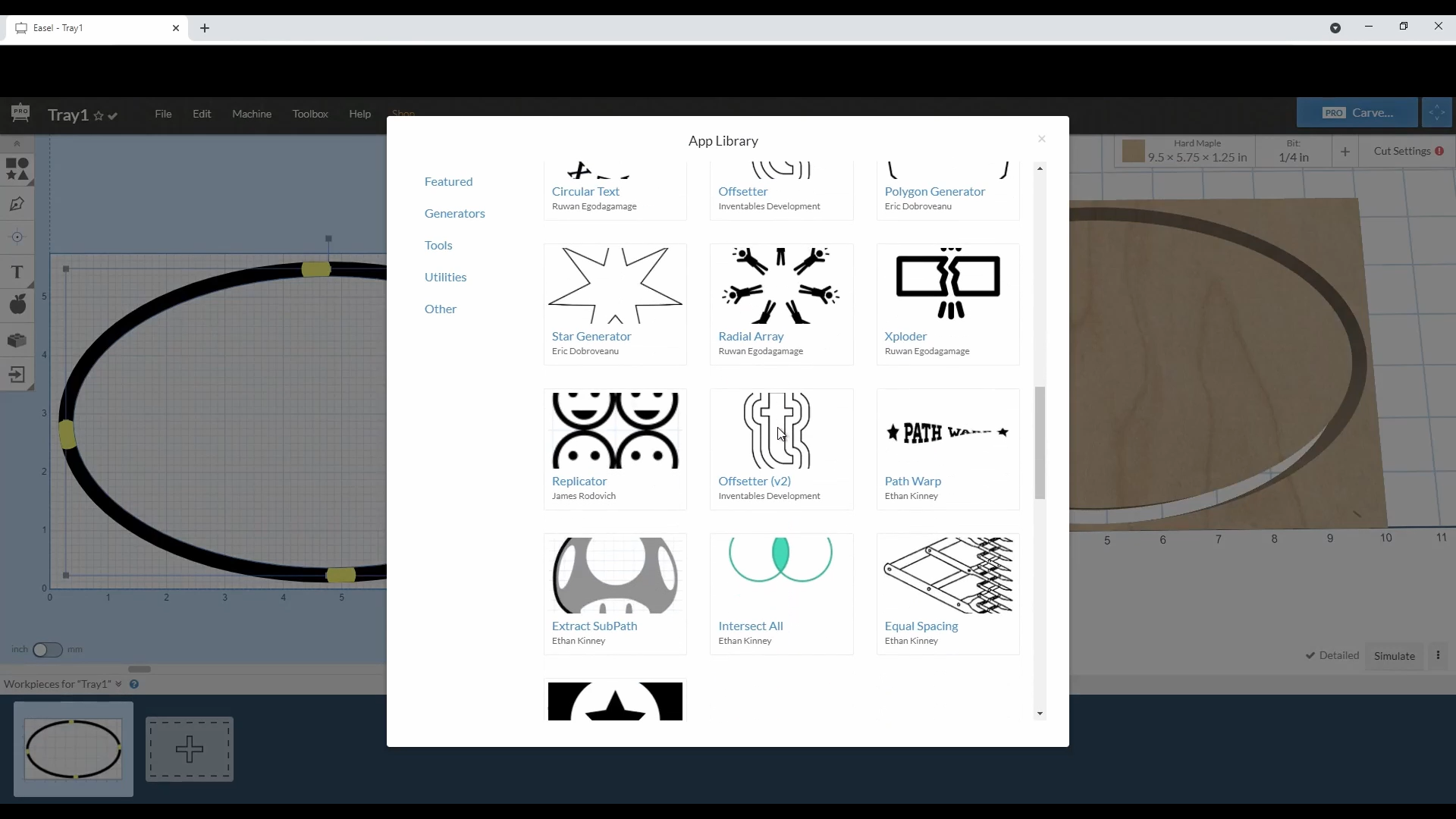
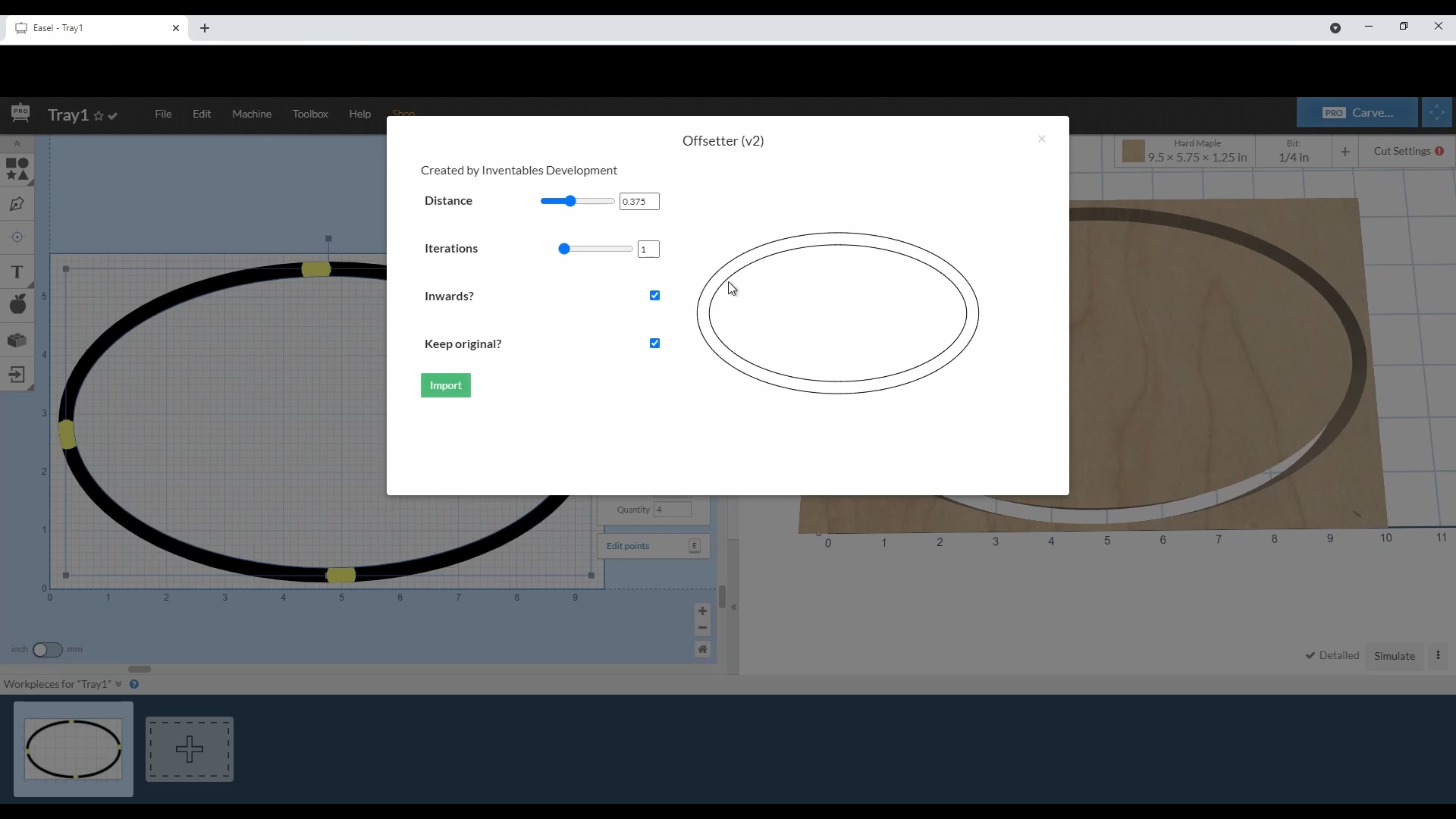
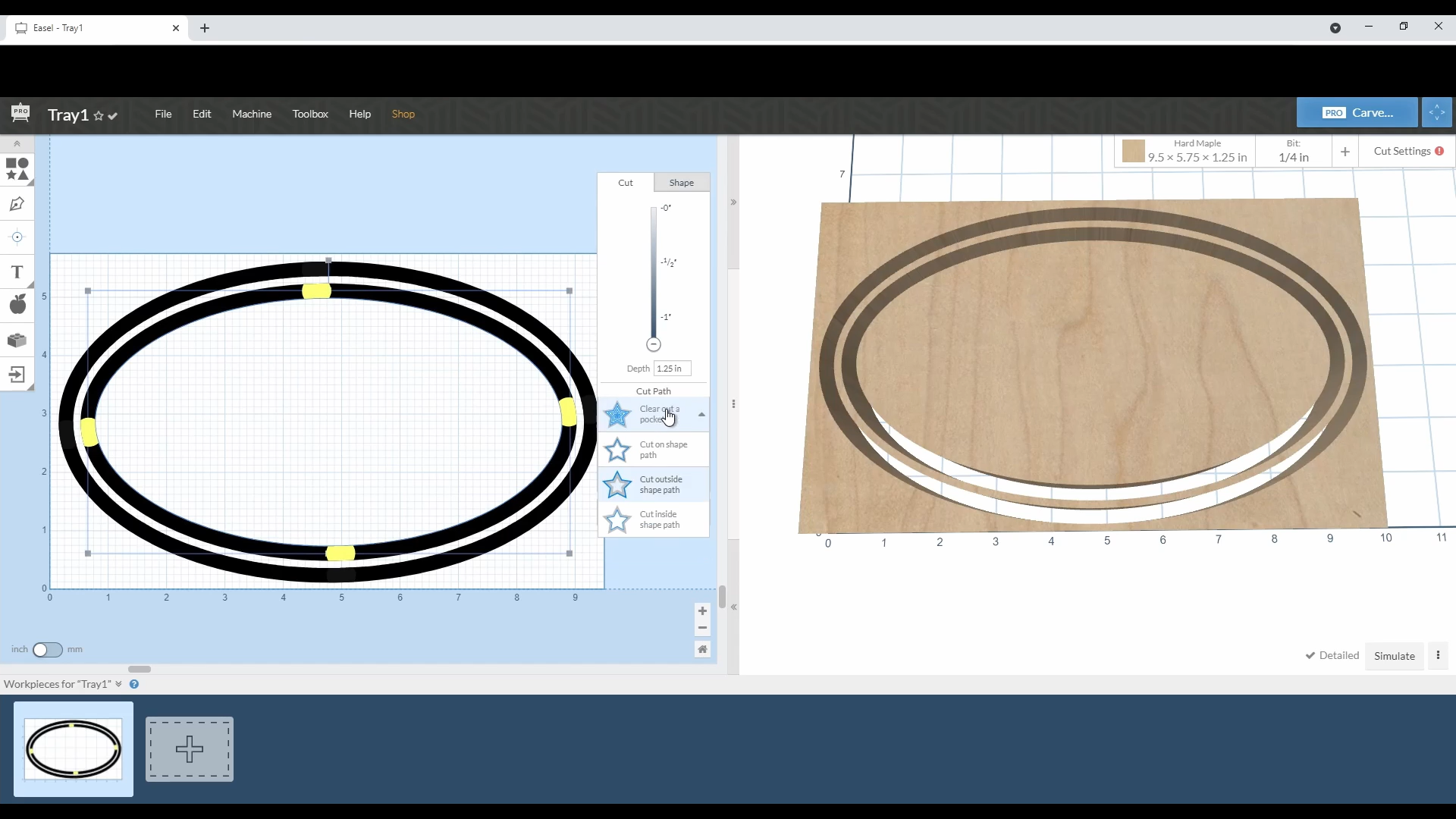
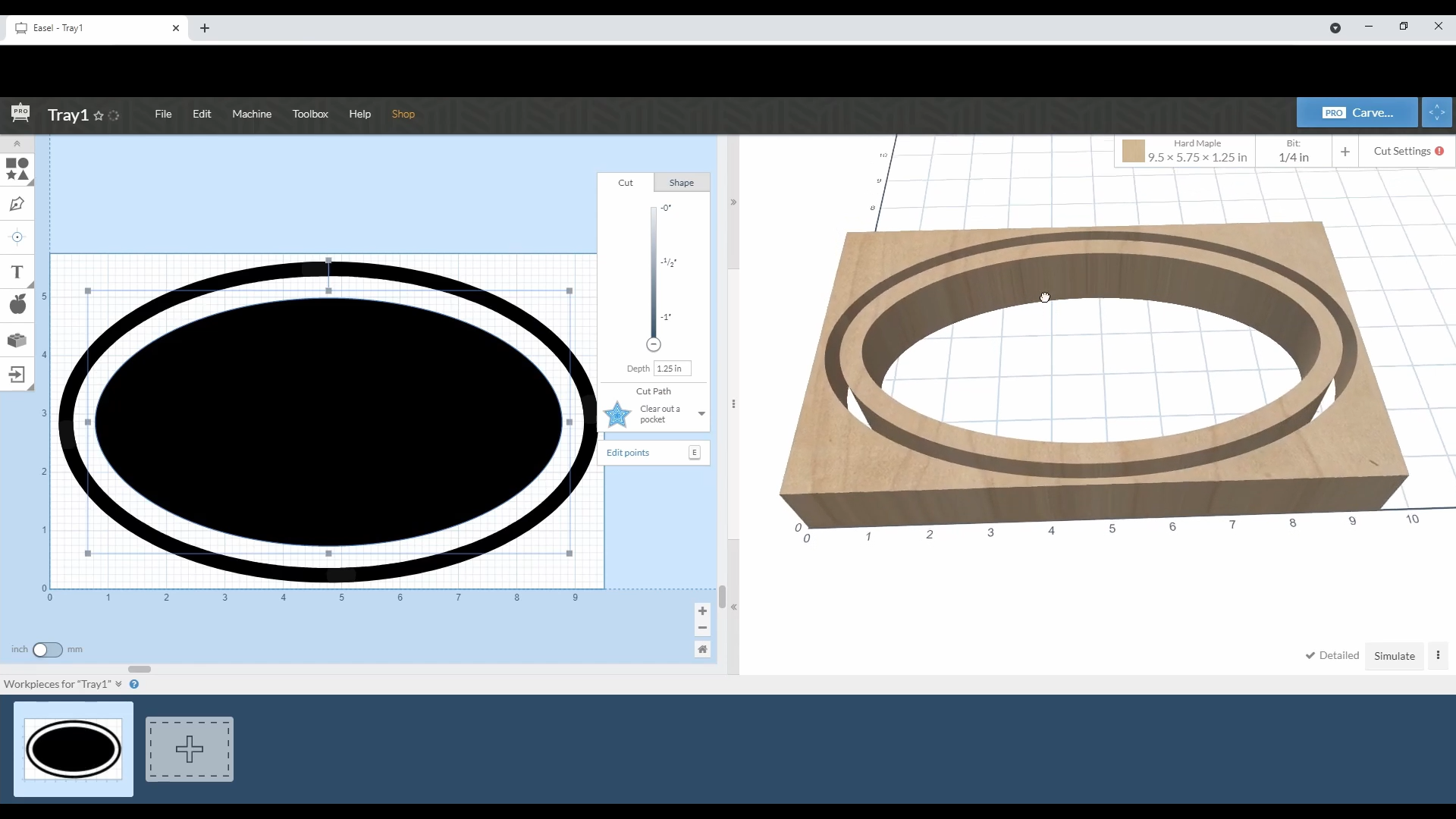
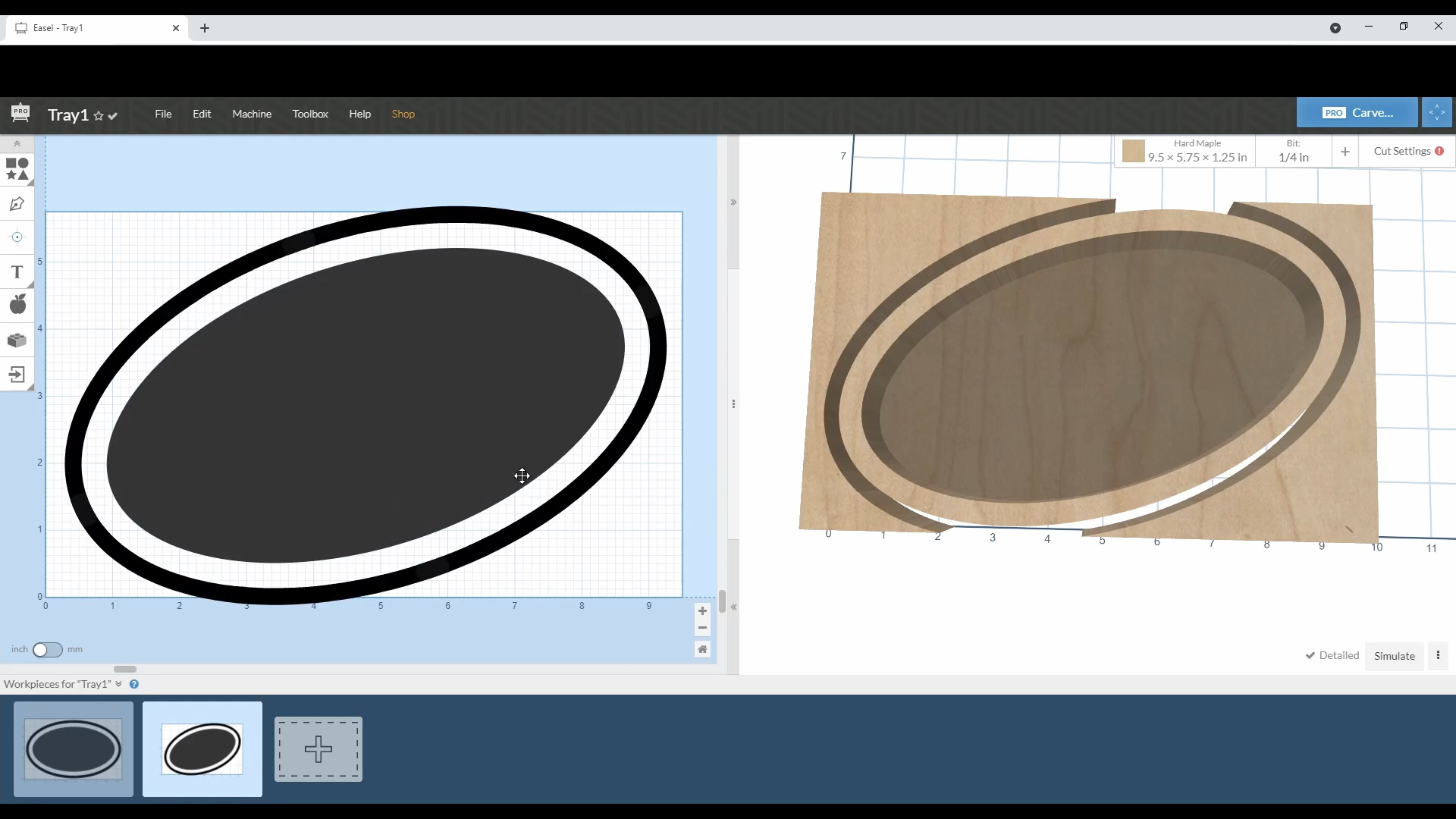
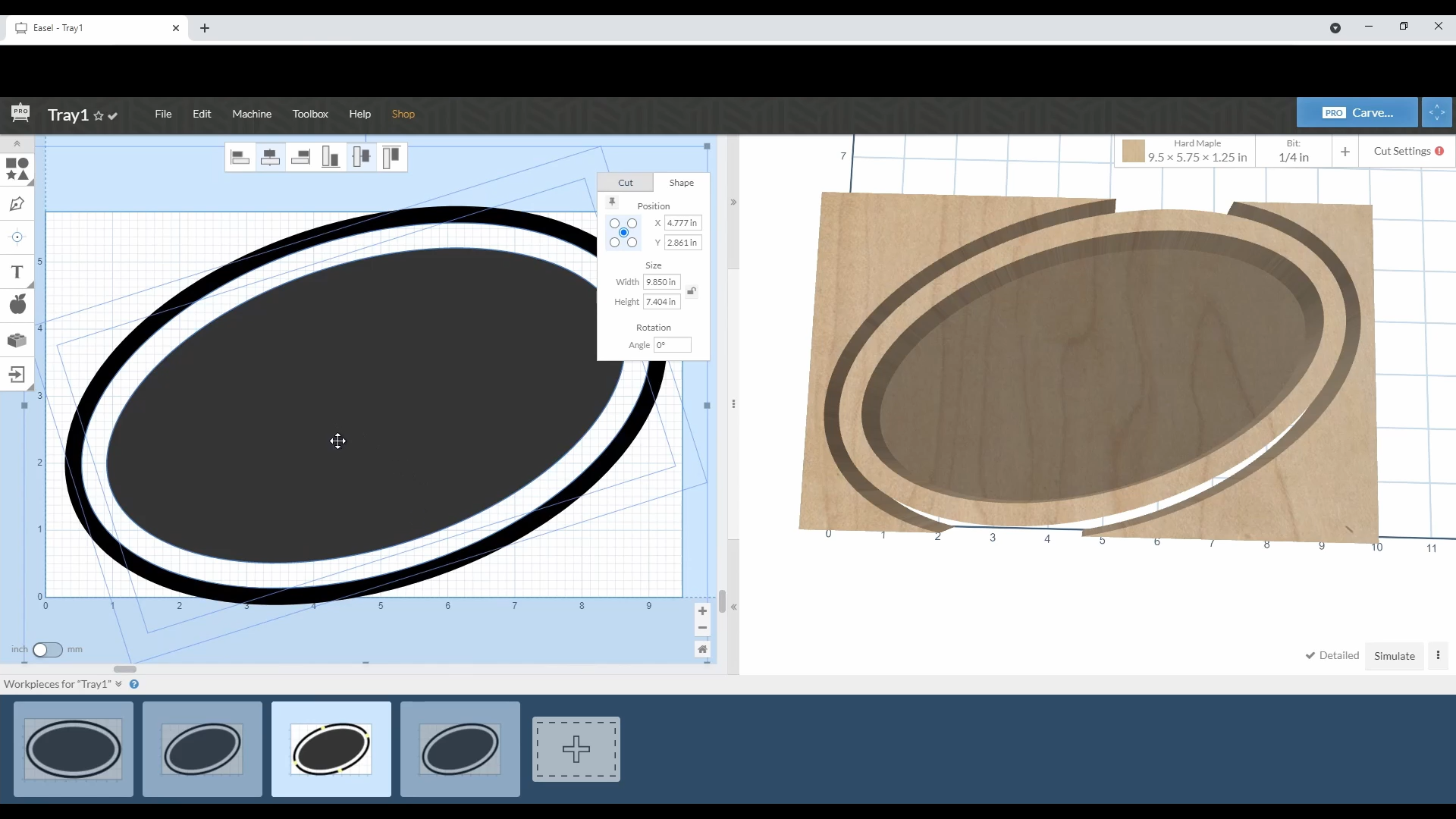
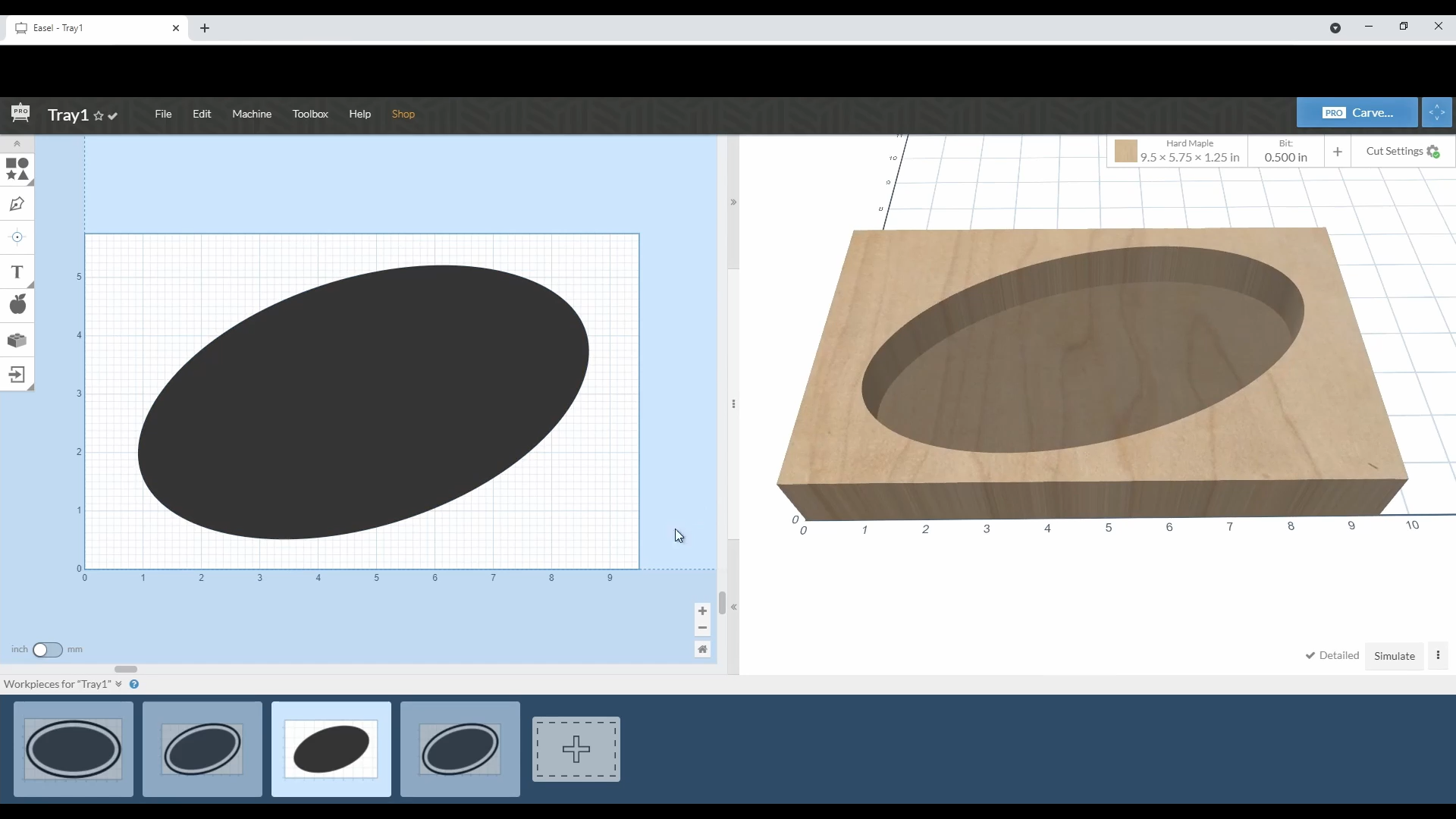
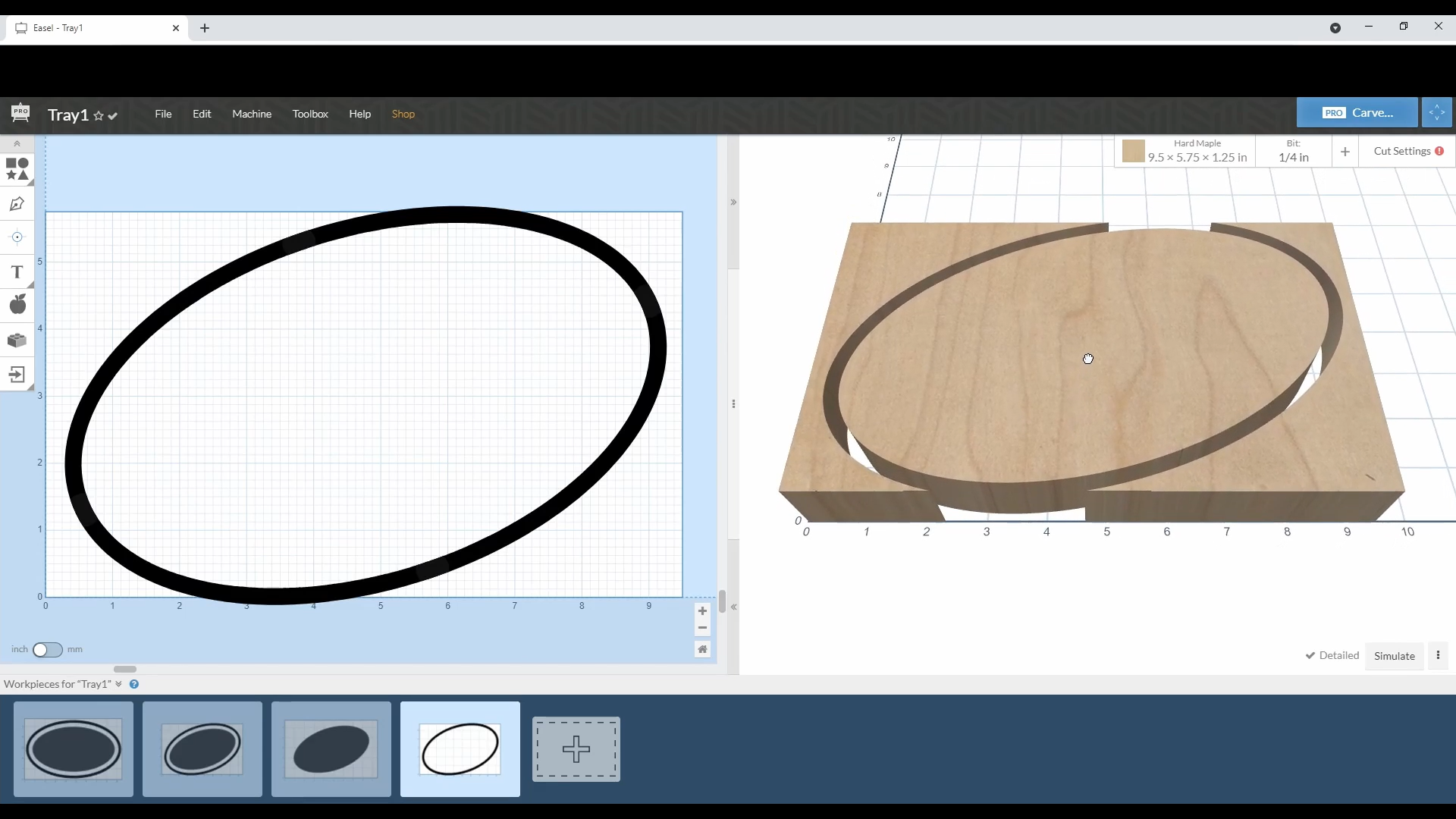
Step 3: 20 Degree Veneer Tray
We are now going to make 3 types of wood blanks to carve similar trays out of and compare how they look. We are going to make the following trays:
20 degree Veneer Tray
Wavey Veneer Tray
Straight Veneer Tray
I thought it would be fun to make some trays that are almost identical in shape, but different in composition so we can see how different they look once completed.
20 Degree Veneer Tray
Creating the Cauls
To glue pieces of veneer together at 20 degrees, I needed to make a couple pieces of wood that would hold them at this angle. These clamping cauls also help distribute the clamping pressure on the pieces of veneer.
To make these I glued several pieces of veneer together and then ripped them in half at 20 degrees on the table saw. I marked the pieces so they would be used in the clamping process in the same way they were glued together. This helps keep the glue up nice and square.
I added packaging tape to the face of the wood that was going to be pressing against the veneer so glue cleanup would be easy.
Cutting the Veneer Strips
The veneer I used for this project came from Cousineau Wood Products and is made for making skateboards. It comes in 10” wide strips that are 41” long and 1/16” thick. To cut it into strips to be glued together I first cut off a piece of veneer that was a little longer than the wood blank I wanted to make.
Note that the edges do not have to be perfect on these strips as we will be running these through a planer to get a nice smooth surface. This process will remove the rough edges. The strips of wood that I cut were 2” wide. For perspective, the final wood blanks I had to cut on the X-Carve CNC were 1.25” thick.
Veneer glue up in sections
Gluing up the veneer pieces is fairly easy. You just want to take your time and have all of your materials ready. This process does use a lot of wood glue so you should have a little more than you anticipate ready to use. One thing I found that makes this process faster and more enjoyable is using a glue roller like the one you will see in the video. This one is manufactured by Rockler. As you squeeze the glue from the bottle the glue gets spread out over the strips of veneer.
I used Titebond Original wood glue for these and if you have used it before you know you really only have about 8 to 10 minutes before the glue starts tacking up. For that reason I split the overall glue up of the veneer sections into multiple pieces. I found that I could glue enough pieces together to make a piece up to 1-3/8” thick. I made multiple pieces this size and then glued those sections together to get the overall wood blank.
Carving
Next I go through the carving operation. I carve the tray recess out first using the bowl bit. Then I switched to a 1/4" downcutting spiral bit and cut the outline of the tray. Since I am using double sided CNC tape I did not use tabs for the cutting process when cutting the outline.
Rounding the Edges
After carving on the CNC I rounded the edges of the trays using a router table with a 1/8" radius roundover bit with a guide bearing. When the trays are deep enough I round over the inside and outside edges of the top and the bottom edge as well.
If the tray is not deep enough to allow the inside edge of the top to be rounded over with the router bearing conflicting then I just do the roundover on the outside edge.
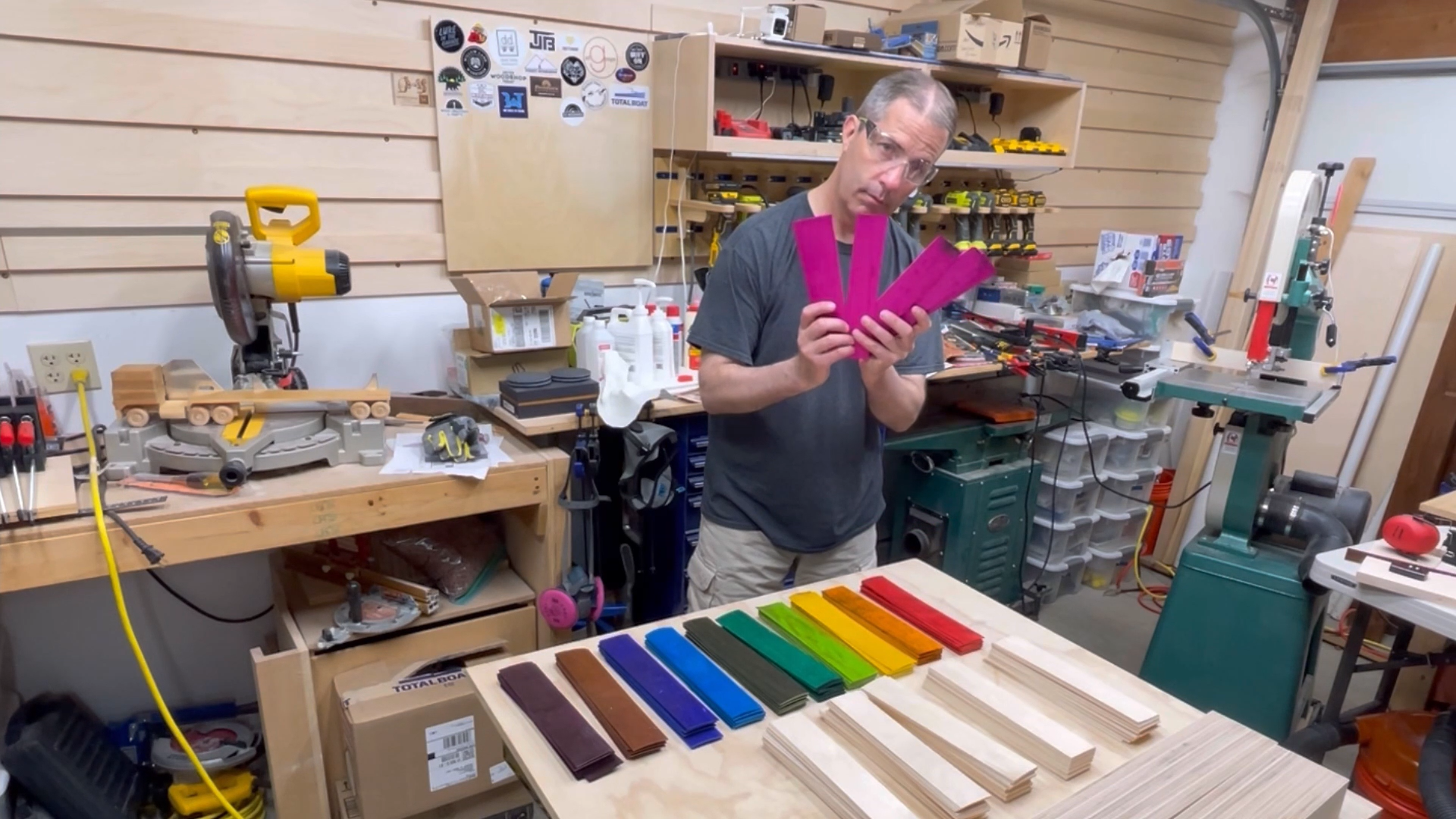
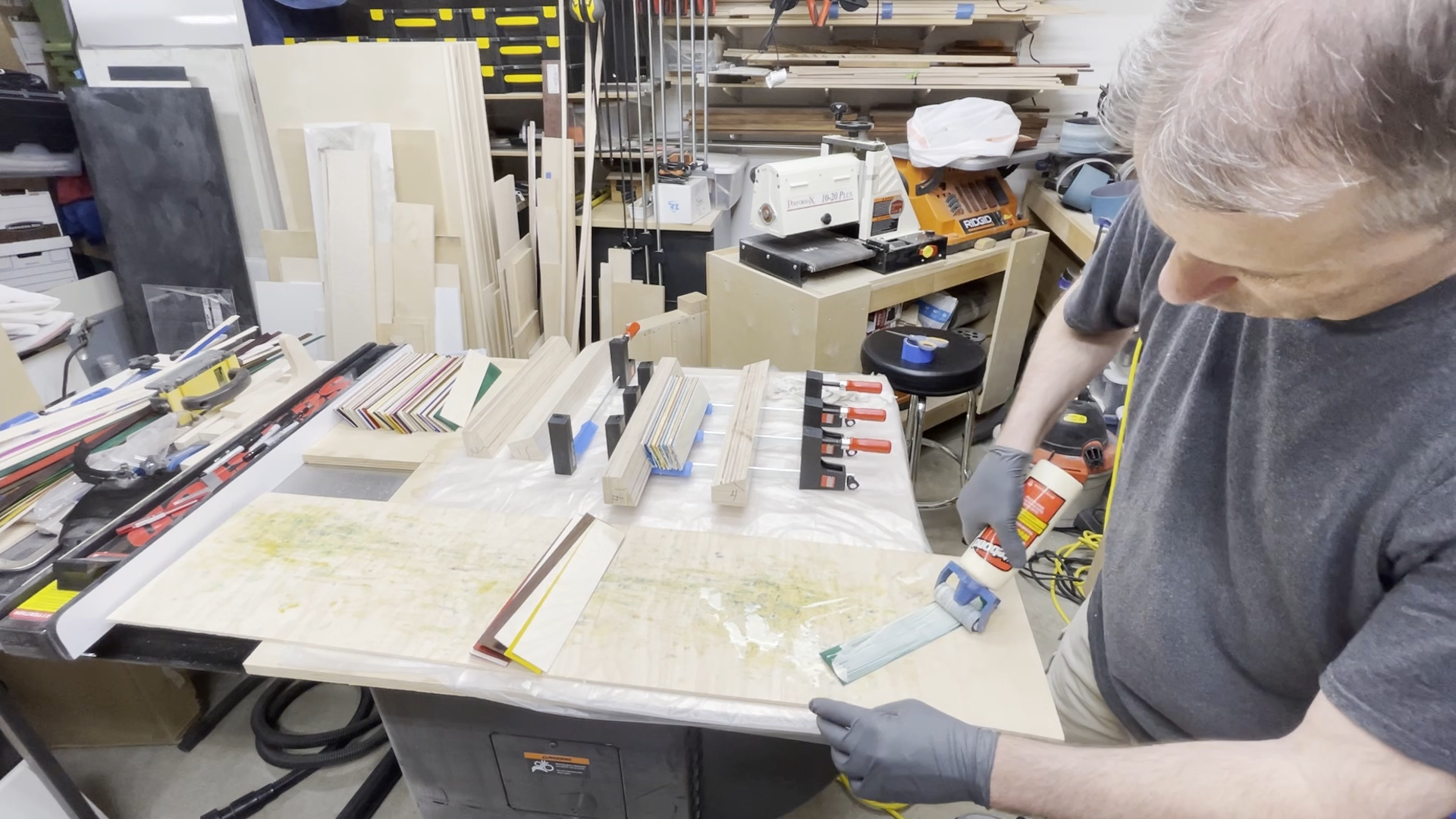
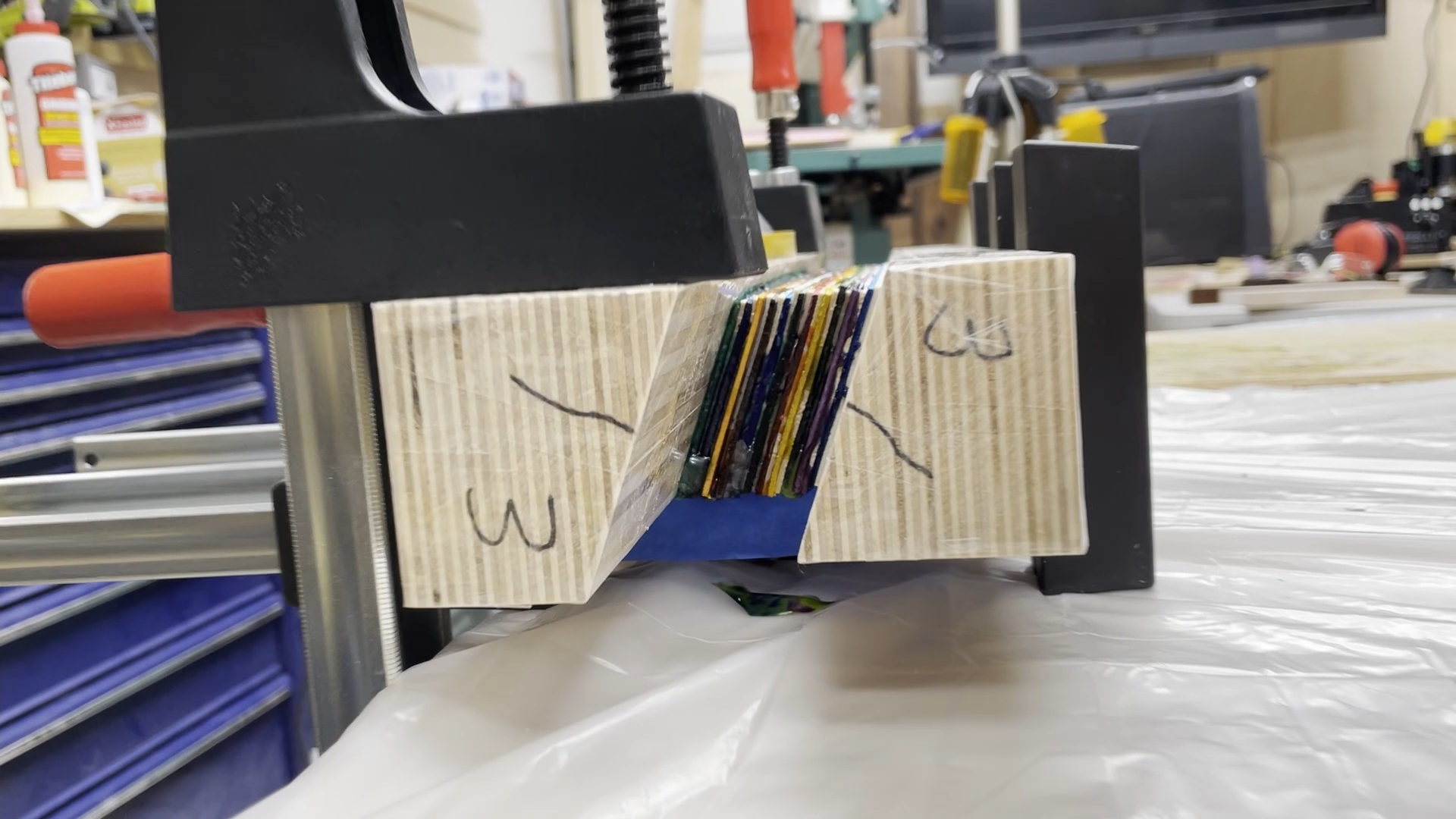
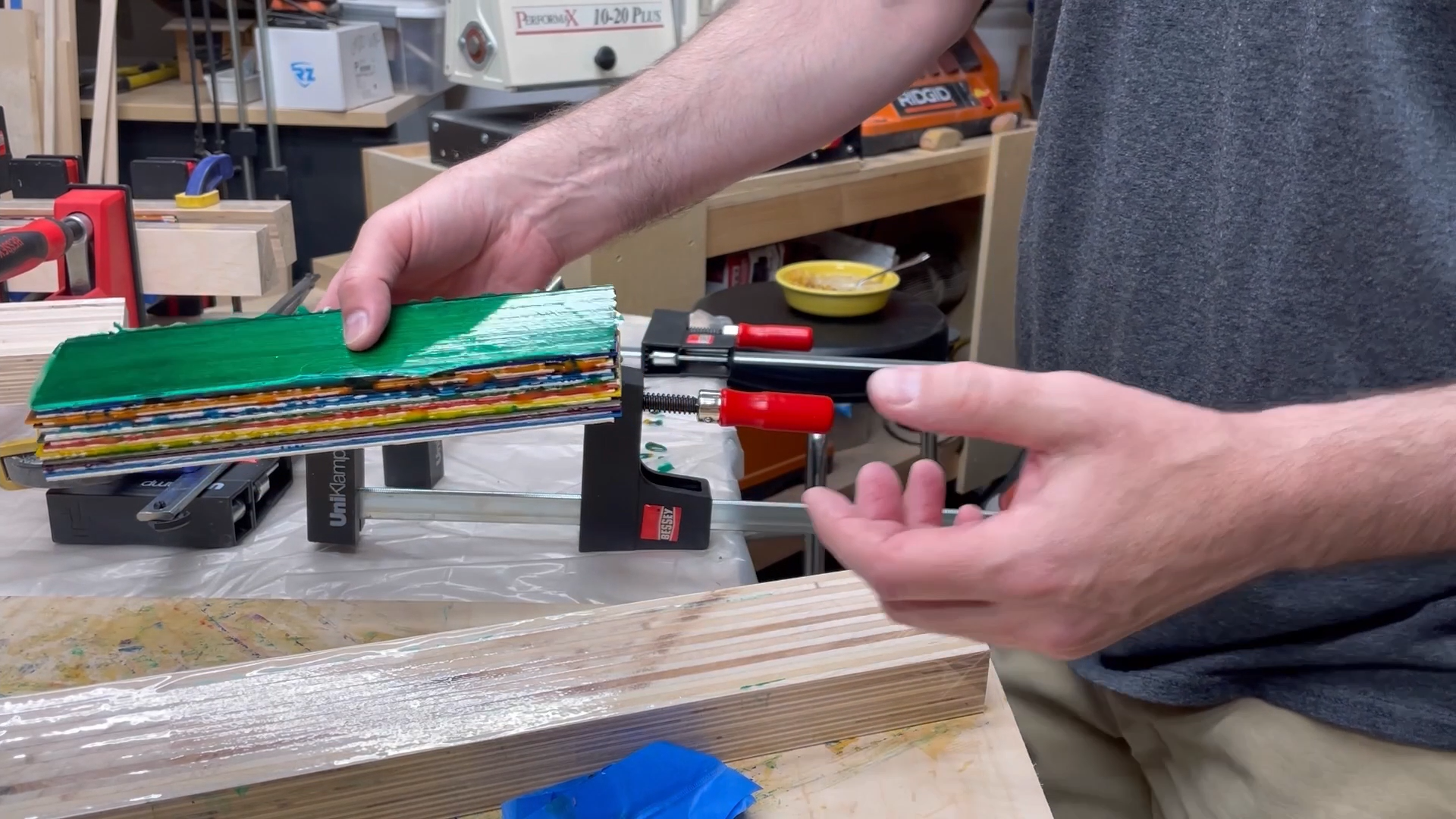
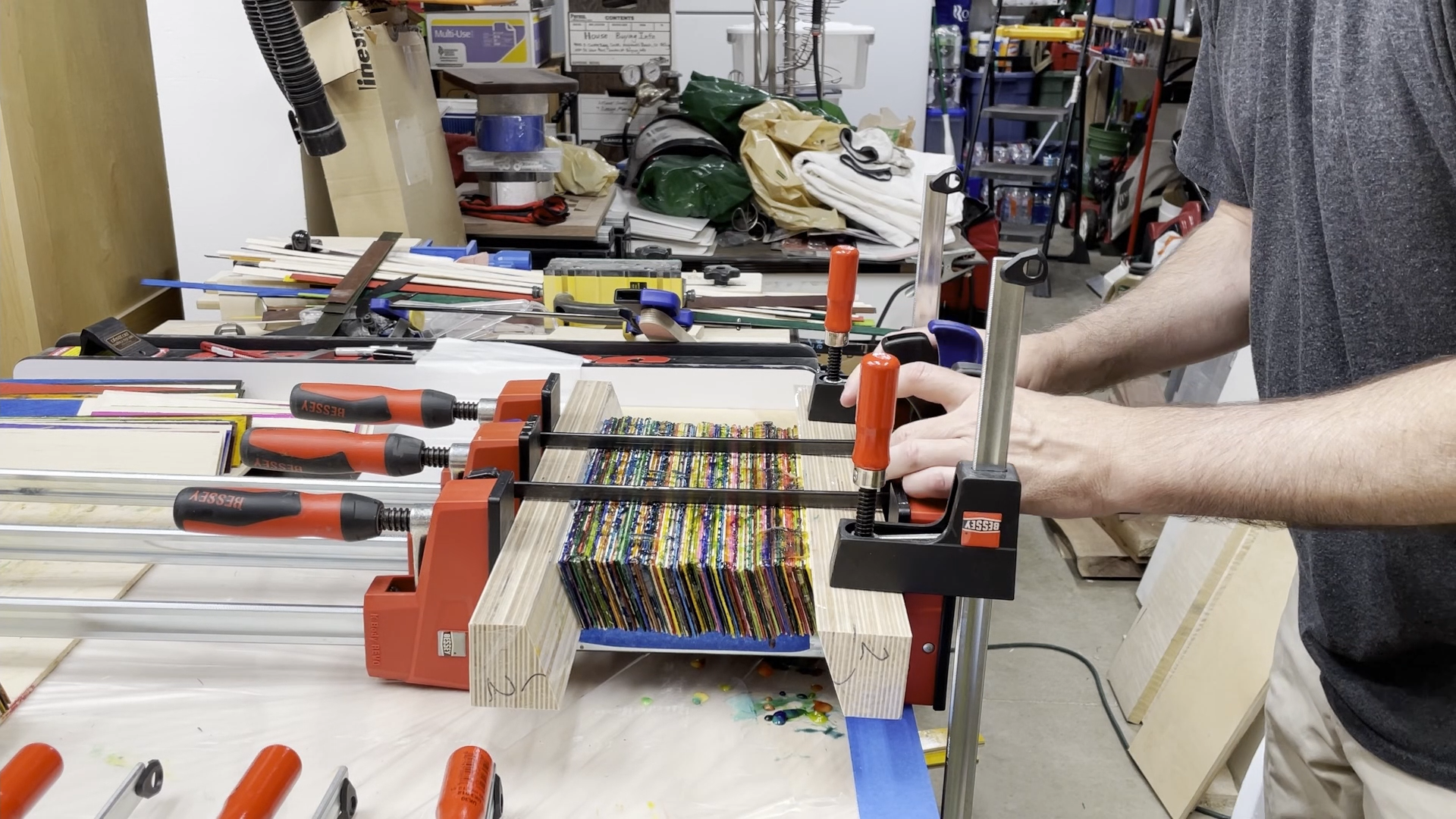
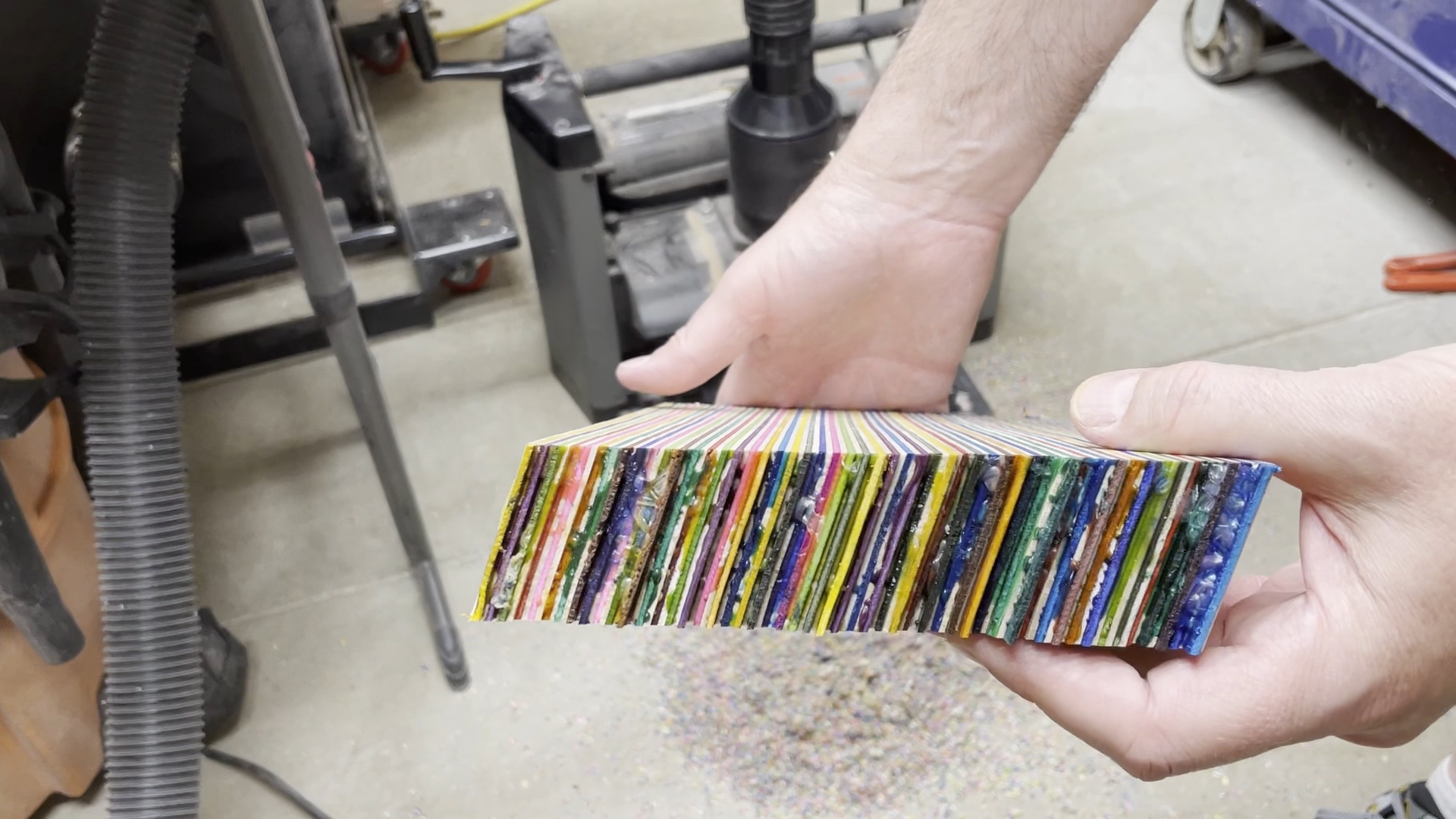
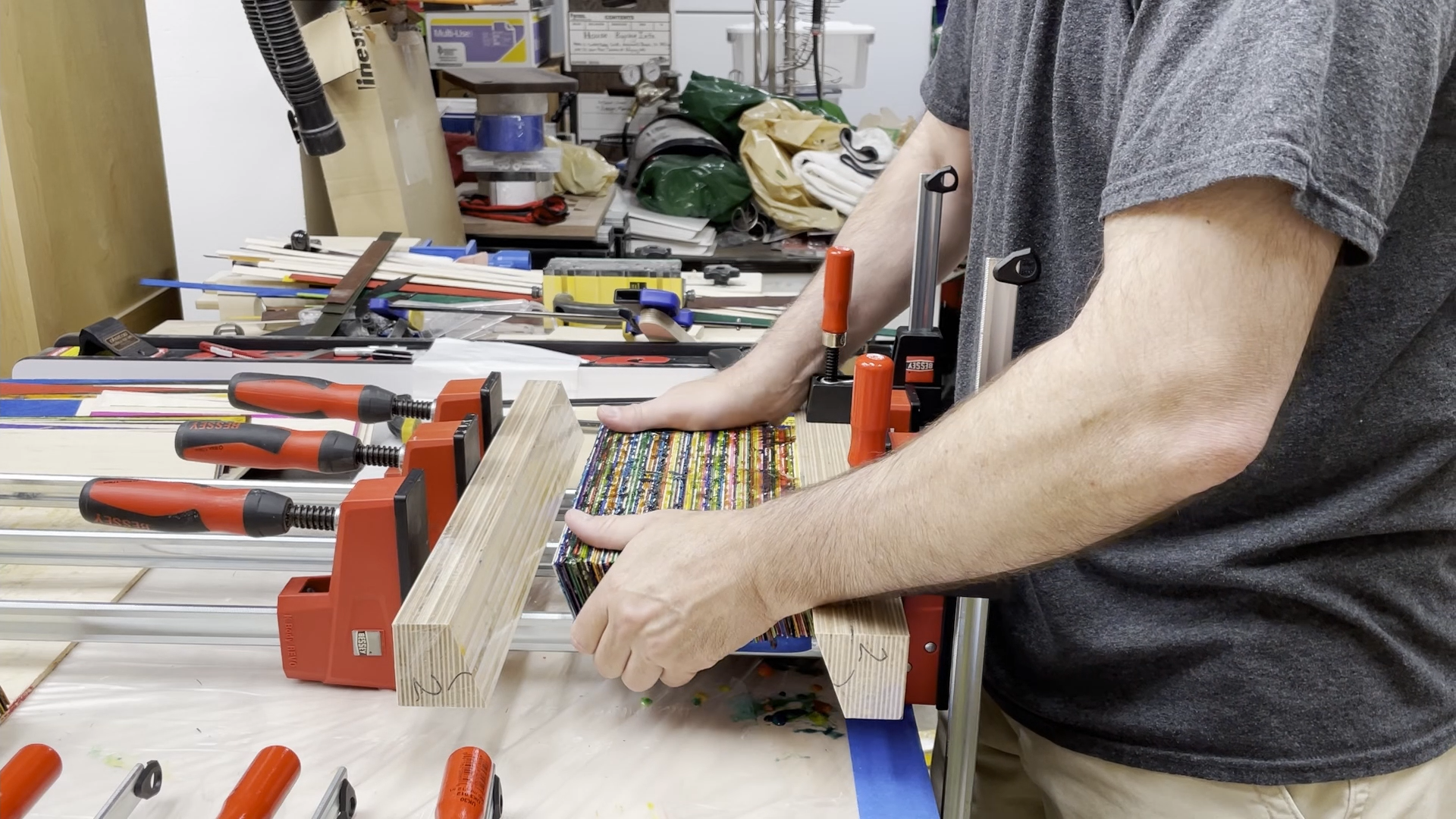
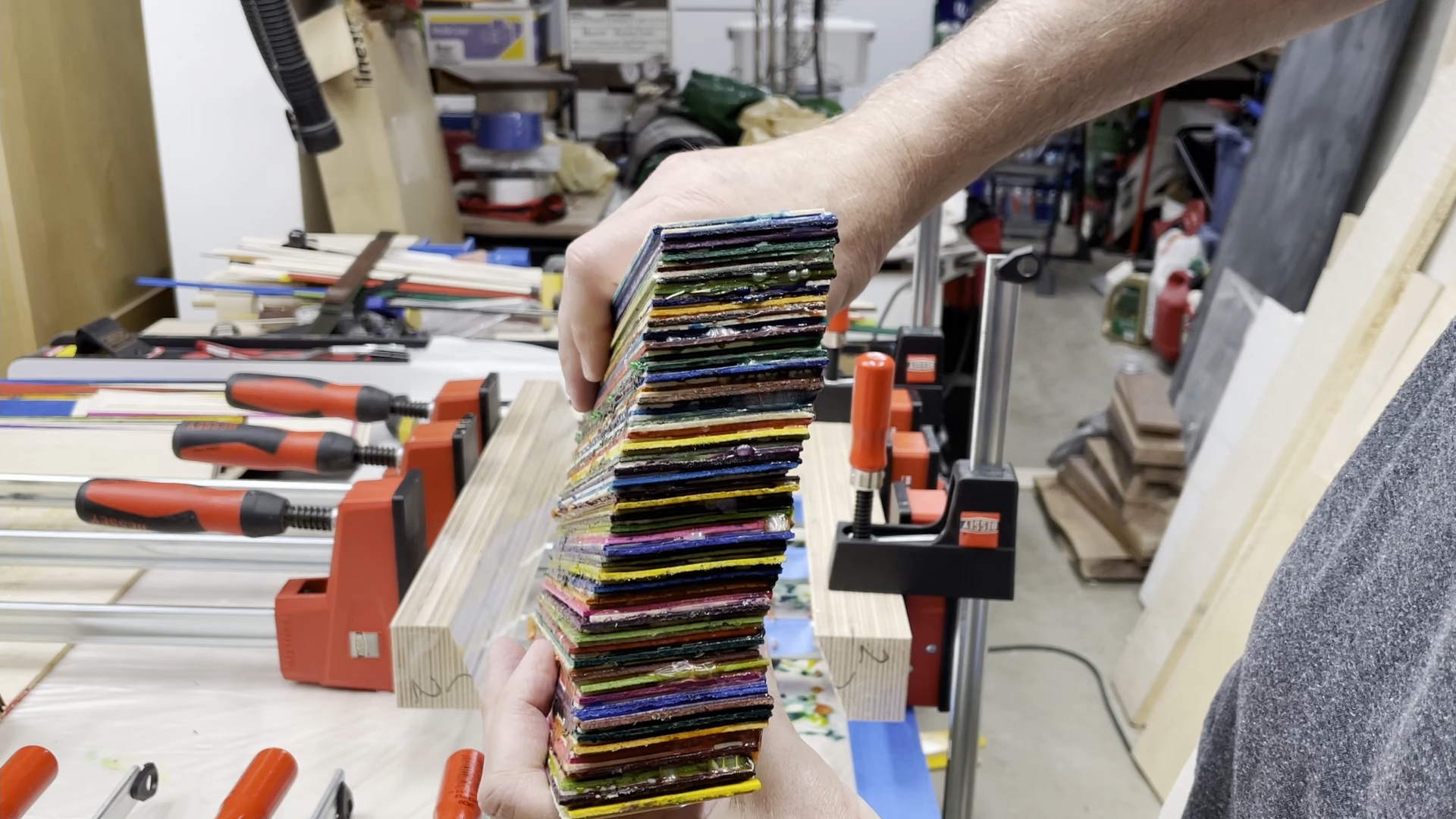
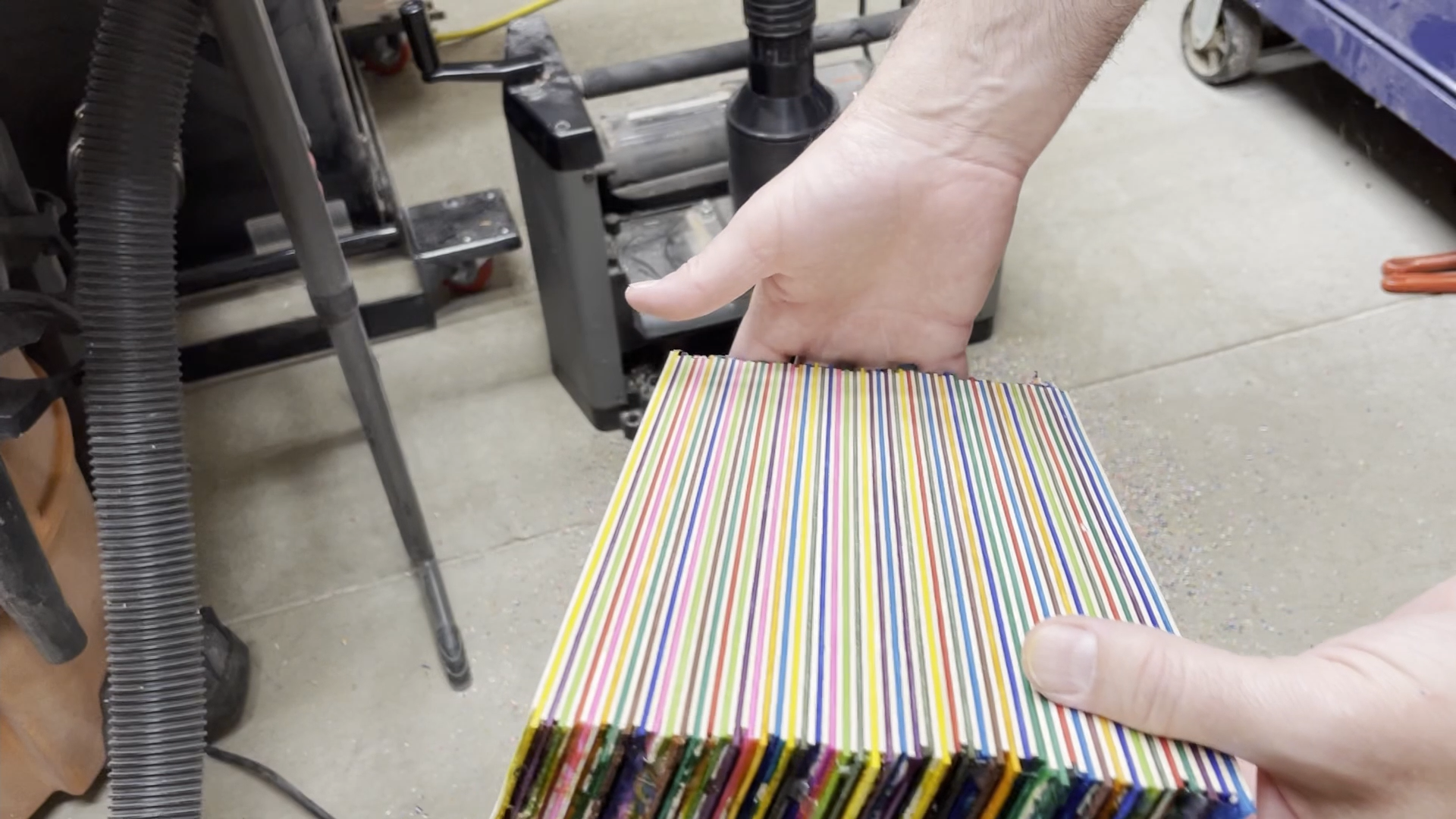
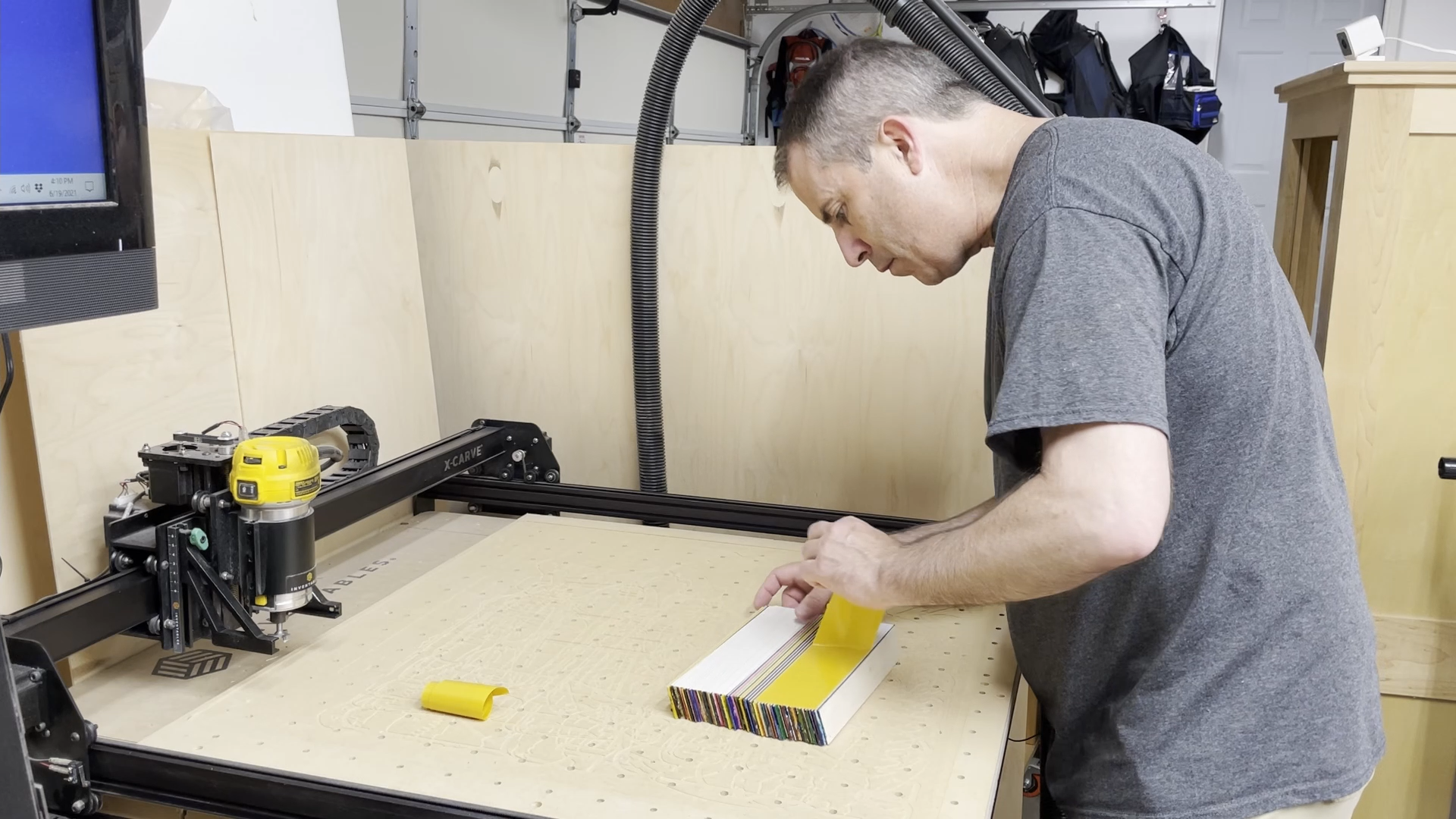
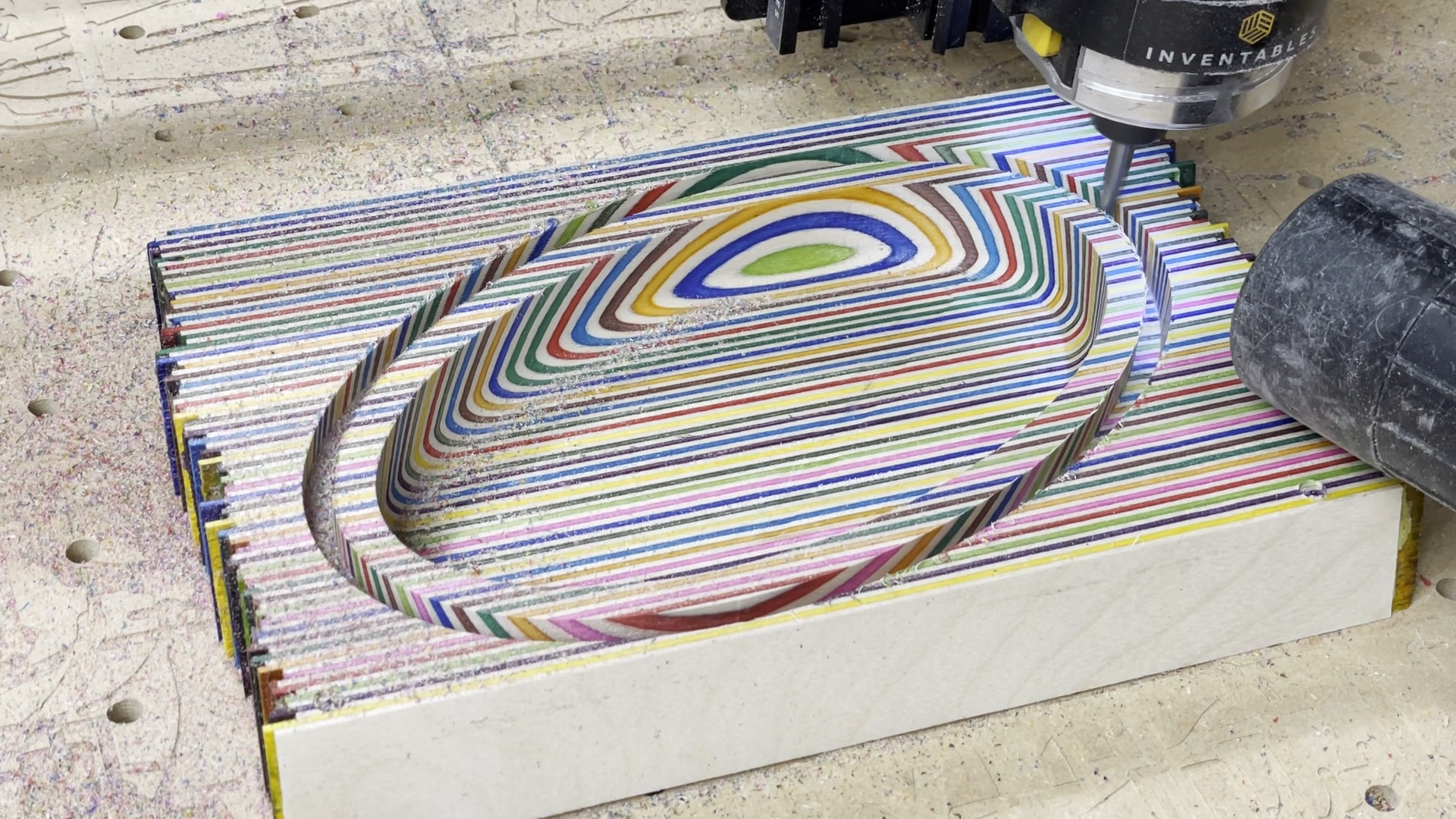
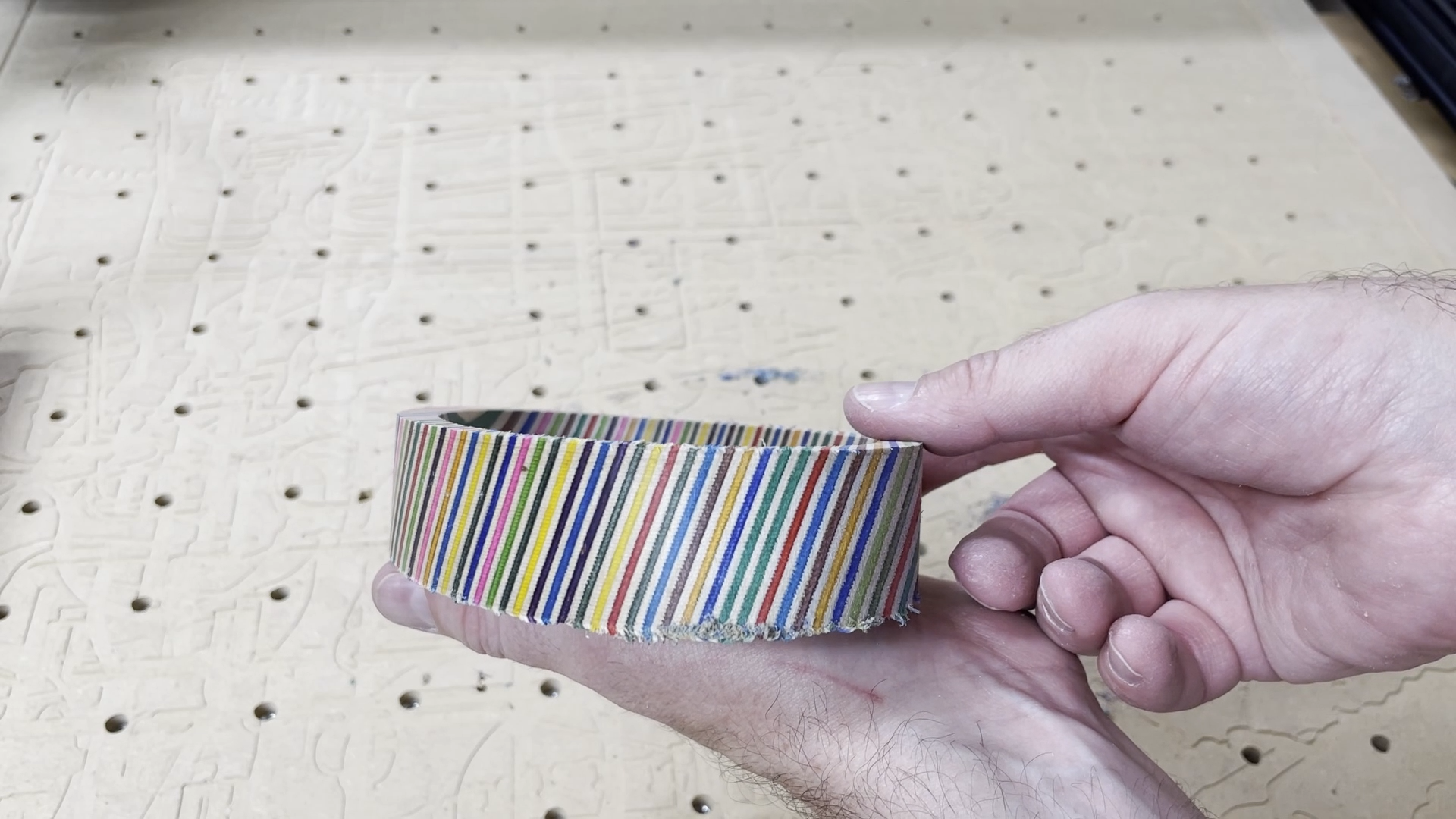
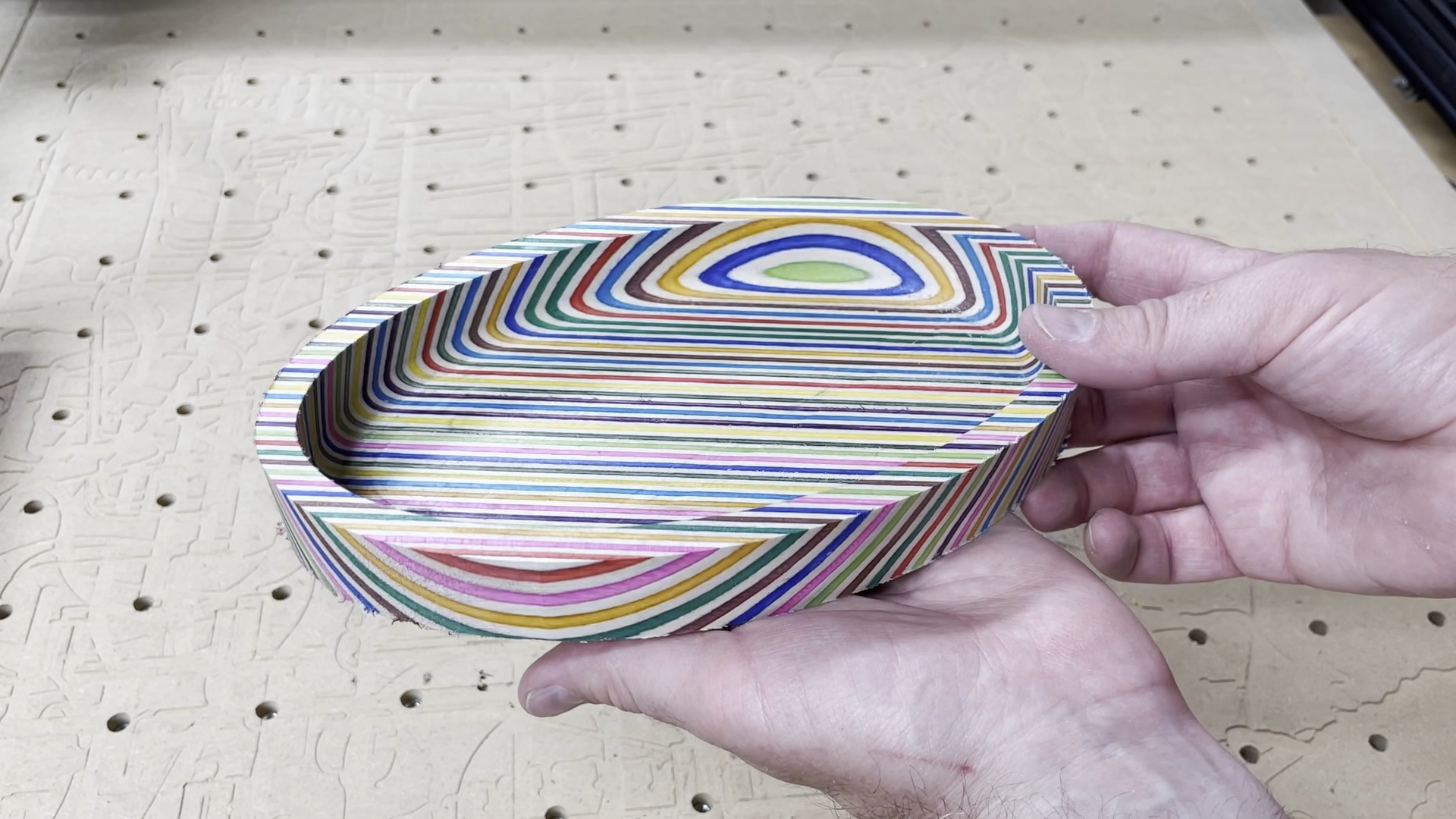
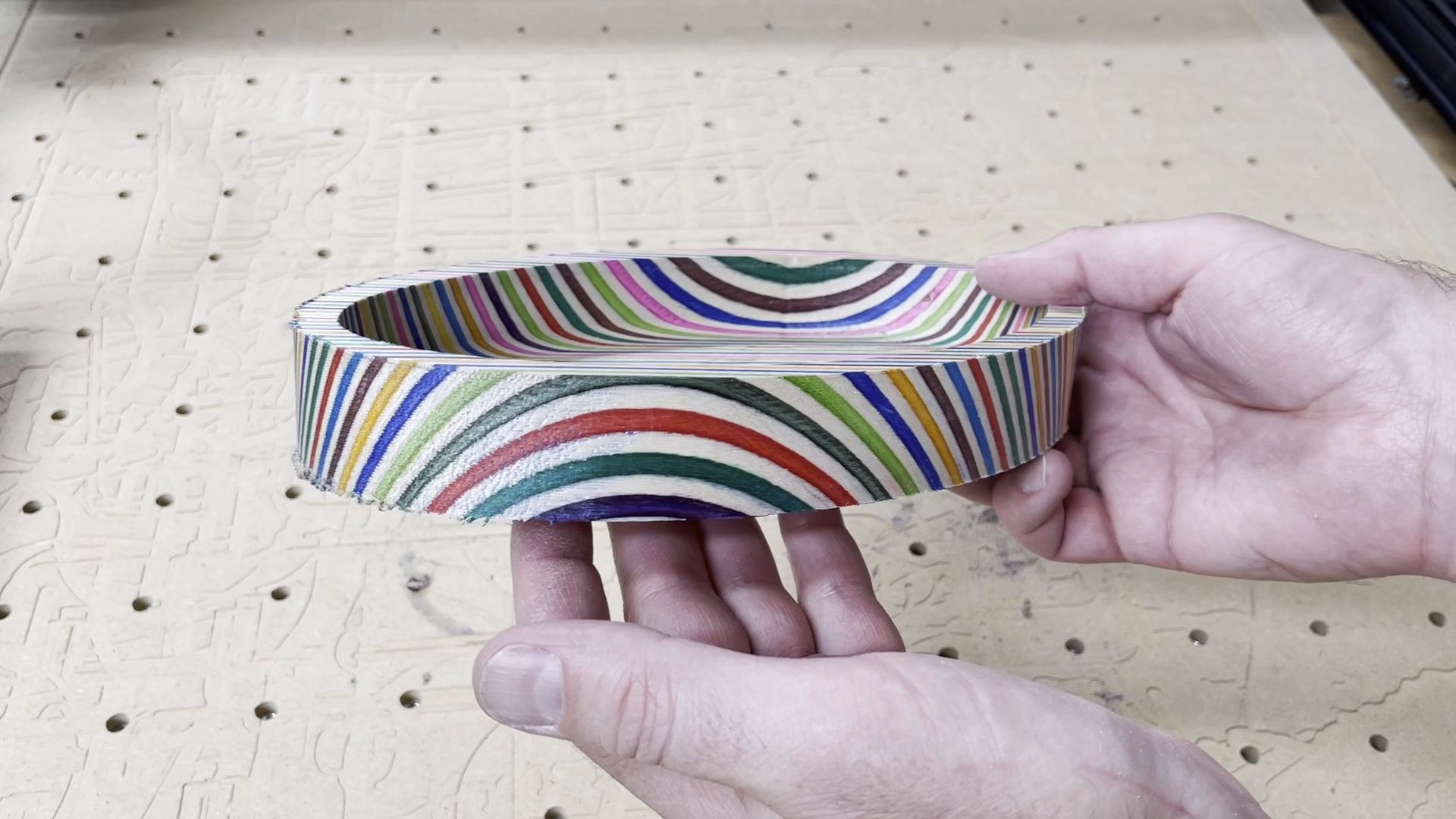
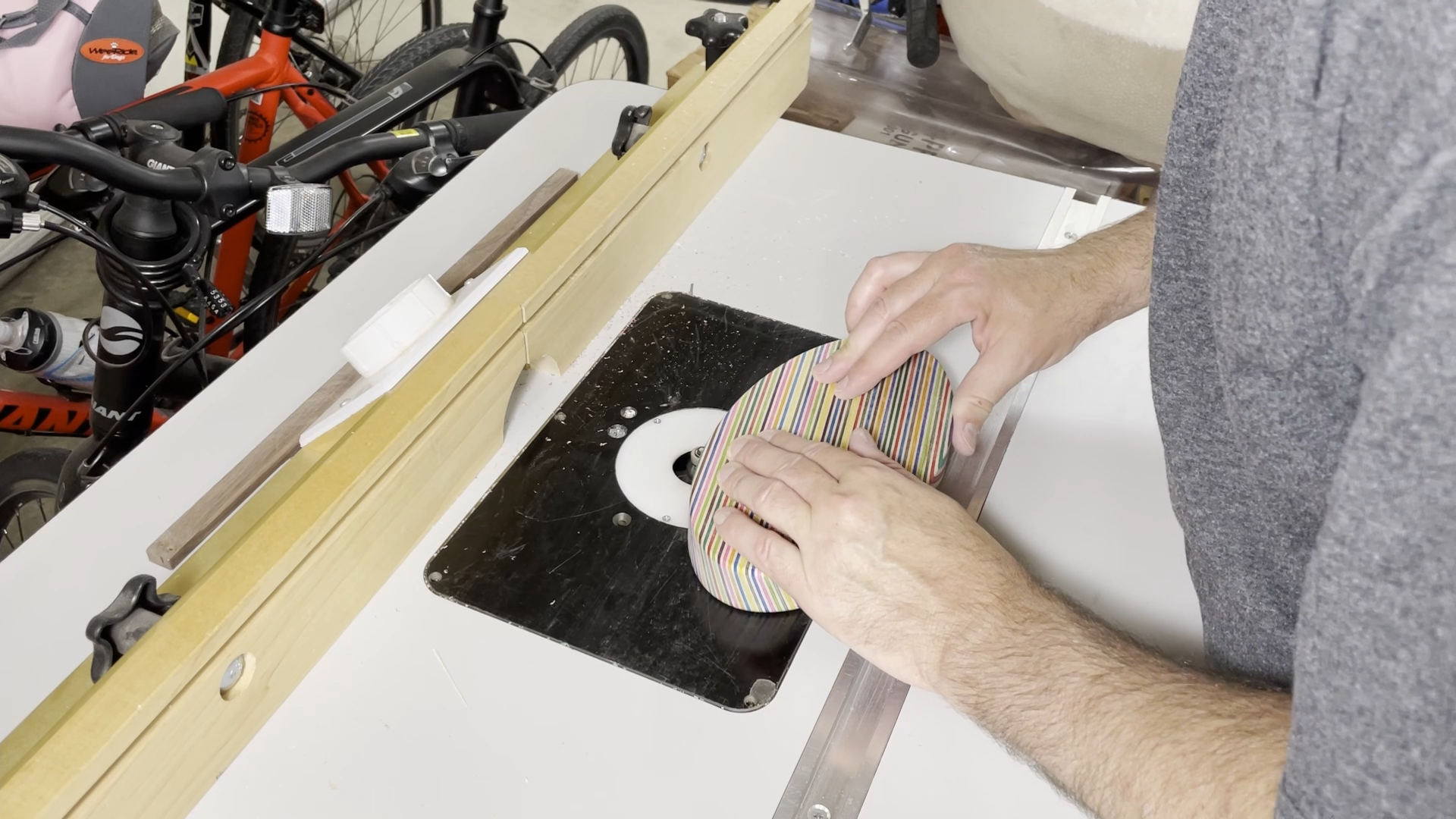
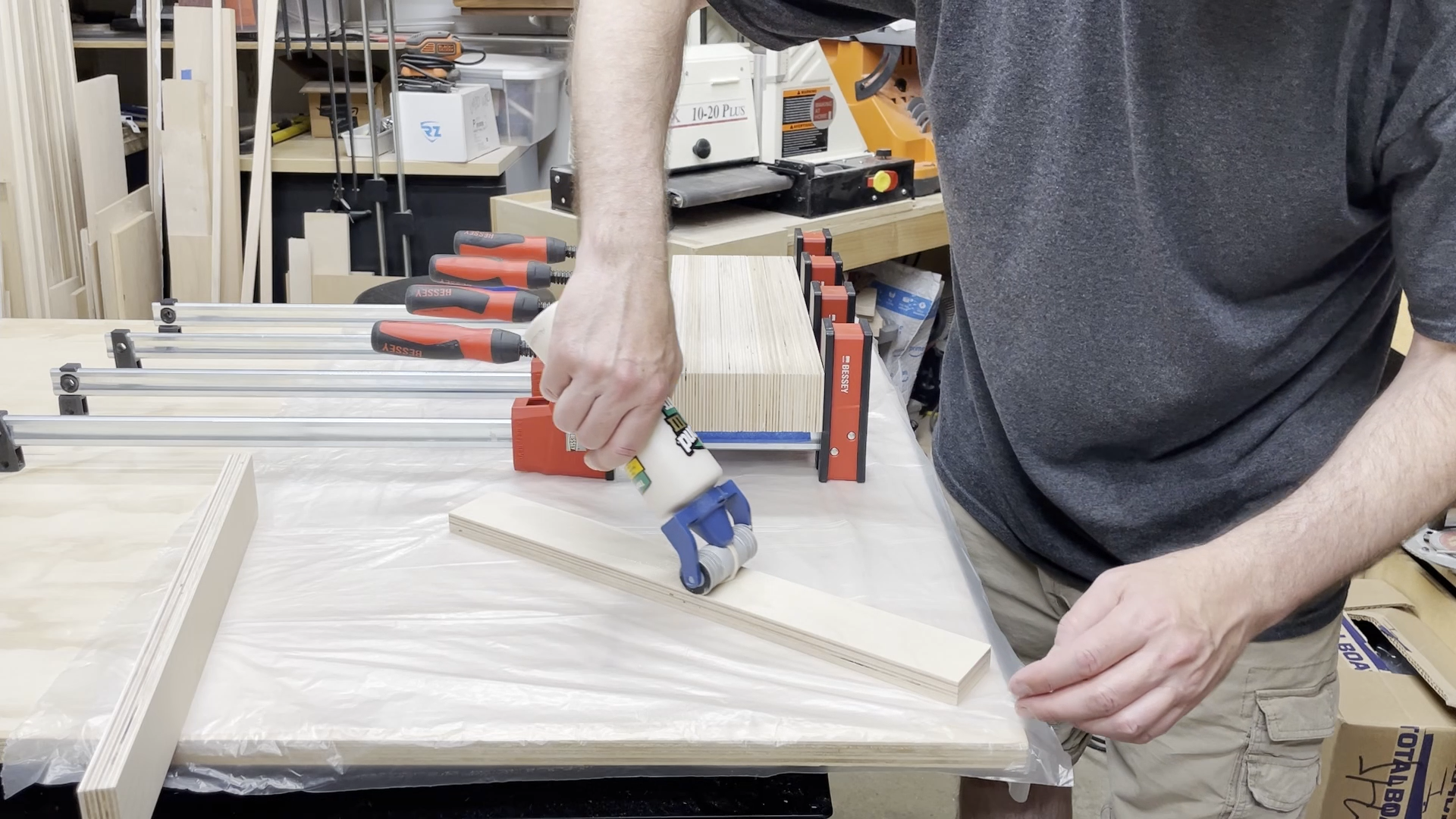
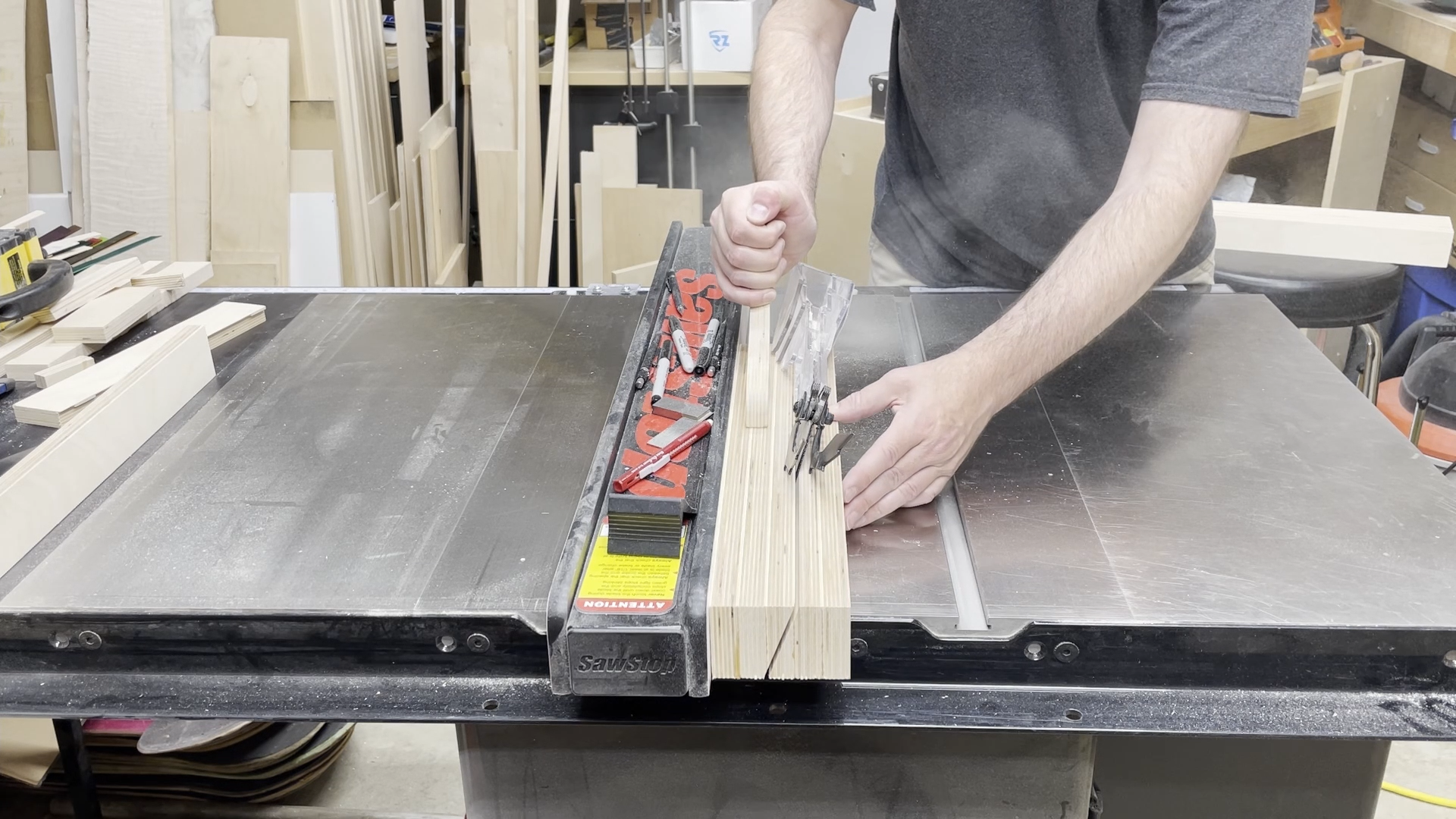
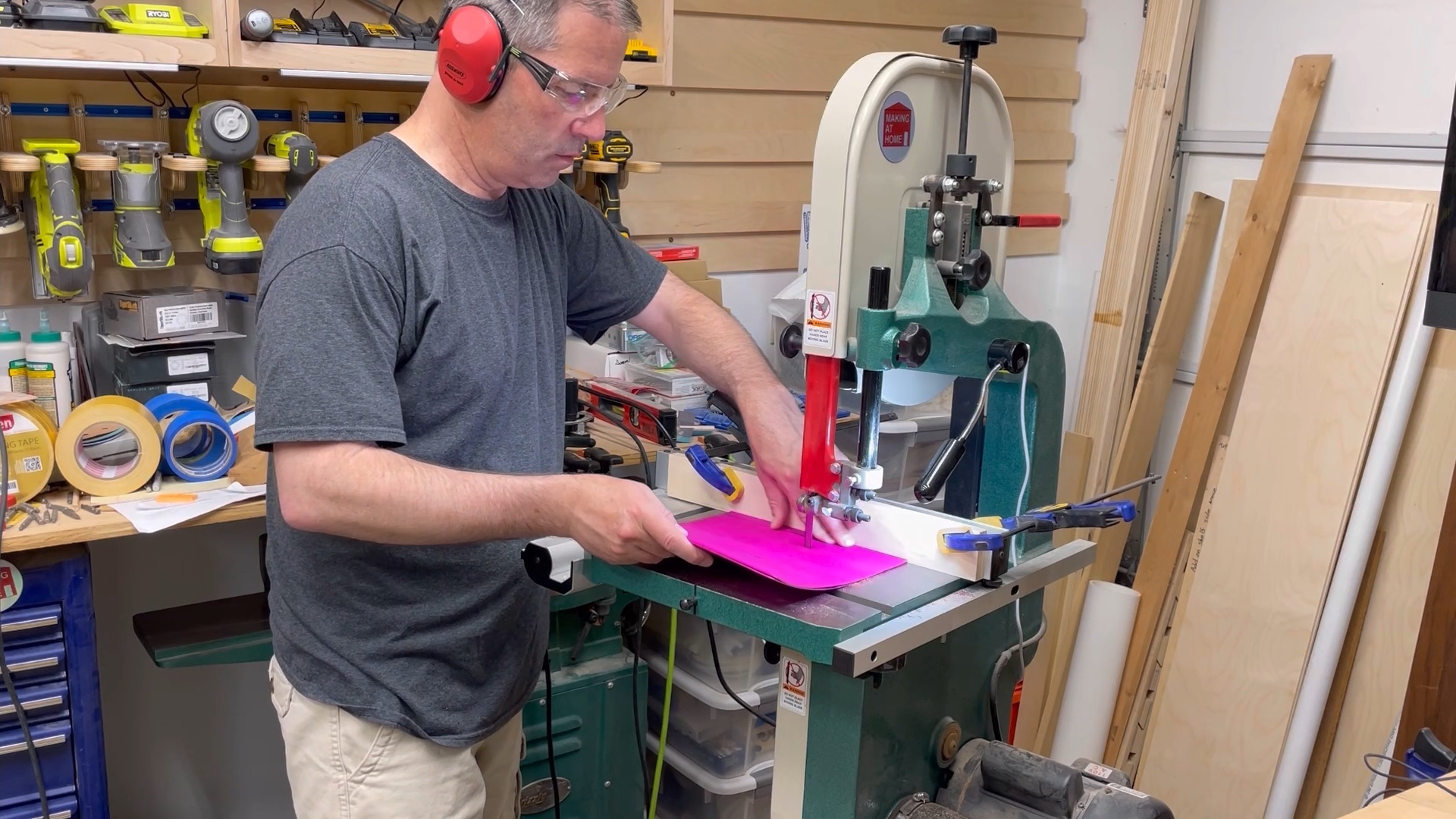
Step 4: Wavey Veneer Tray
The wavey veneer tray is created by cutting wavey lines through a wood blank with a band saw. The strip of veneer is glued in place using epoxy. After this sets up you can repeat the process and cut another wavey line into the blank. For this example, I used 1/16” thick pink veneer strips in a curly maple wood blank. The pink lines really give a contrast to the maple and are an eye catcher.
With this technique you can really get creative by varying the number and color of the veneer strips being used.
I think it’s a good idea with this technique to trace the lines onto the piece of wood before you cut them. That way you can decide if you like the pattern before you actually start cutting into the wood.
The kerf on my bandsaw blade makes a cut that is slightly narrower than the 1/16” veneer that I used. To help account for that difference in width, I passed each side of the cut across my spindle sander to smooth out the bandsaw marks. Since it would be hard to get this to a perfect fit, I glued the pieces together with epoxy. This helps with any unevenness of the cuts and fills the gaps.
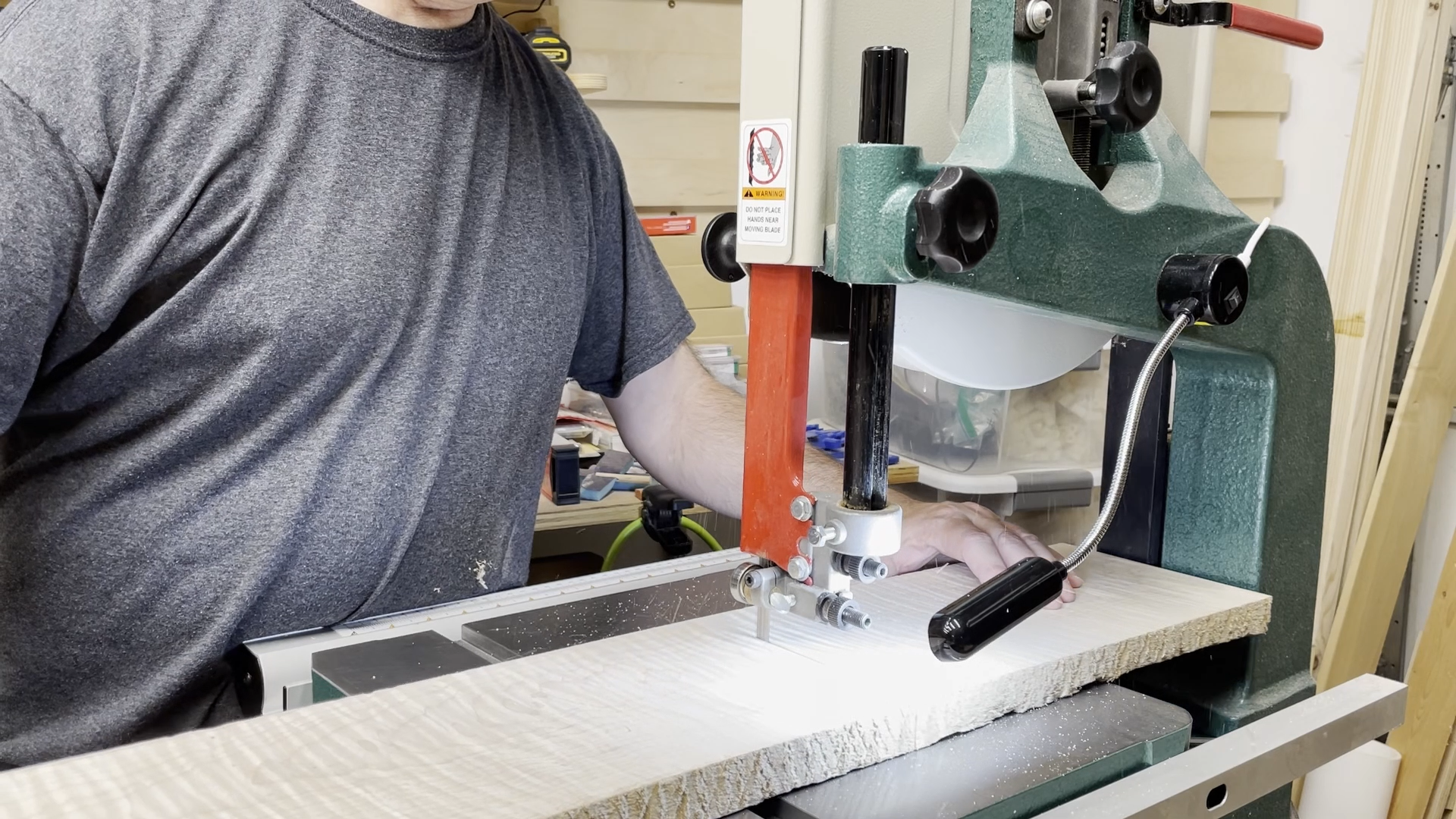
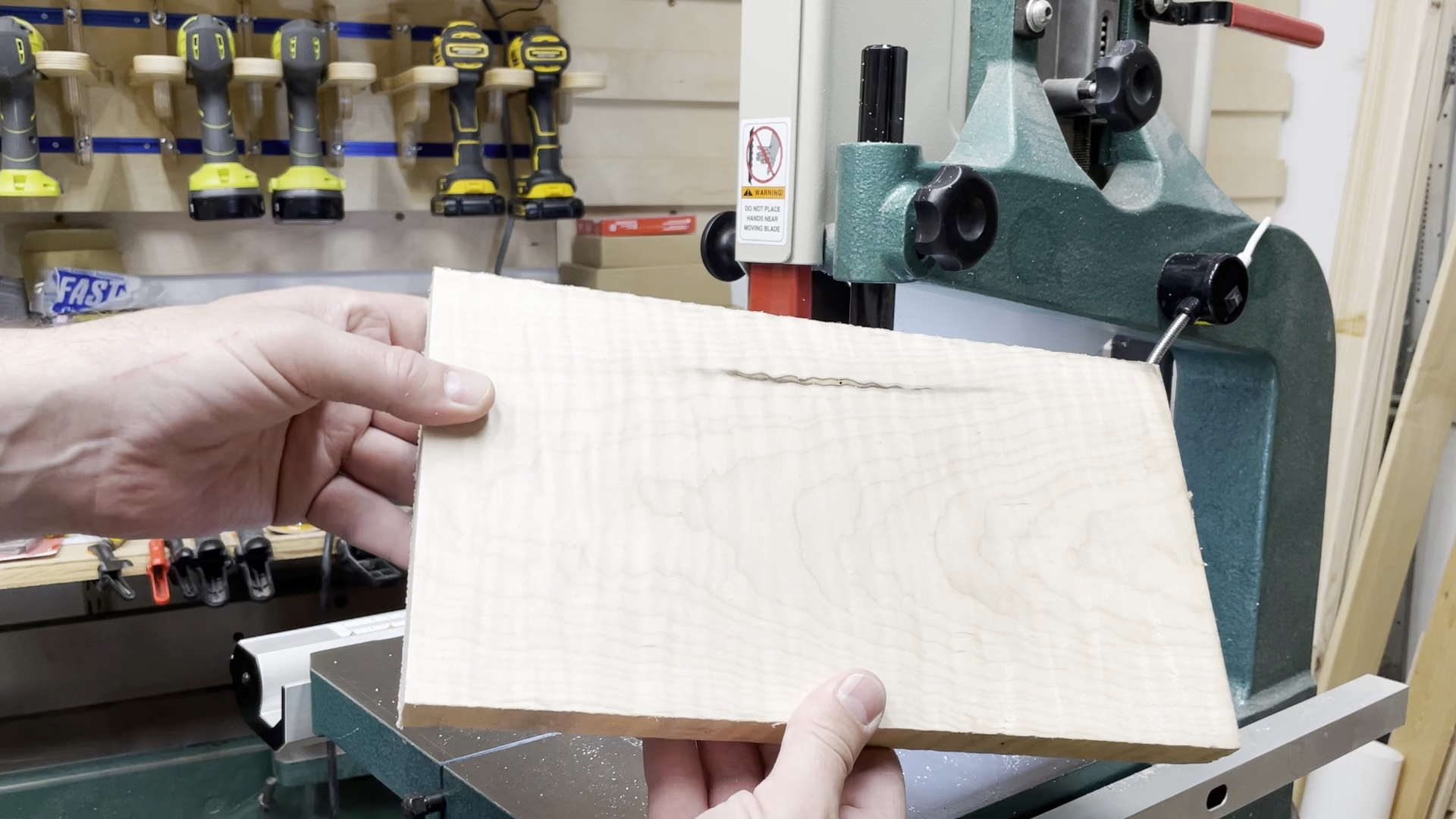
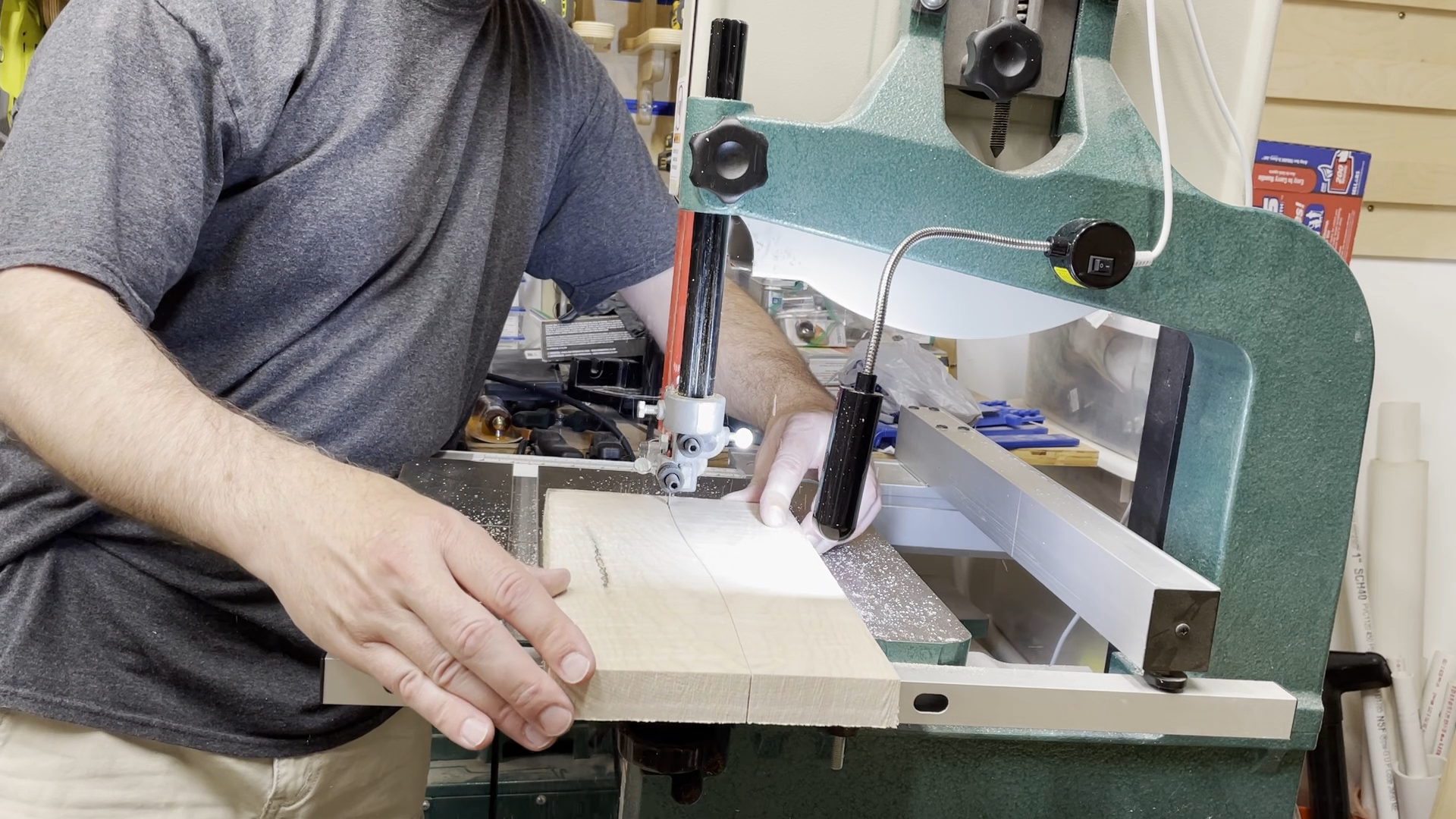

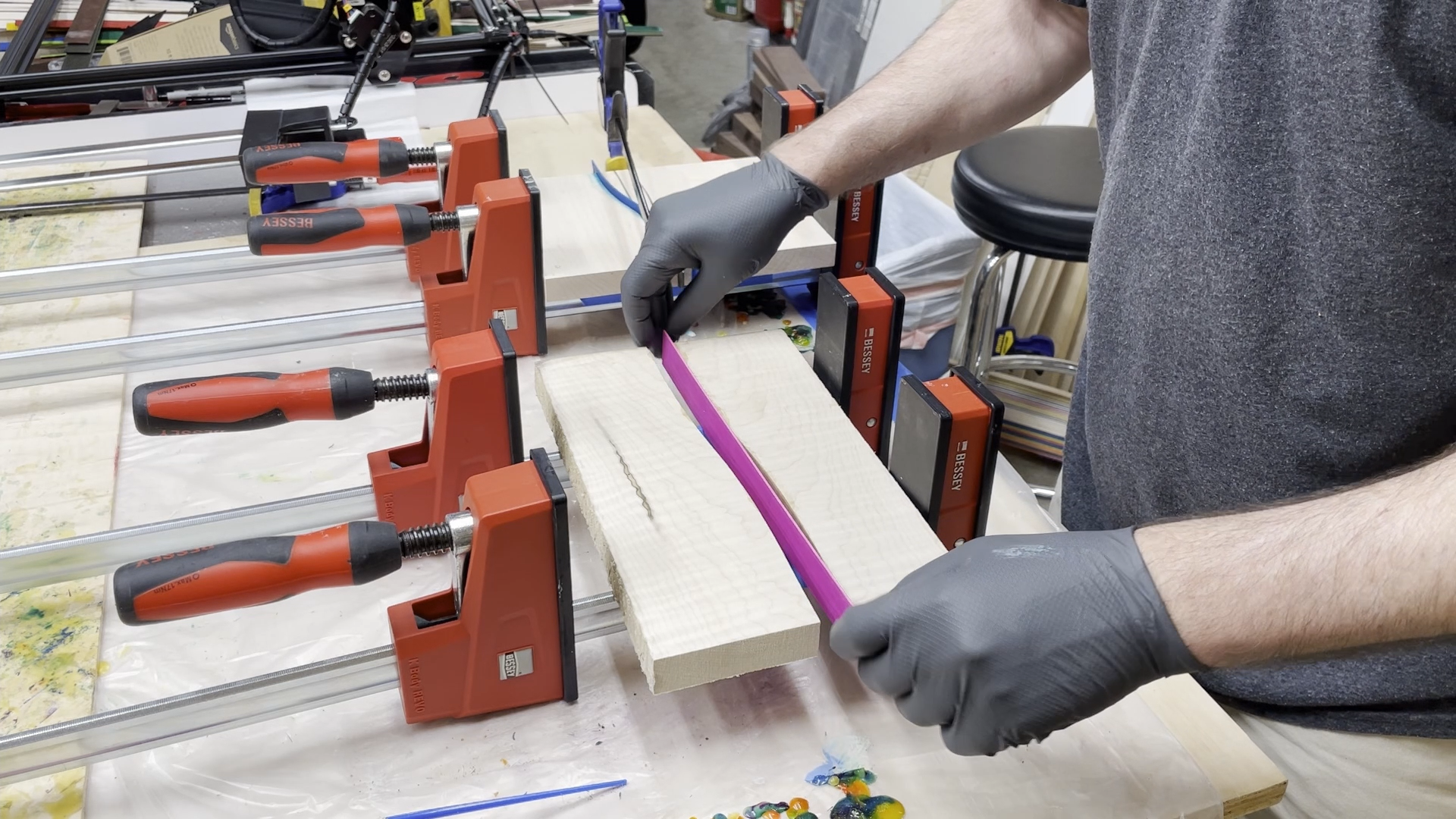
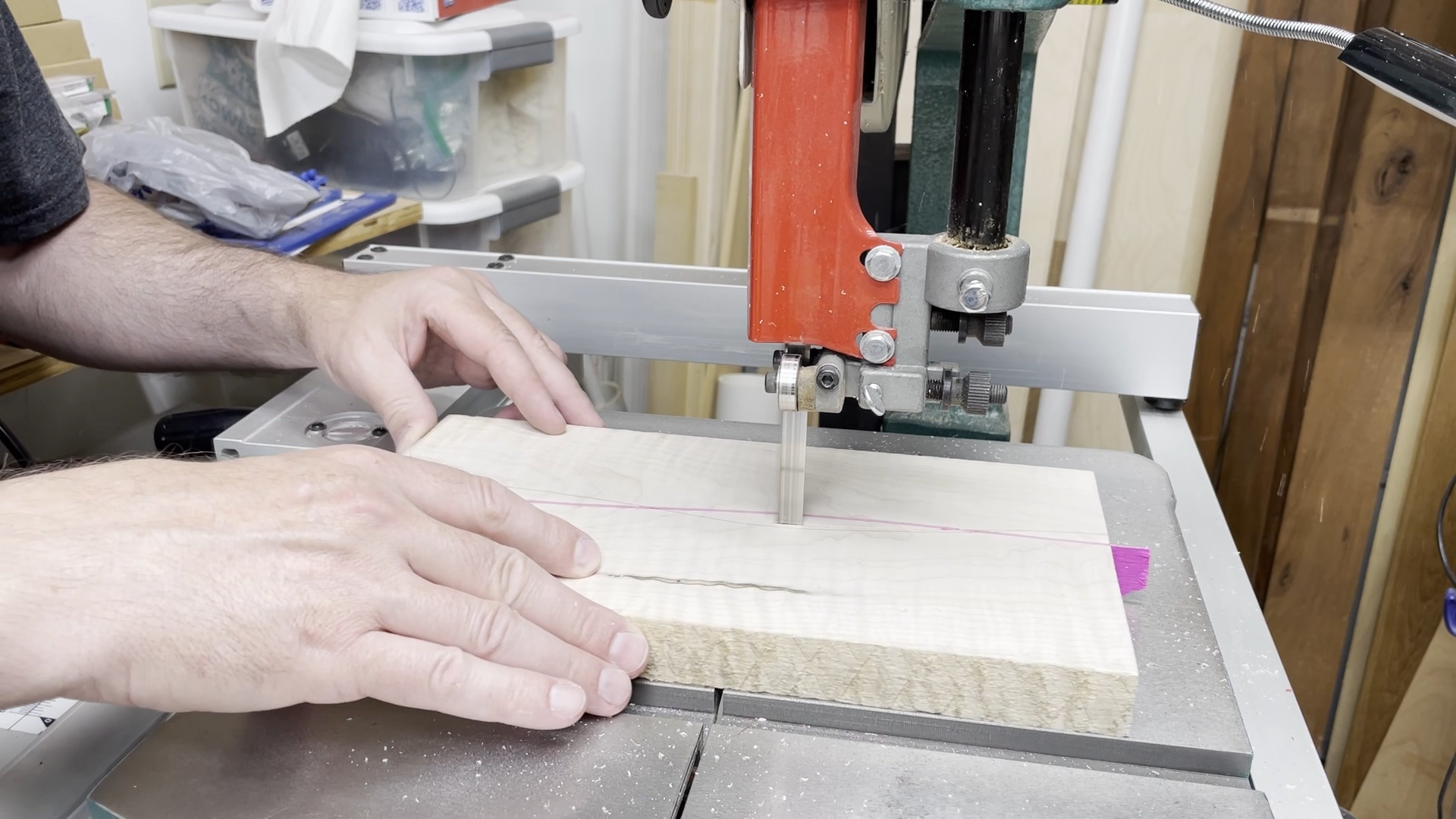
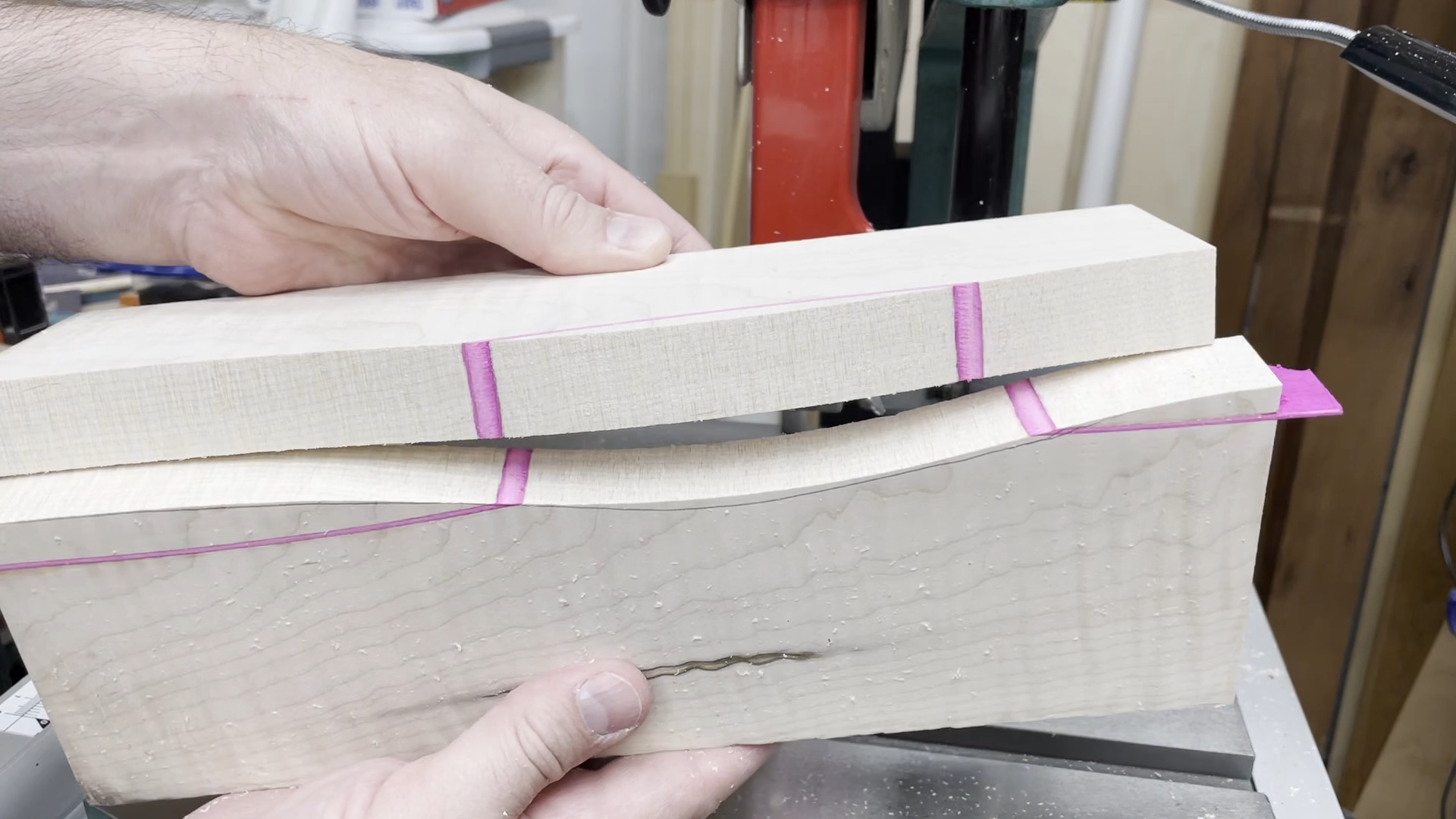
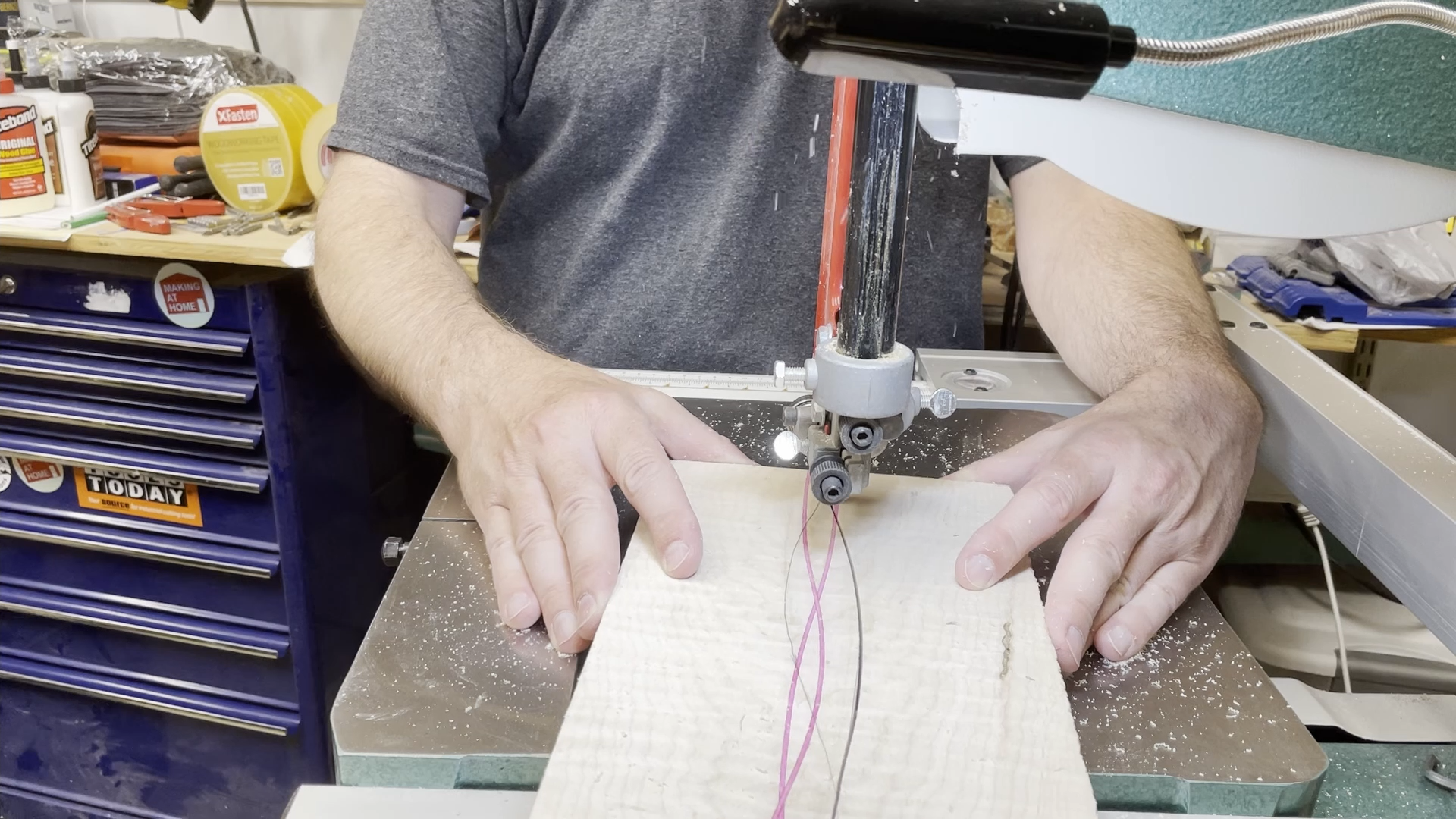
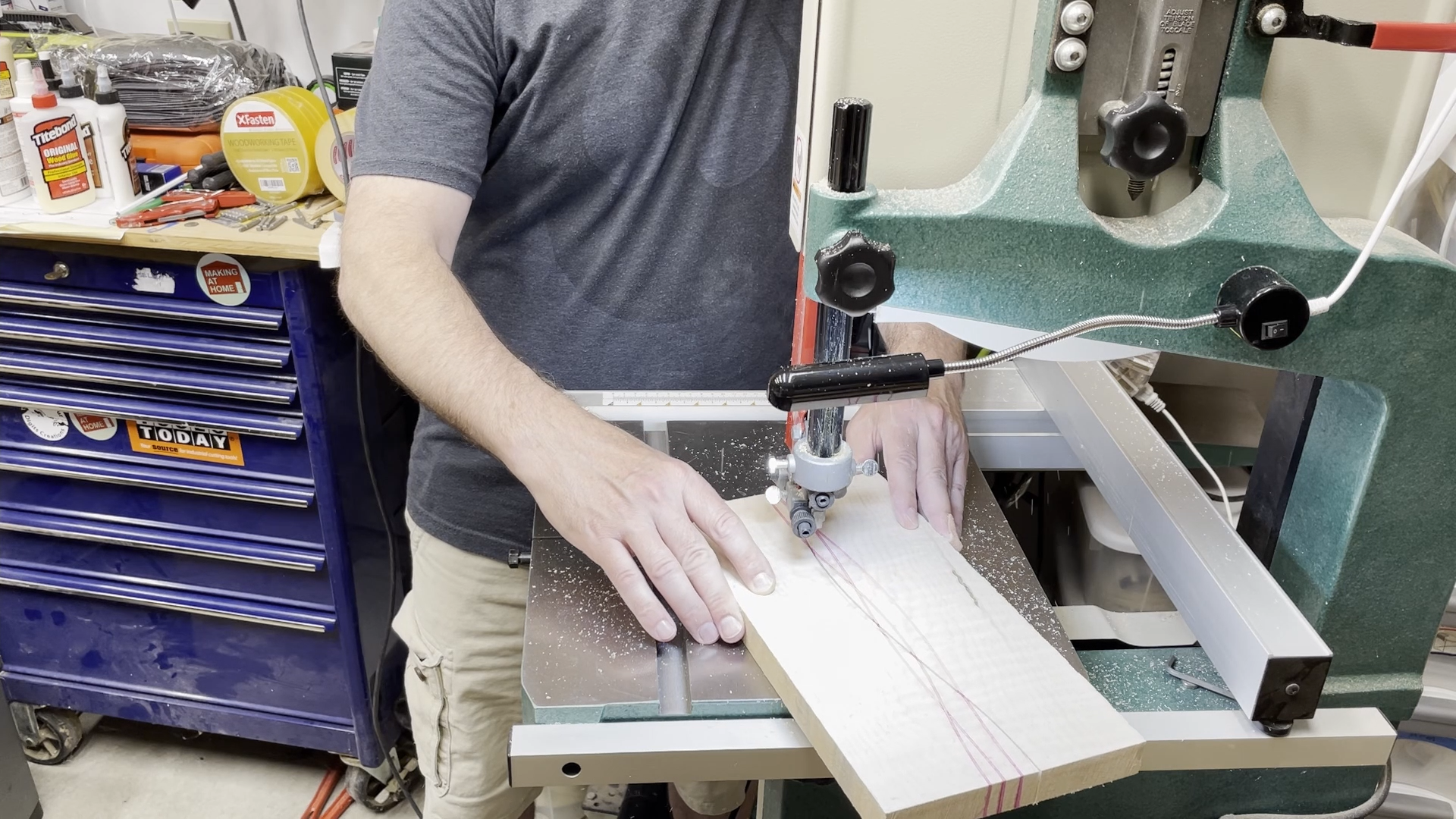
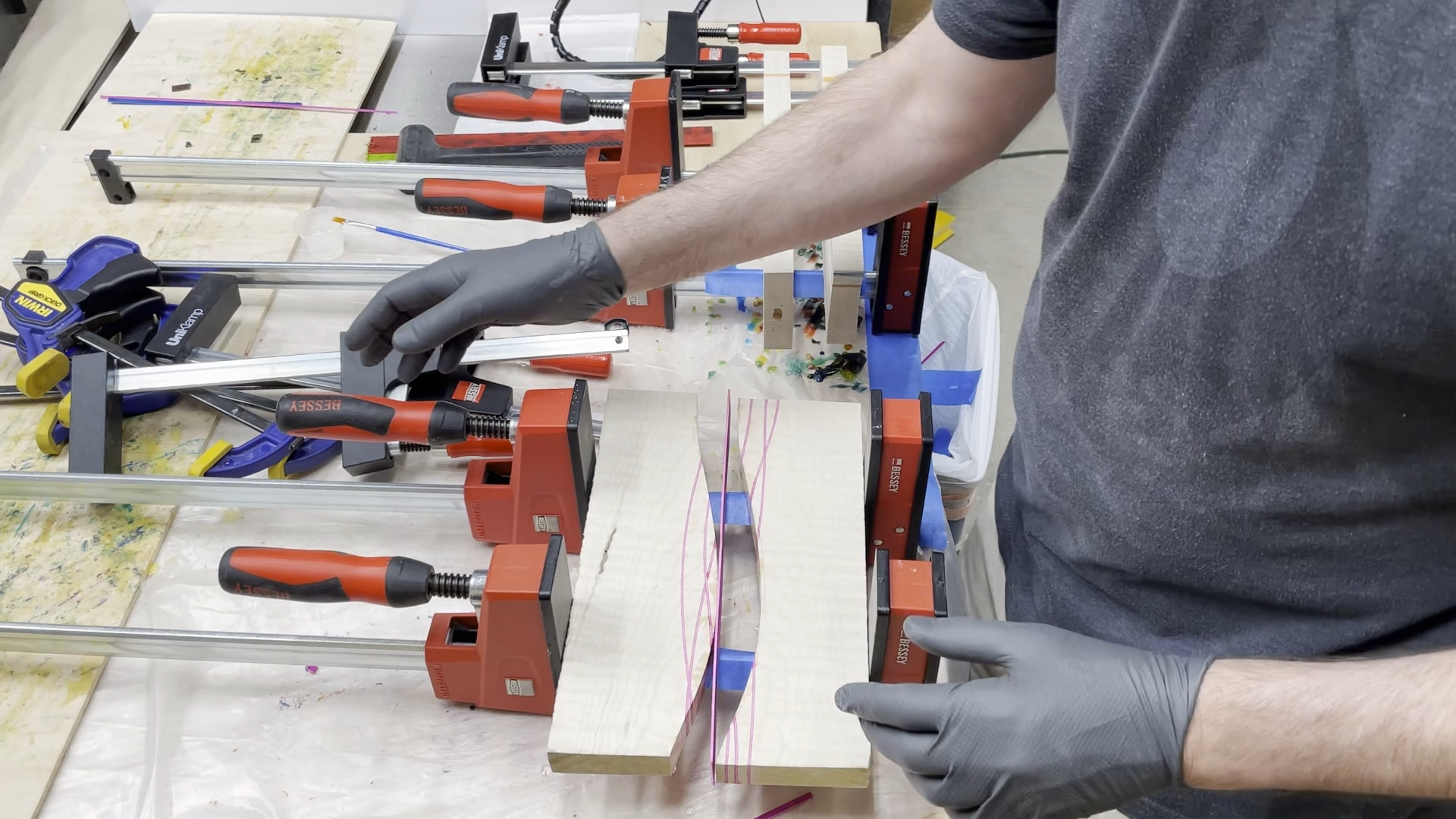
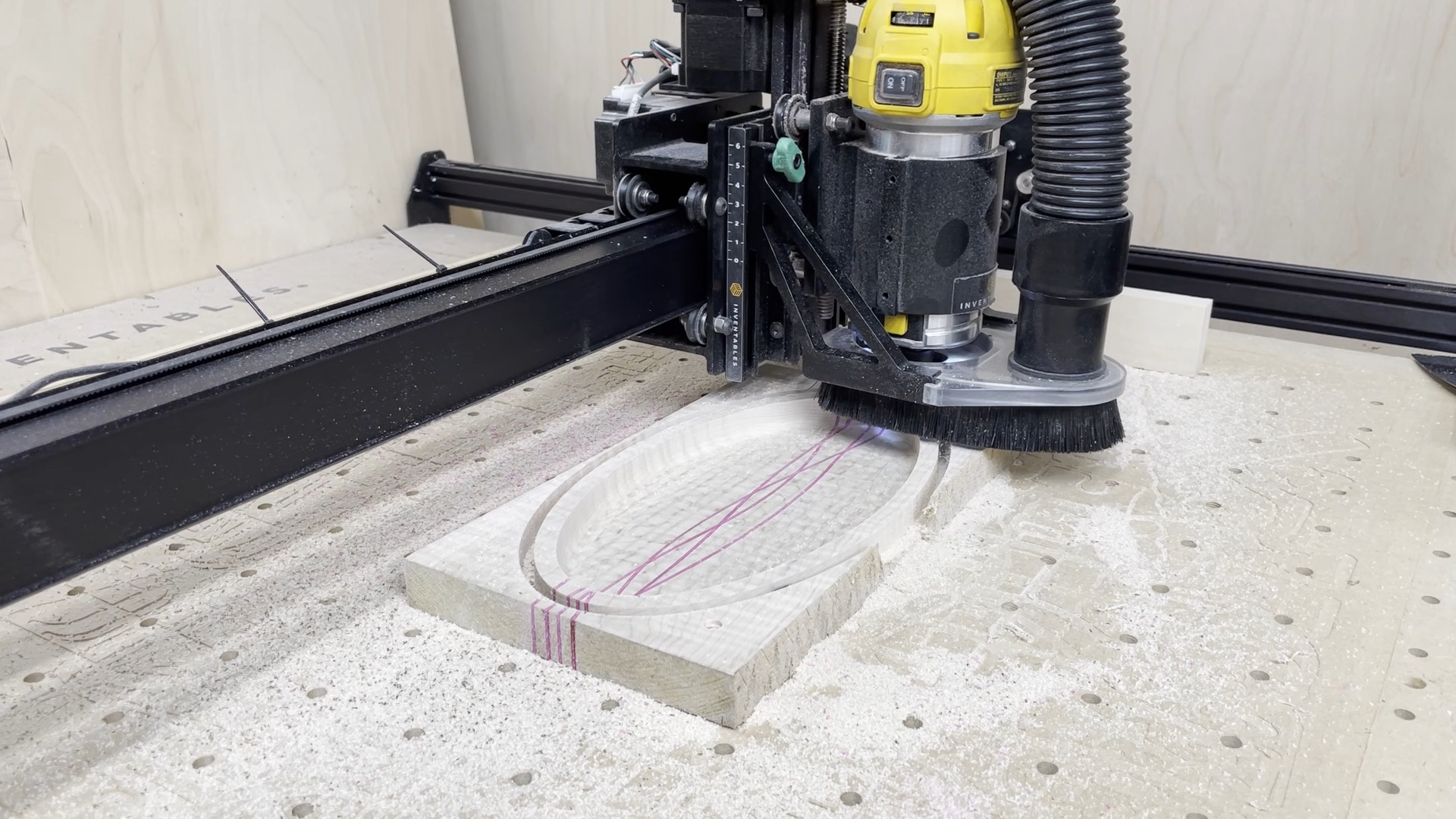
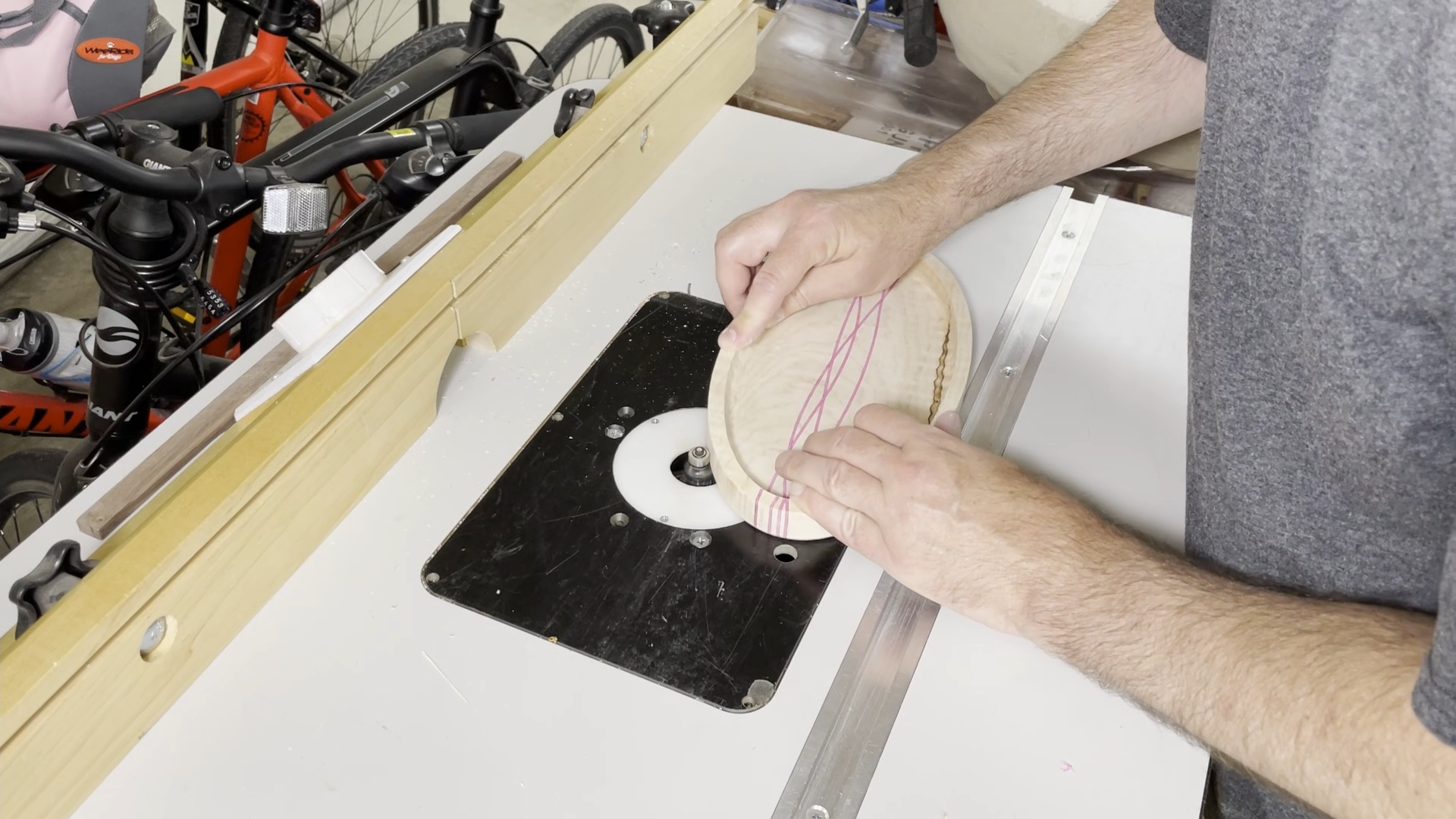
Step 5: Straight Veneer Tray
The simplest version of the tray involved adding several straight pieces of veneer to a blank of wood by making one straight cut on the table saw. For this example, I added three layers of veneer to a piece of lace wood. I layered one piece of pink dyed veneer between two layers of clear maple veneer. The clear piece of maple on each side of the pink veneer really made a difference in how much the pink veneer stood out in the piece if lacewood.
This glue up is very fast since all of the pieces can be glued together at one time.
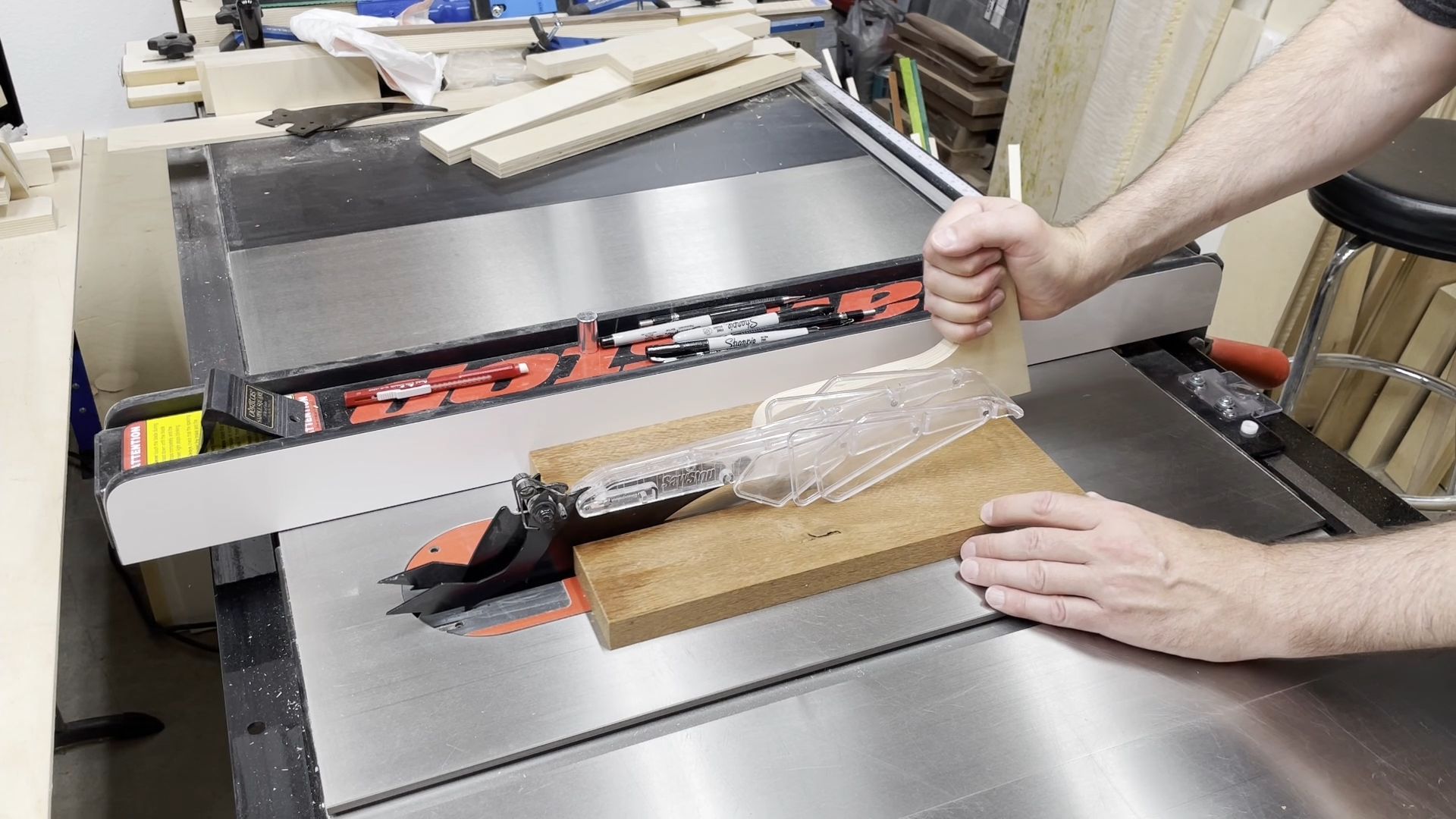
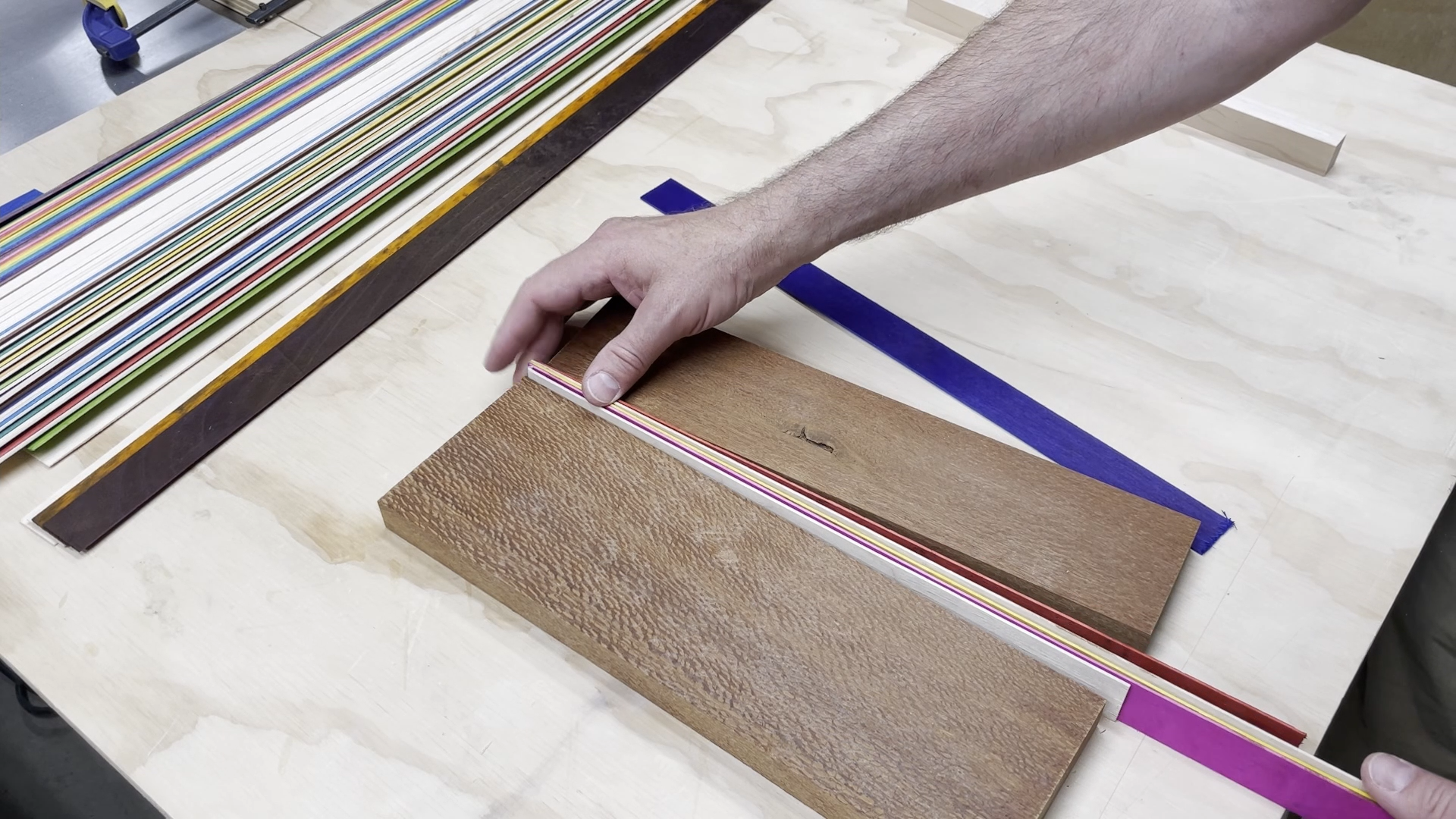
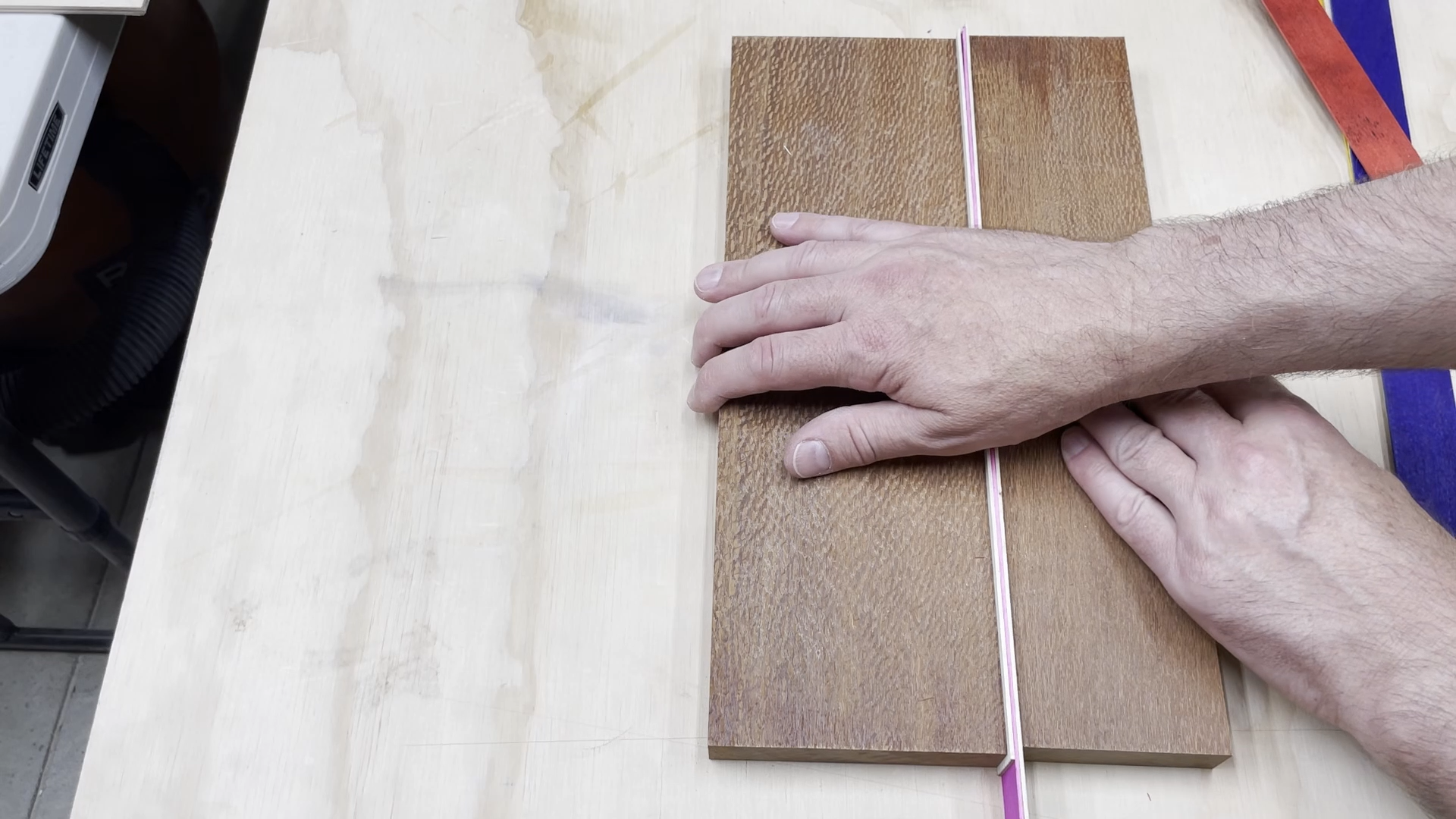
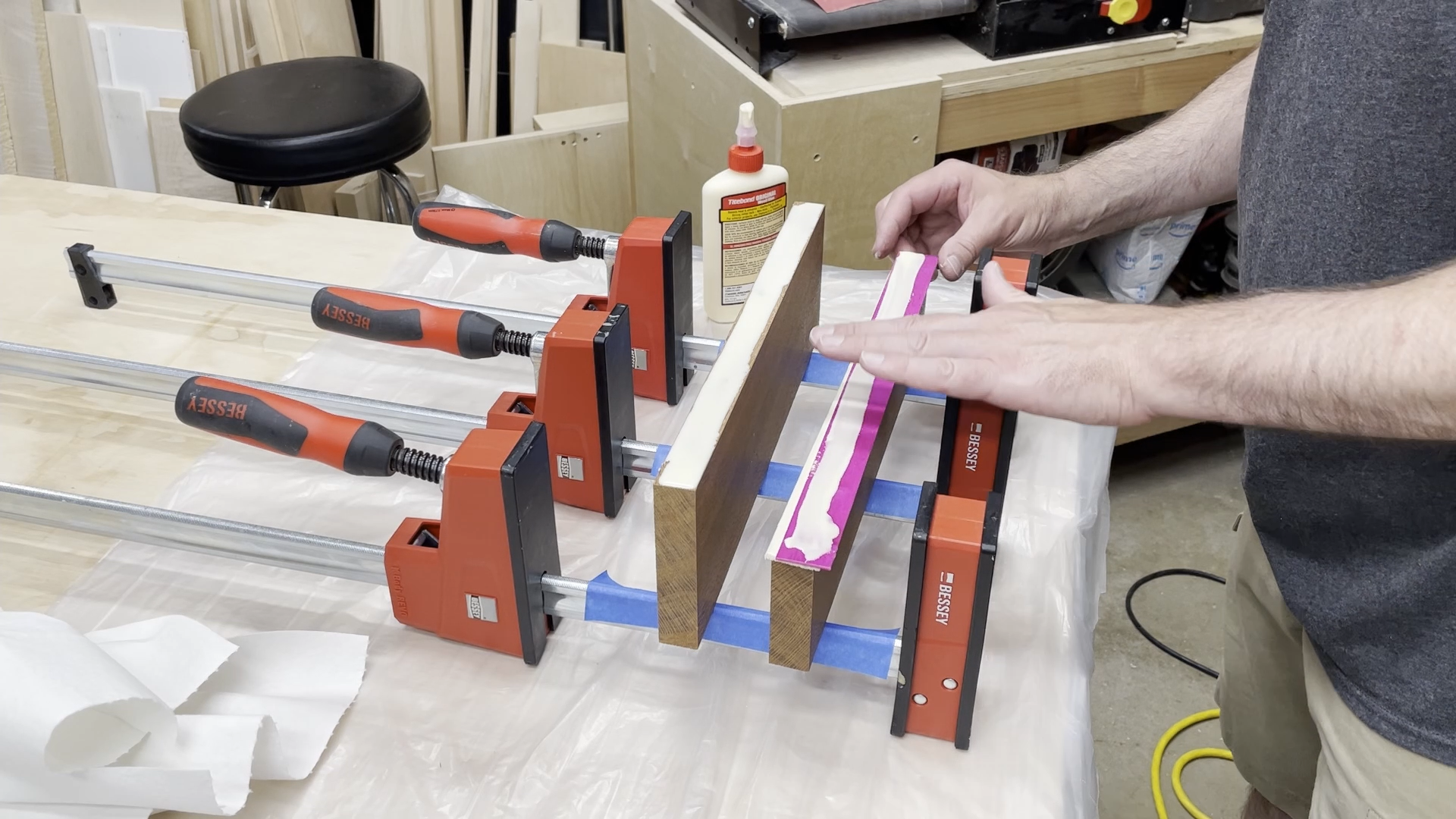
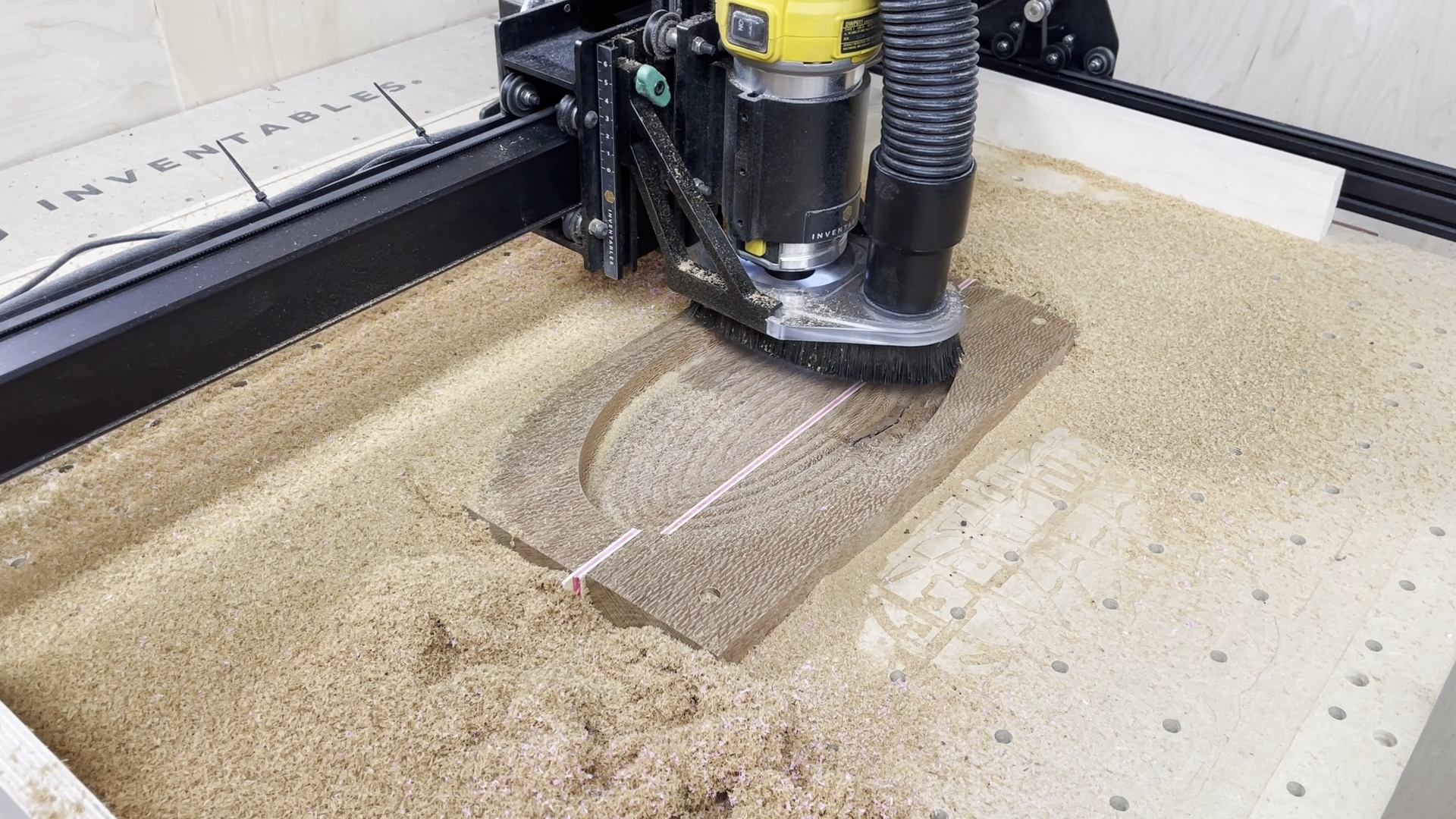
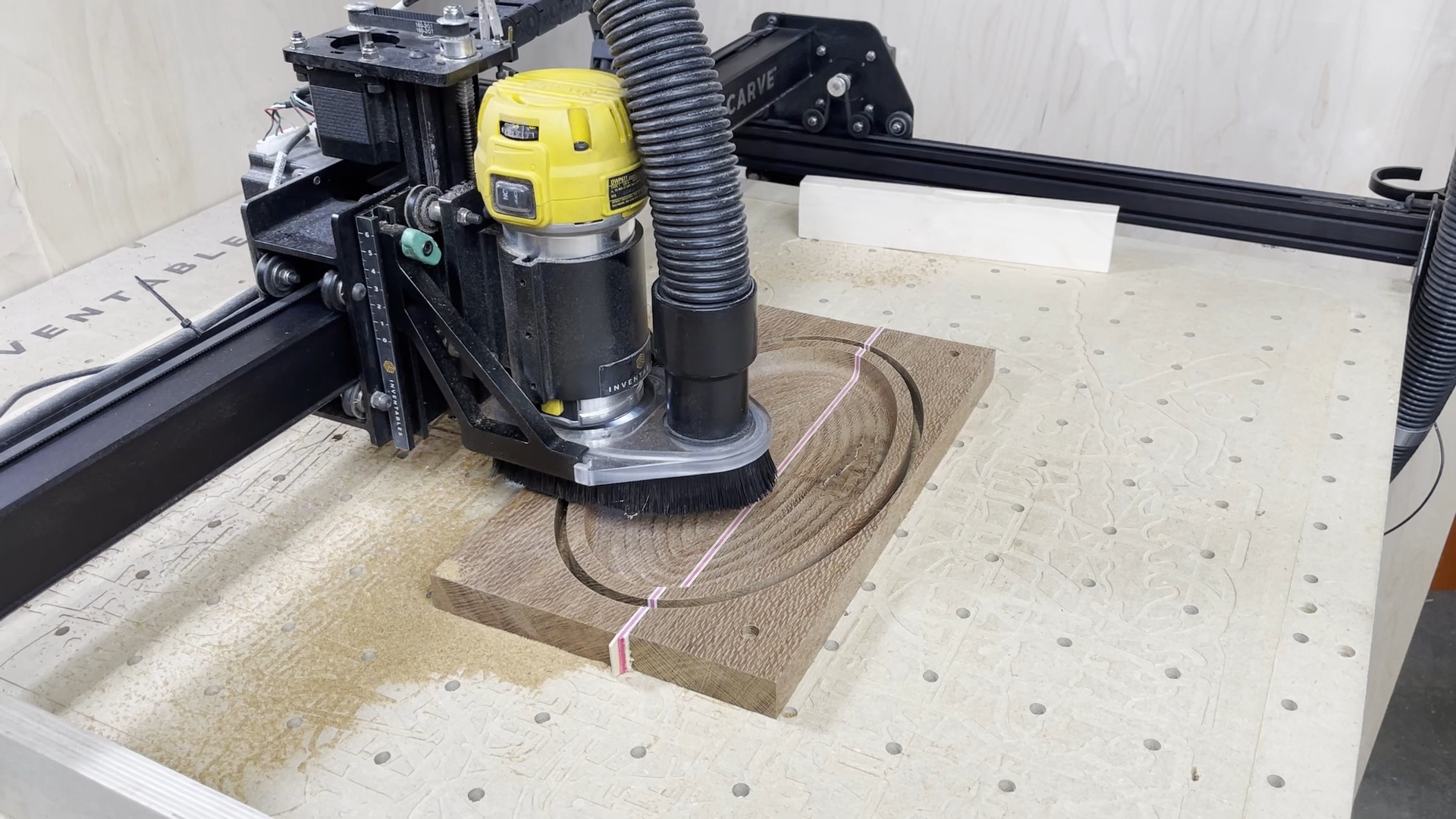
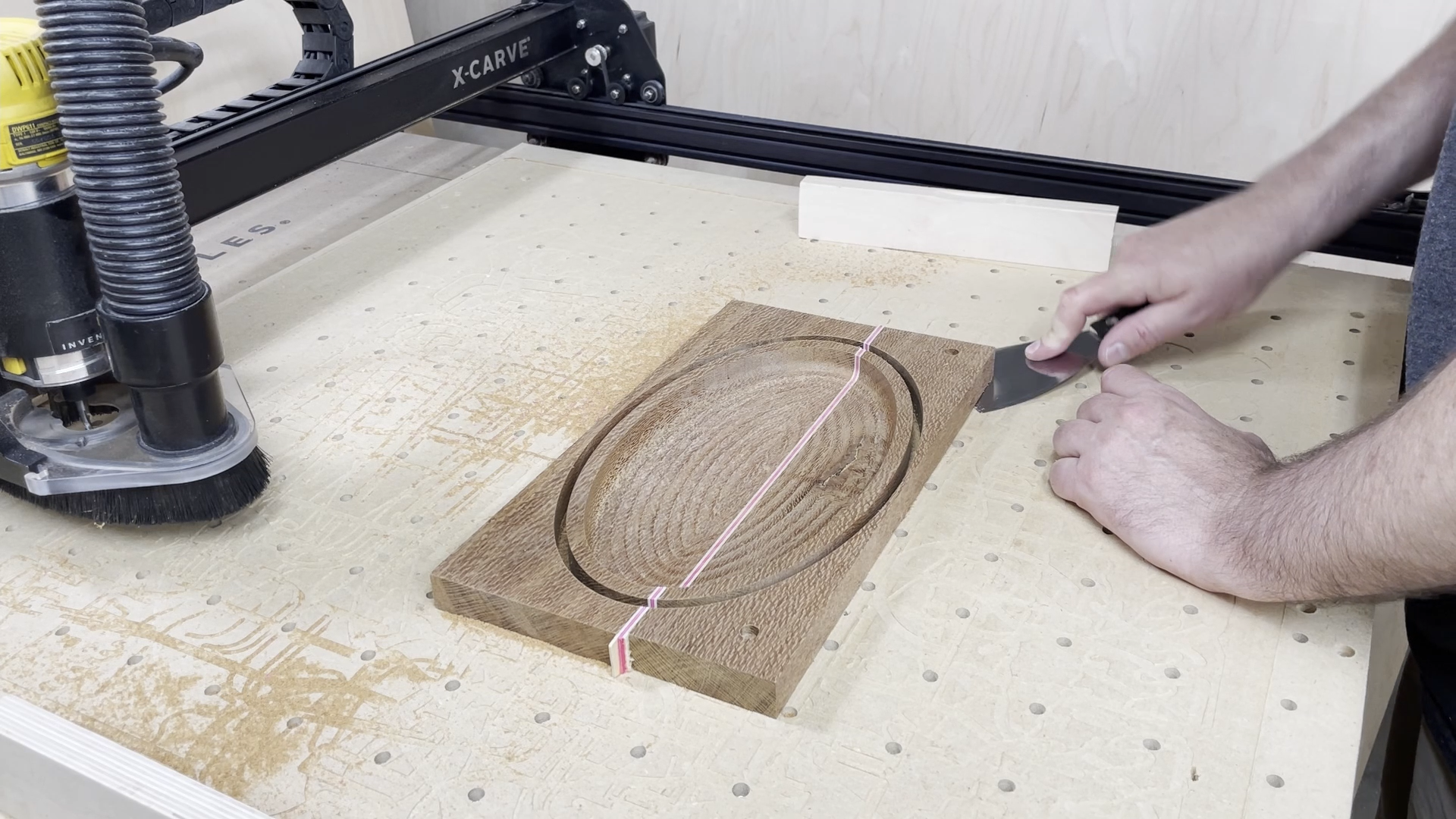
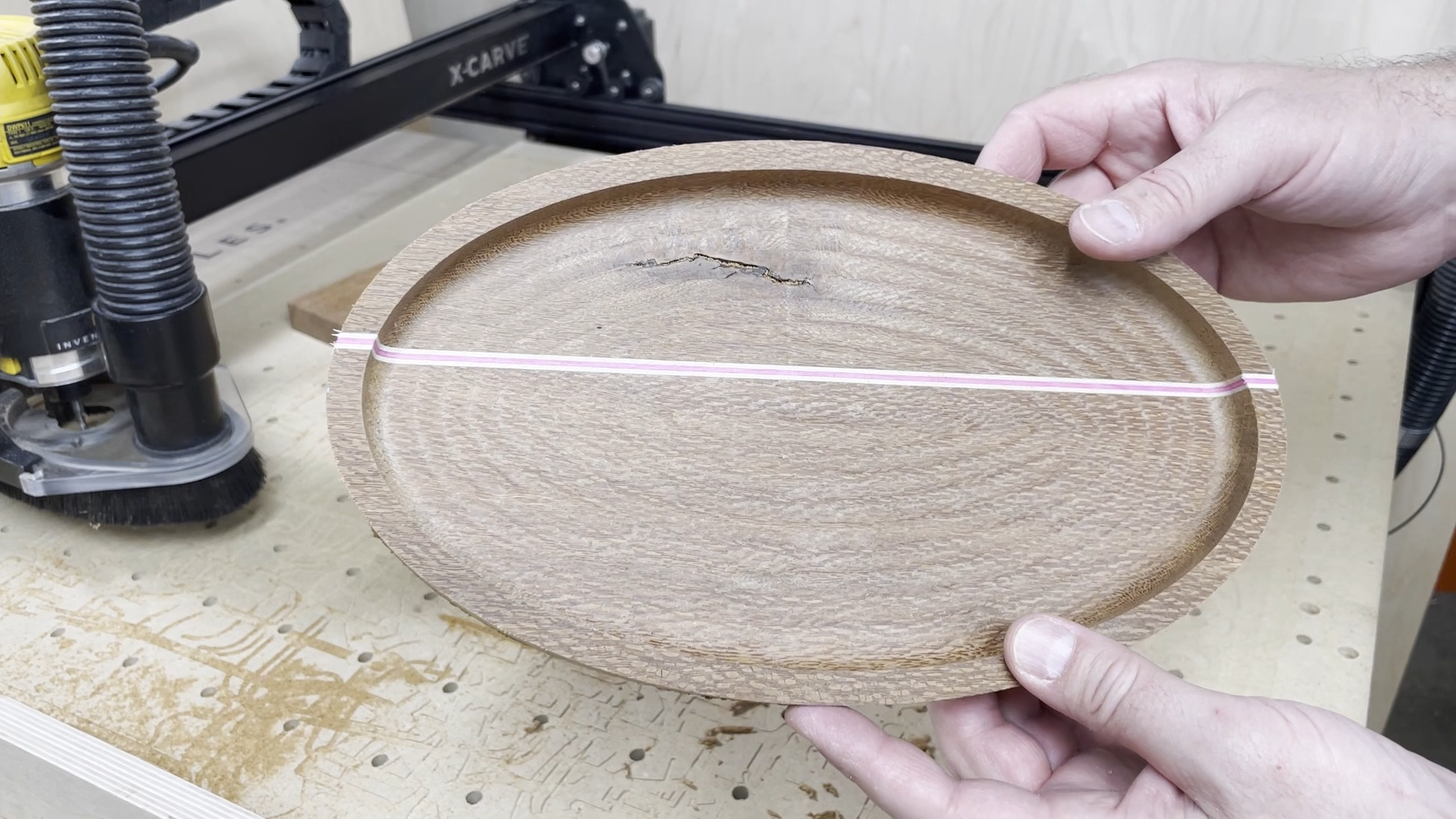
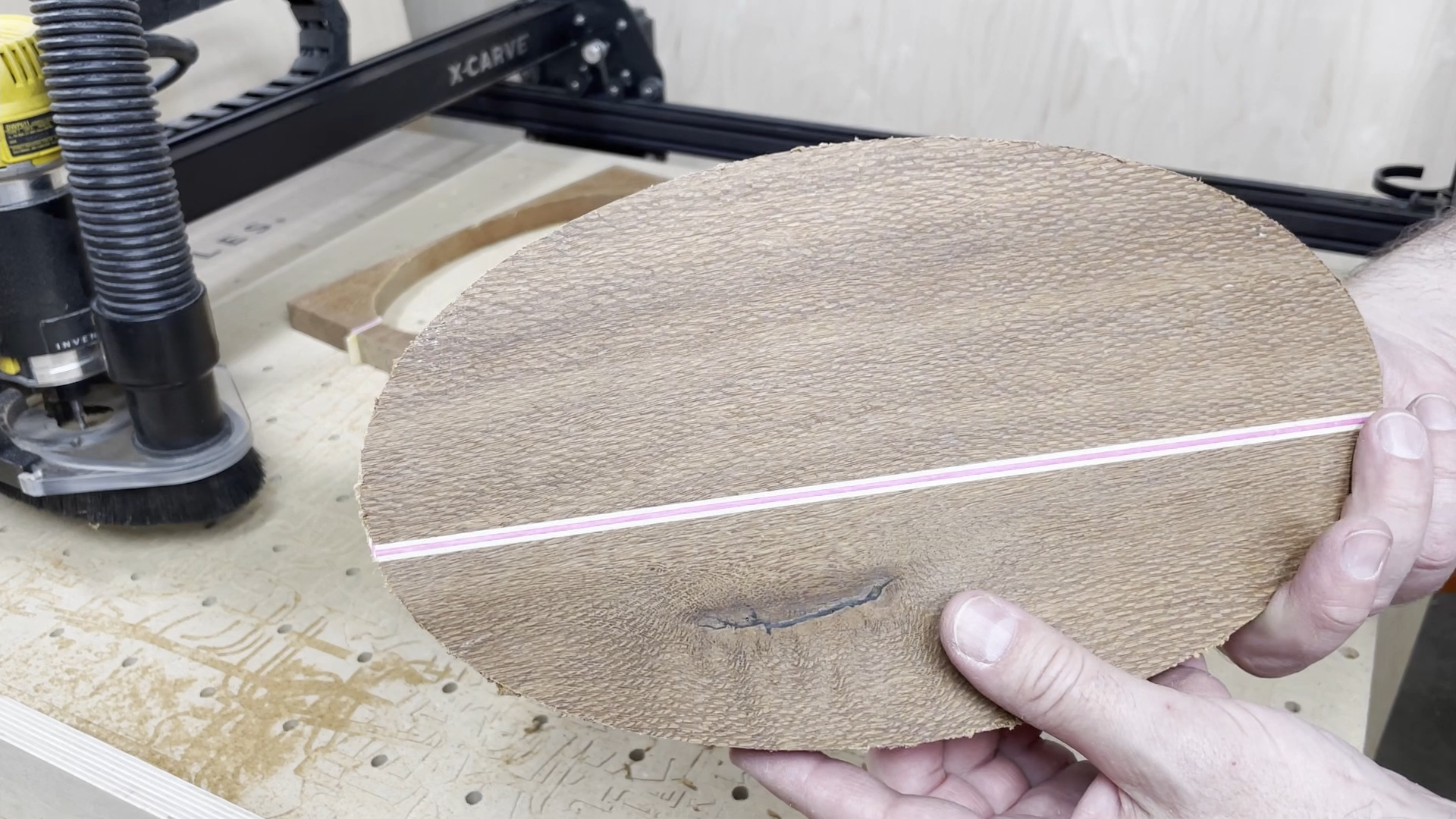
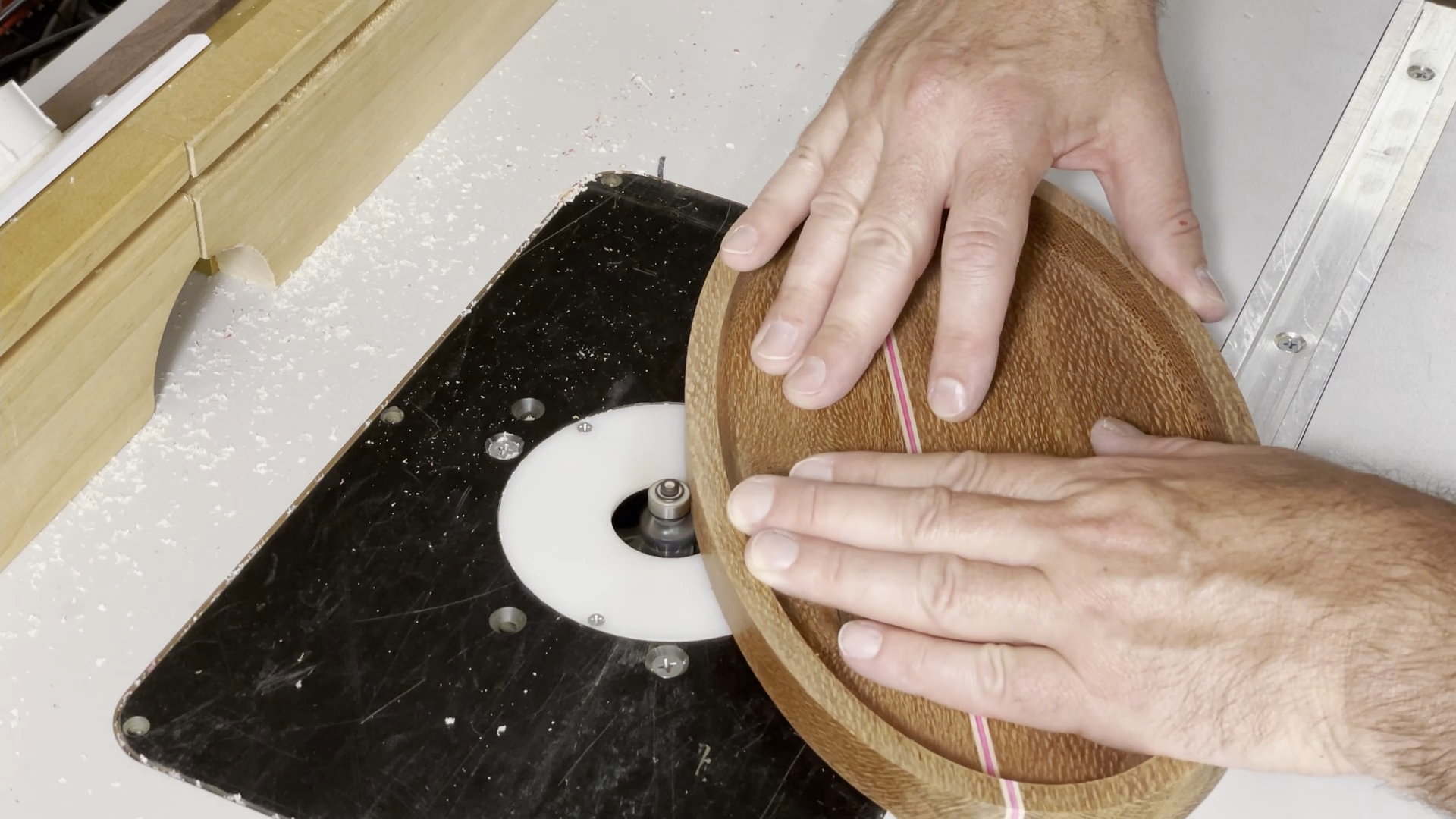
Step 6: Sanding and Finish
Sanding is not one of my favorite things to do. In making trays like this I would recommend getting some of the 2" diameter disc sanding attachments for your drill. They are great for sanding down the inside of your trays. See a link for these in my Tools and Materials section.
I usually sand down to 220 grit as that seems to take out most of the tool marks. The level you sand your trays down to will really depend on the type of finish you are going with. You will need to make the call here.
For the finish on these trays I decided to use a spray on lacquer. It goes on easy and in about 30 minutes, depending on temperature and humidity, you can add another coat. In my case I could flip the piece over and add the spray lacquer to the other side fairly fast.
I end up adding three coats to get to the desired coverage and smoothness.
I used Minwax clear spray lacquer with satin finish.
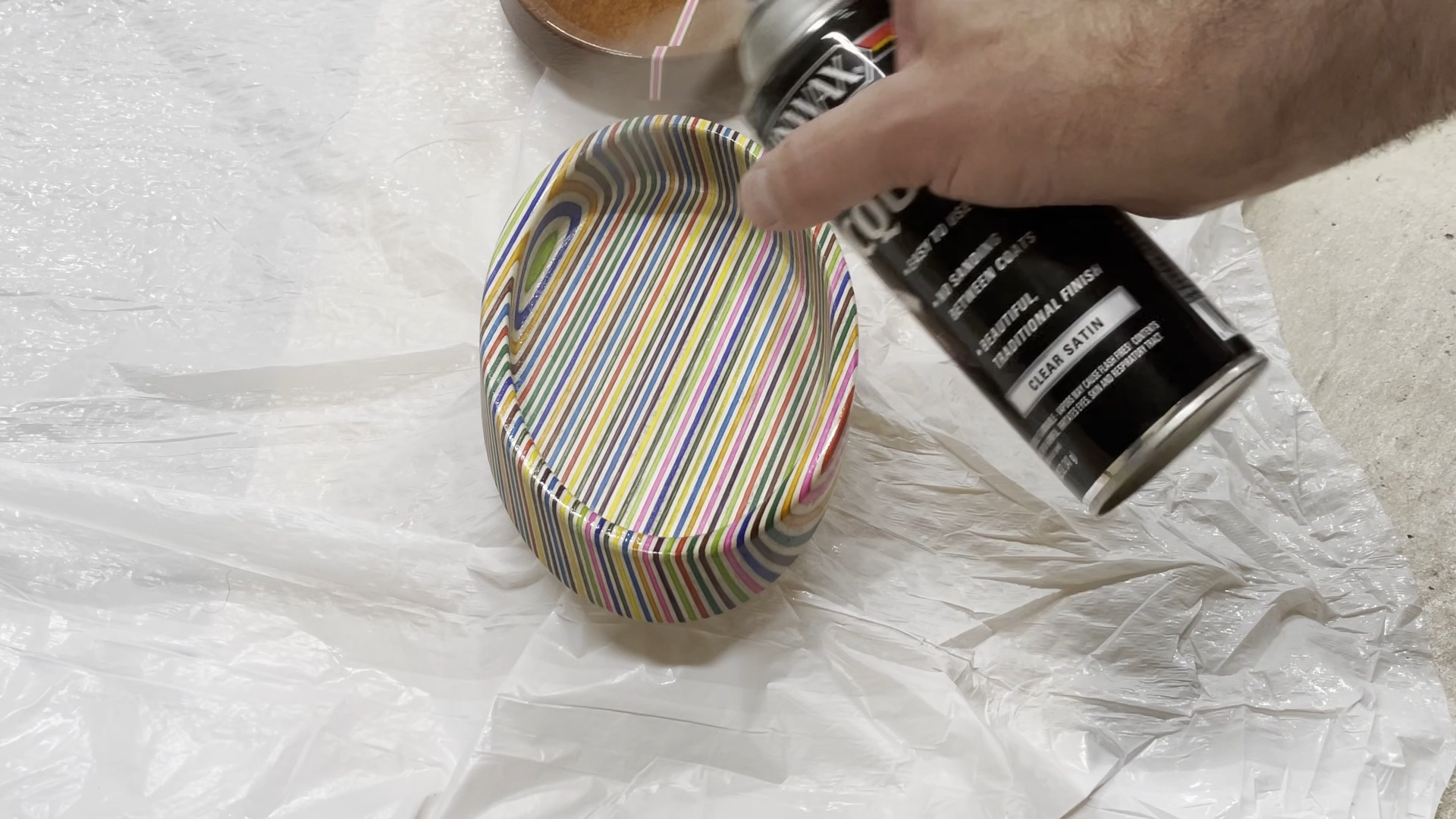
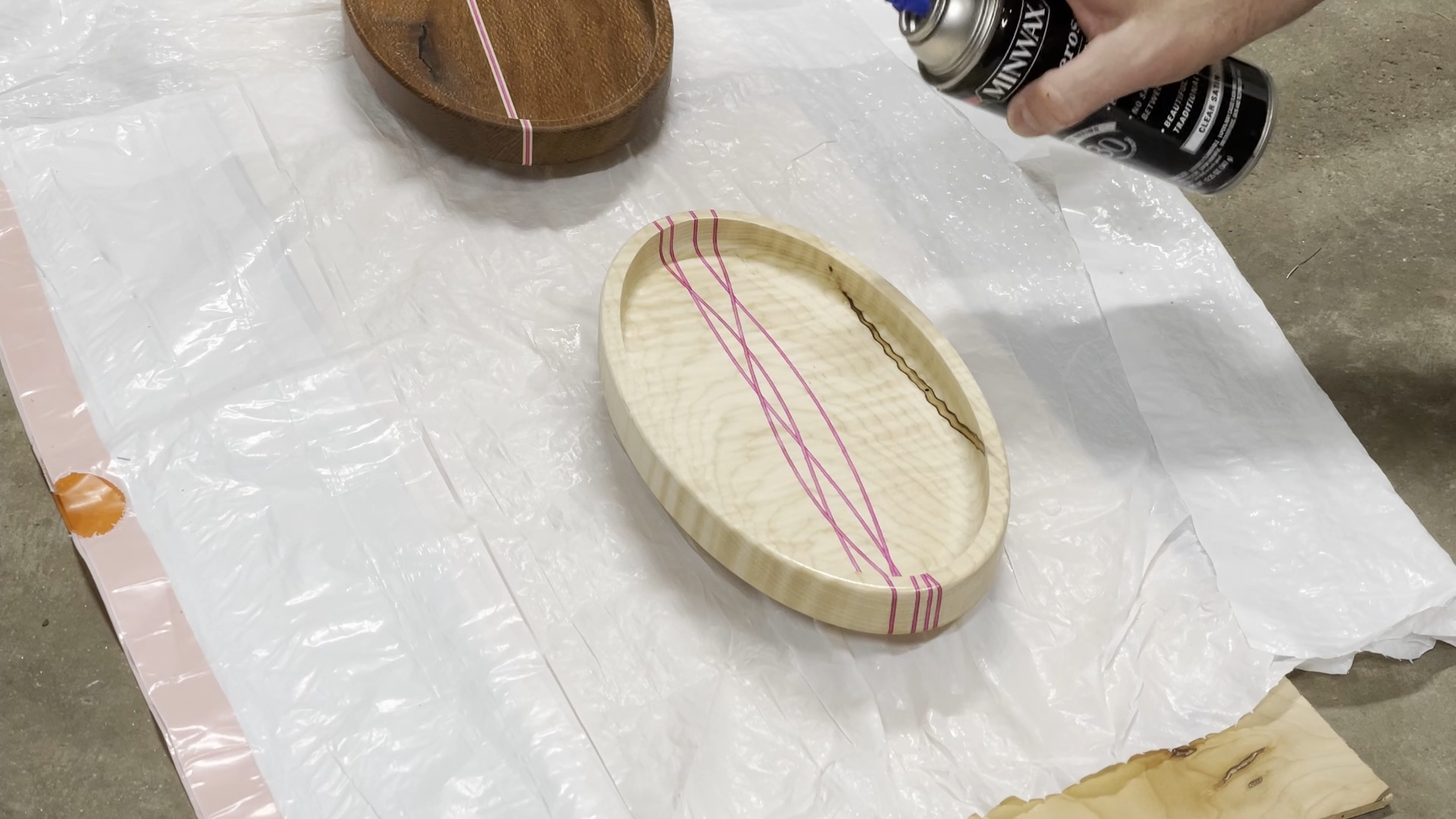
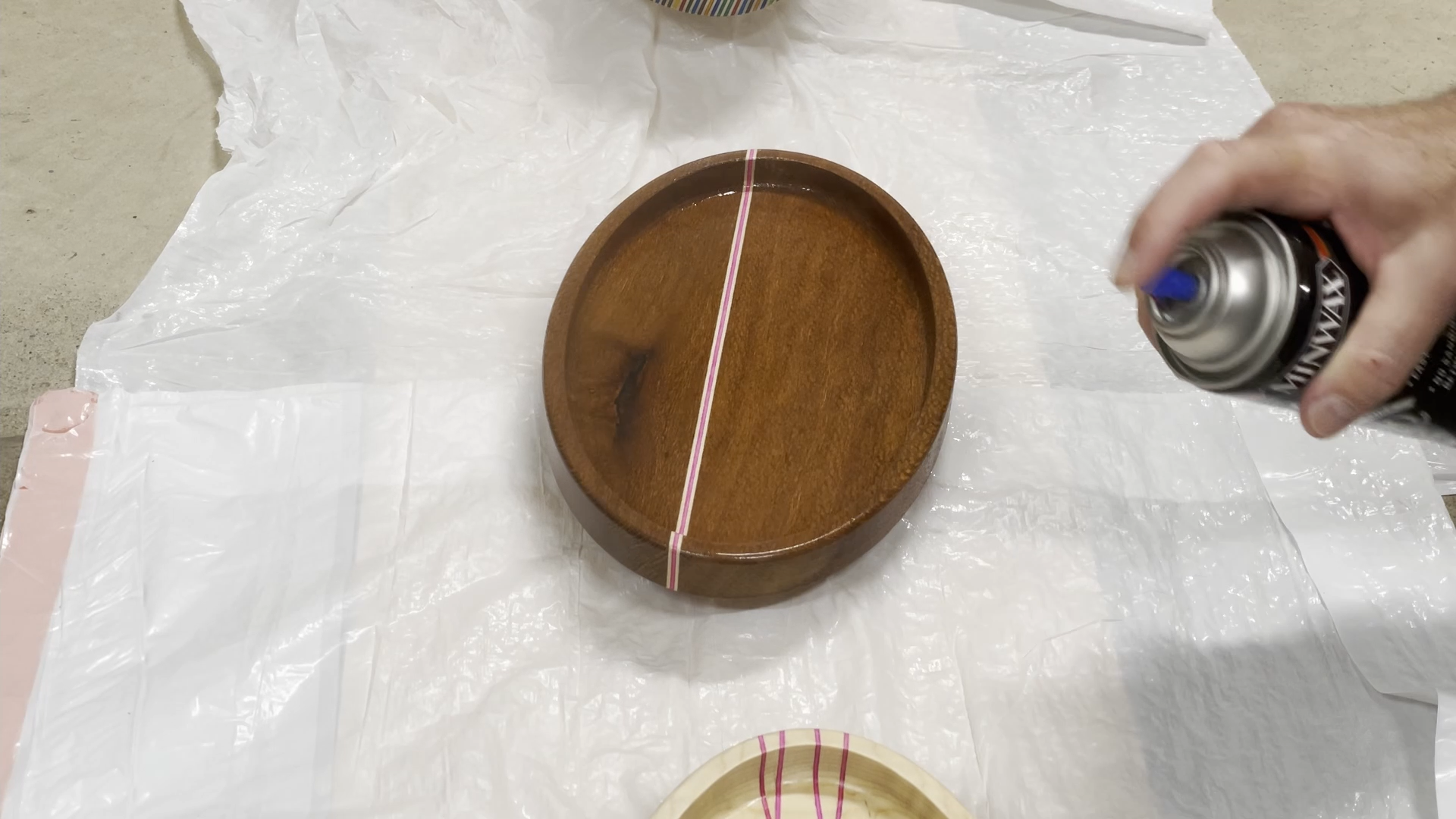
Step 7: Final Thoughts
Easel Pro software from Inventables is great for making things like these trays and it is very easy for people to start using no matter what skill level they area at.
The trays are nearly identical in shape, but have a very different look based on the three different types of wood blanks that are used.
Of the three different trays, I think I like the curly maple with the pink dyed veneer strips the most. The pink really stands out against the lighter maple. Most people I talked to liked this tray the best as well.
The multicolor tray is a close second. Someone did mention to me that this tray reminds them of Fruit Stripe gum. Does anyone else feel that way?
I hope you got something out of this project. If you use anything in this information then please drop me a line and let me know what was helpful.
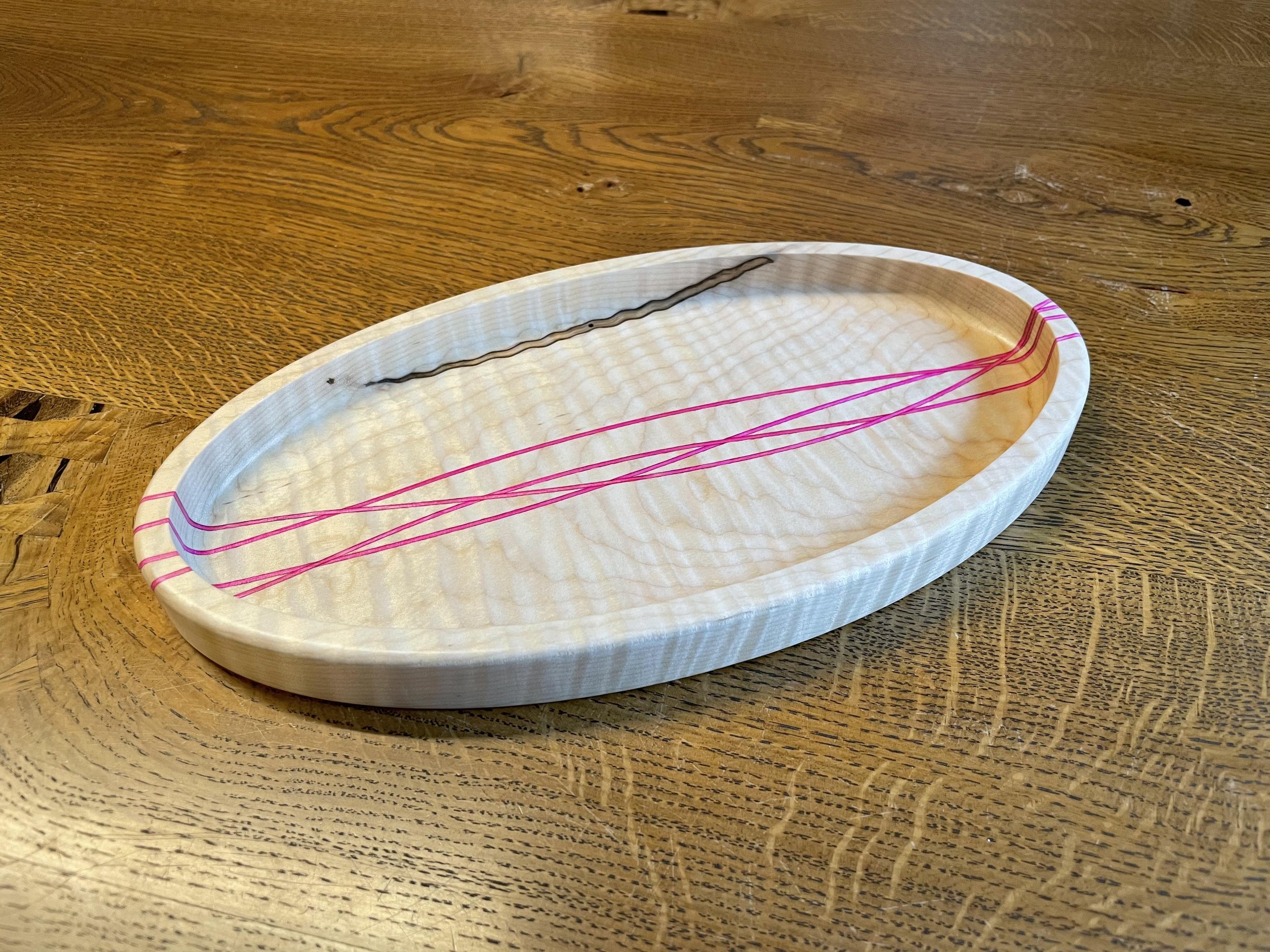
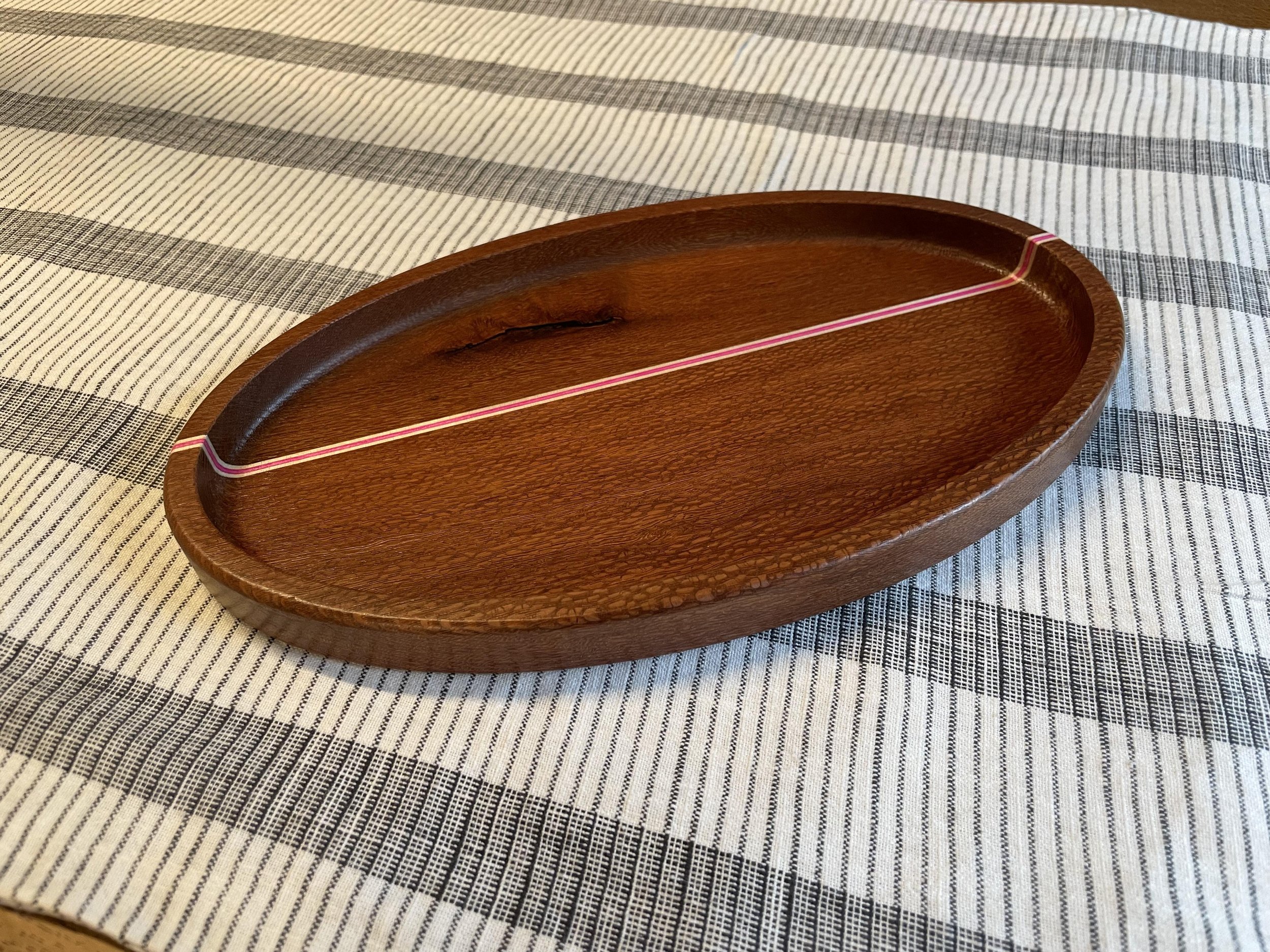
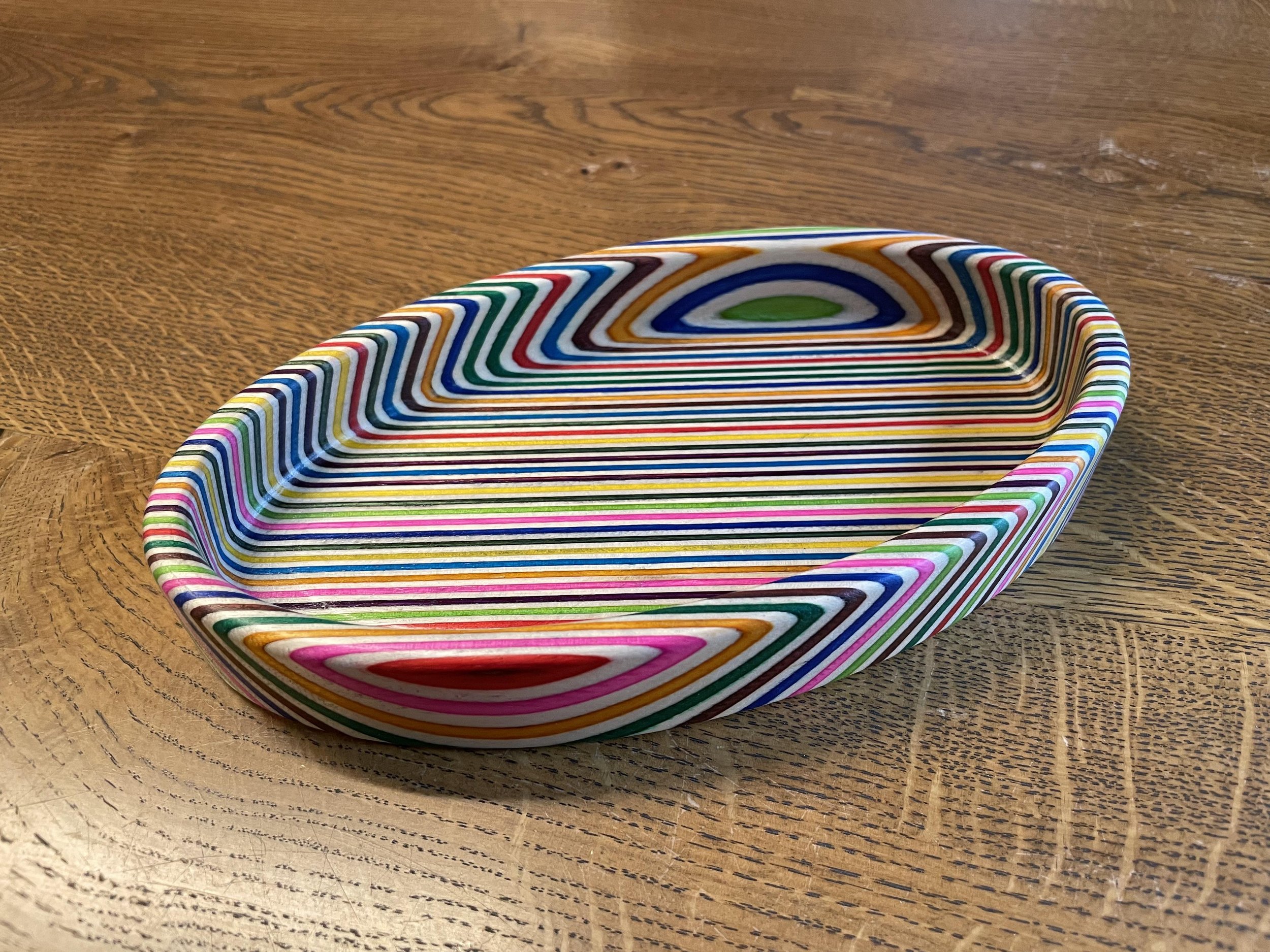